注塑成型是一种制造工艺,它将熔融的材料注射到模具中,以生产部件。这种工艺可使用不同的材料,,如热塑性塑料、聚合物或弹性体。熔融材料通过漏斗被送入桶中,在那里被加热、熔融和混合。然后将其注入模具。凝固后,材料占据模具的型腔形状。注塑工艺广泛用于大批量生产,因为其产生相对低的废料产量并且具有高的可重复性。
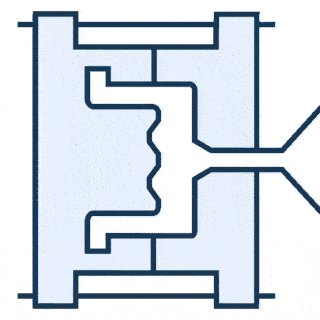
注塑成型工艺的通用性要求更广泛的设计考虑。大部分设计考虑因素将在制定产品要求后在模具上做出。影响设计的一些因素包括:零件将如何使用(单一产品或用于装配)、其尺寸和机械要求以及其承受化学品或压力等因素的能力。下面探讨了设计注塑时需要考虑的一些重要技巧。
仔细选择适合您的设计的材料
不同的材料提供不同的特性。例如,一些注射成型材料提供比其它材料更多的尺寸稳定性。类似地,一些与粘合剂的结合比另一些更好。材料设计考虑以下因素:温度、压力、生物和化学相互作用。热塑性树脂可大致分为非晶和半晶。尽管半结晶热塑性塑料提供了更好的耐化学性和电阻,但它们的非晶对应物的尺寸稳定性和耐冲击性要高得多。材料选择会影响所需的公差等级或某些特征(如壁厚)。
在Xometry,我们提供各种注塑材料,包括塑料、弹性体和硅橡胶。
考虑零件公差
