如果您的设计日益复杂,本指南将提供清晰、结构化的方法,确保零件按规格生产,同时避免不必要的成本和延迟。您将学习如何评估设计的复杂性、发现优化机会,并与制造商有效协作以确保零件符合要求。