模具通常以严格的公差准备,通常具有高达0.005 mm的CNC公差。但随着塑料冷却,发生收缩,这取决于材料。一些聚合物比另一些收缩得更大。例如,尽管可以预期PLA的最大收缩率为0.5%,但PEEK的收缩率可能高达1.5%。在设计零件和应用公差时,务必考虑收缩,并考虑所用材料的类型。
选择合适的壁厚
以下是不同材料的推荐壁厚:
- ABS: 1.143 mm - 3.556 mm
- 乙缩醛: 0.762 mm - 3.048 mm
- 丙烯酸: 0.635 mm - 12.7 mm
- 液晶聚合物: 0.762 mm - 3.048 mm
- 长纤维增强塑料: 1.905 mm - 27.94 mm
- 尼龙: 0.762 mm - 2.921 mm
- 聚碳酸酯: 1.016 mm - 3.81 mm
- 聚酯: 0.635 mm - 3.175 mm
- 聚乙烯: 0.762 mm - 5.08 mm
- 聚苯硫醚: 0.508 mm - 4.572 mm
- 聚丙烯: 0.889 mm - 3.81 mm
- 聚苯乙烯: 0.889 mm - 3.81 mm
- 聚氨酯: 2.032 mm - 19.05 mm
此外,墙壁应该均匀厚。不均匀的壁厚会导致凹陷痕迹。沉痕是由于较厚部分的缓慢冷却造成的局部表面凹陷。尽可能保持壁厚均匀。然而,当不可避免地具有不均匀的壁厚时,厚度差不得大于标称厚度的15%。我们还建议使用渐缩或平滑过渡。
为设计添加拔模角度
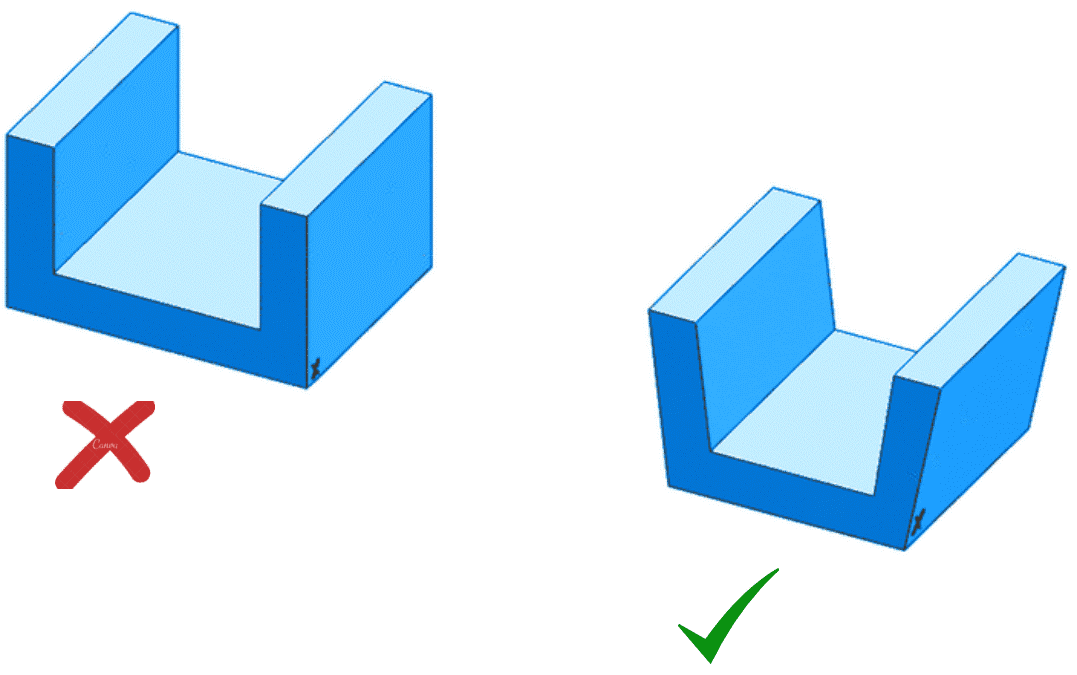
许多材料移除过程(如数控加工)可产生垂直壁。然而,创建具有垂直壁的用于注塑成型的零件将导致该零件在冷却时收缩而卡住,特别是在芯部。如果施加过大的力来顶出零件,则损坏顶出销甚至模具的风险变得非常高。设计墙壁的部分与轻微倾斜,以避免这一问题。这种倾斜叫做拔模。
由于它在设计中造成的高度复杂性,拔模通常会在零件设计的最后阶段加入。不同的曲面需要不同的拔模。有纹理的表面需要最大的拔模。注塑成型中常见的一些表面及其最小拔模角度如下。
- 对于“接近垂直”的要求:0.5°
- 最常见的情况:2°
- 所有关闭面:3°
- 具有浅纹理的面:3°
- 具有中等纹理的面: 5°
为某些零件添加肋和角撑板
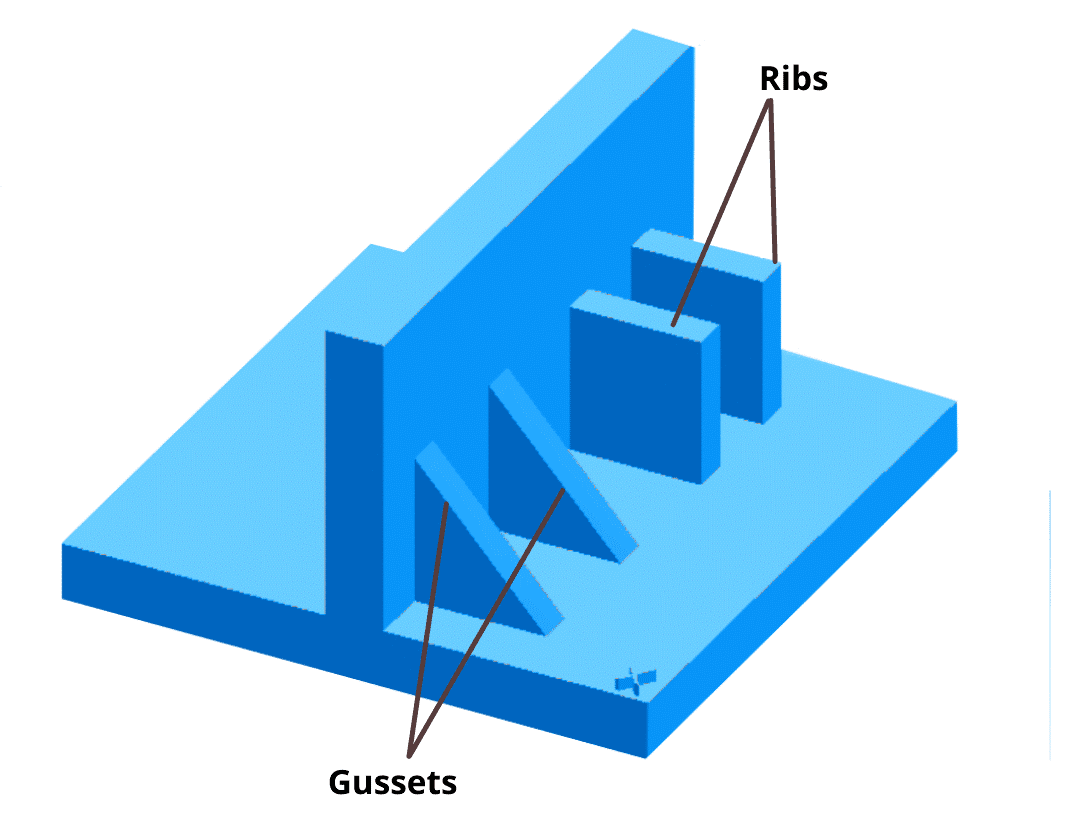
某些部分需要加强筋。加强筋和角撑板为零件提供额外的强度,并有助于消除外观缺陷,如翘曲、凹陷和空洞。这些特征对于结构元件是必不可少的。因此,优选将它们添加到零件中,而不是增加零件的厚度以增加强度。
然而,如果设计不当,这可能导致收缩。当某些零件的冷却速度比其他零件快得多时,就会发生收缩,导致某些部分永久弯曲。通过将肋的厚度保持在它所附接到的壁的厚度的50%至60%之间,可以有效地减少翘曲。
为零件设计添加半径和圆角
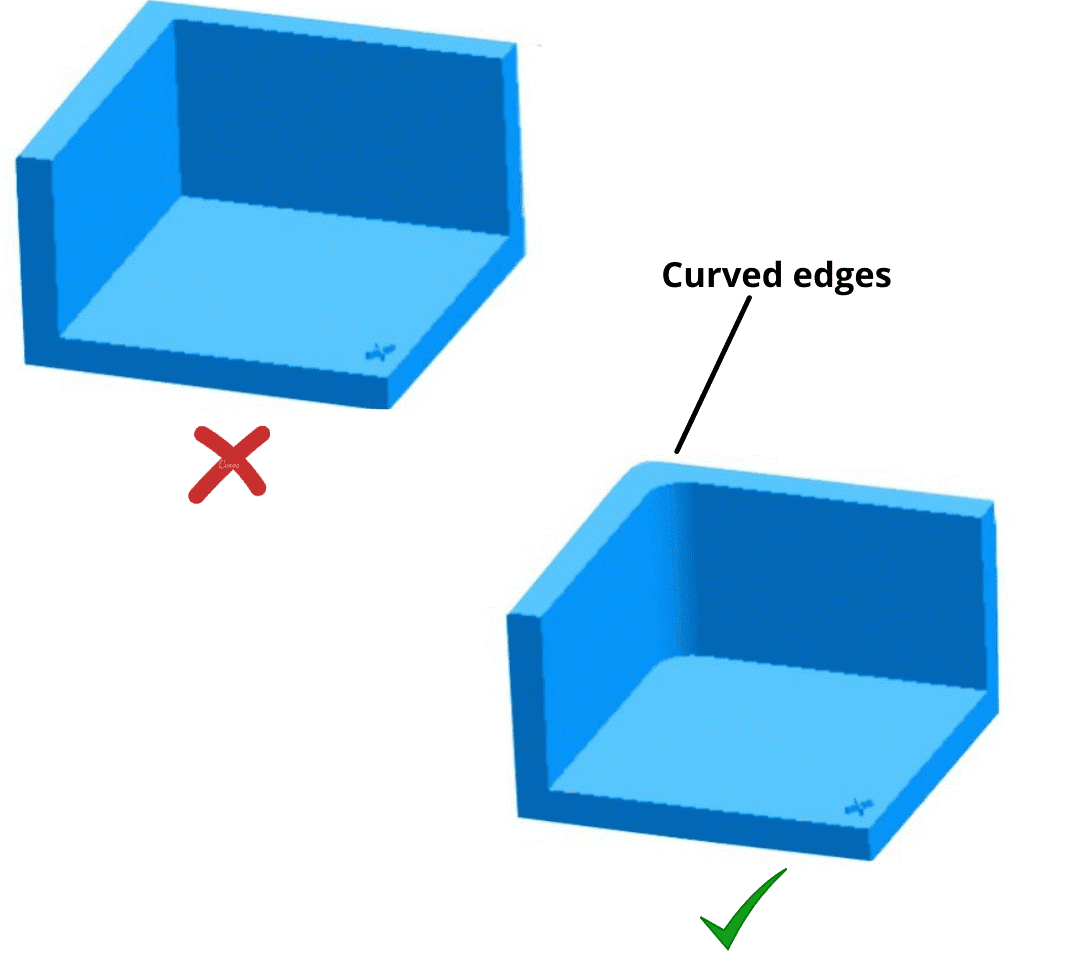
在可能的情况下,对零件应用半径可以消除尖角,从而改善材料流动和零件的结构完整性。当熔融材料流过拐角或进入拐角时,尖锐的拐角会导致零件的薄弱。尖角不可避免的地方只有分型面或关闭面。
半径和圆角也有助于零件顶出,因为倒圆的拐角在脱模过程中比尖锐的拐角更不容易卡住。此外,尖角在结构上也是不可取的,因为它们会导致可能失效的应力点。半径有助于消除拐角处的应力。
此外,在零件中包含尖角会成倍增加生产成本,因为这将需要模具具有尖角,而这只能使用非常昂贵的制造技术来实现。始终将内半径的最小值加上0.5T,外半径加上1.5T,其中T是零件的厚度。
为零件添加按扣配合
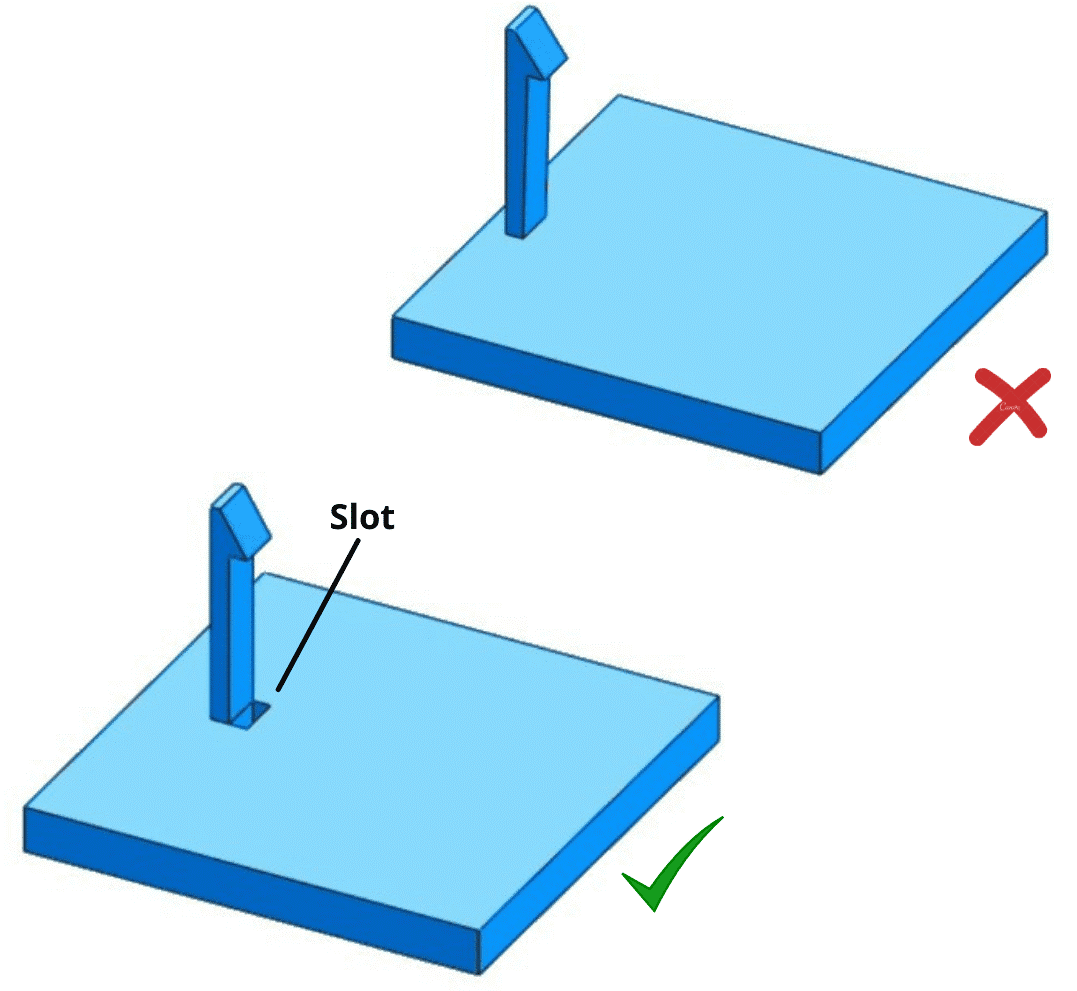
搭扣配合可通过底切获得。由两个半部组成的直拉模具是最直接的设计,不适合制造具有底切特征的零件。这是由于难以用数控加工这种模具以及材料在脱模时卡住的趋势。底切通常使用侧芯创建。然而,侧芯显著增加了加工成本。幸运的是,这里有一些设计提示,可以在不使用侧芯的情况下实现底切功能。一种方法是引入一个槽来代替。
这也称为传递核心。另一种方法是调整或移动零件的分模线。进行此操作时,也相应地调整拔模角度。移动分模线最适合位于零件外部的底切。也可以使用剥离底切,也称为凸块。然而,只有当零件在从模具脱模的过程中具有足够的柔性以变形和膨胀时,才能使用此特征。
此外,给足够的间隙:颠簸必须有一个30至45的提前角,以有效脱模。所有这些昂贵的侧核的替代品都需要对零件进行重大重新设计。如果由于可能影响零件的功能而无法重新设计零件,则必须使用滑动侧动作和核心来处理底切。这些特征在模具关闭时滑入,打开时滑出。侧芯必须垂直移动并具有适当的拔模角度。
将凸起连接至侧壁或肋
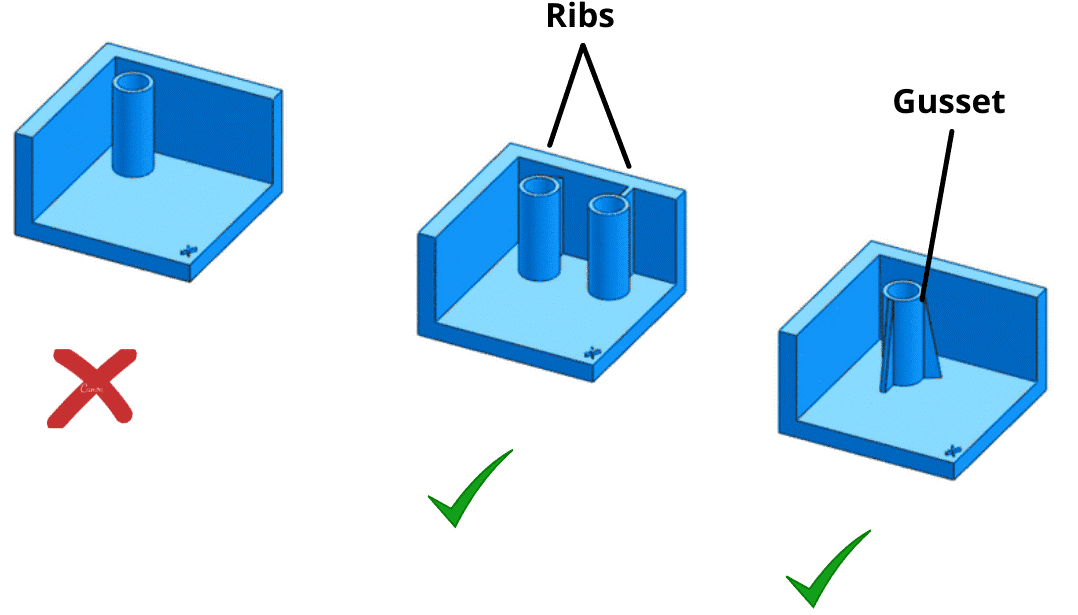
凸起是模制到零件中的圆柱形特征,用于接收销、插入件或自攻螺钉,以用于组装或安装零件。这些要素不应是独立的。务必将凸耳连接到侧壁或肋上,以确保零件的结构完整性。对于自攻应用,凸起的外直径应为螺钉直径的2.5倍。
选择正确的闸门位置
闸门是进入部分,熔融材料通过它进入模具。闸门的错误放置可导致材料在模具的不同部分中的不均匀流动。这将导致形成称为流动线的条纹或图案。
除了策略性地放置浇口之外,增加注射也可确保遍及模腔的均匀流动。始终在零件上预留闸门,闸门不会影响零件的功能或美观
Xometry的注塑服务
我们提供30多种材料的注塑服务,如塑料、合成橡胶和硅酮橡胶以及弹性体。只需转至我们的报价引擎,上传您的型号并选择您的零件首选项,即可获得即时报价。
推荐阅读:注塑成型服务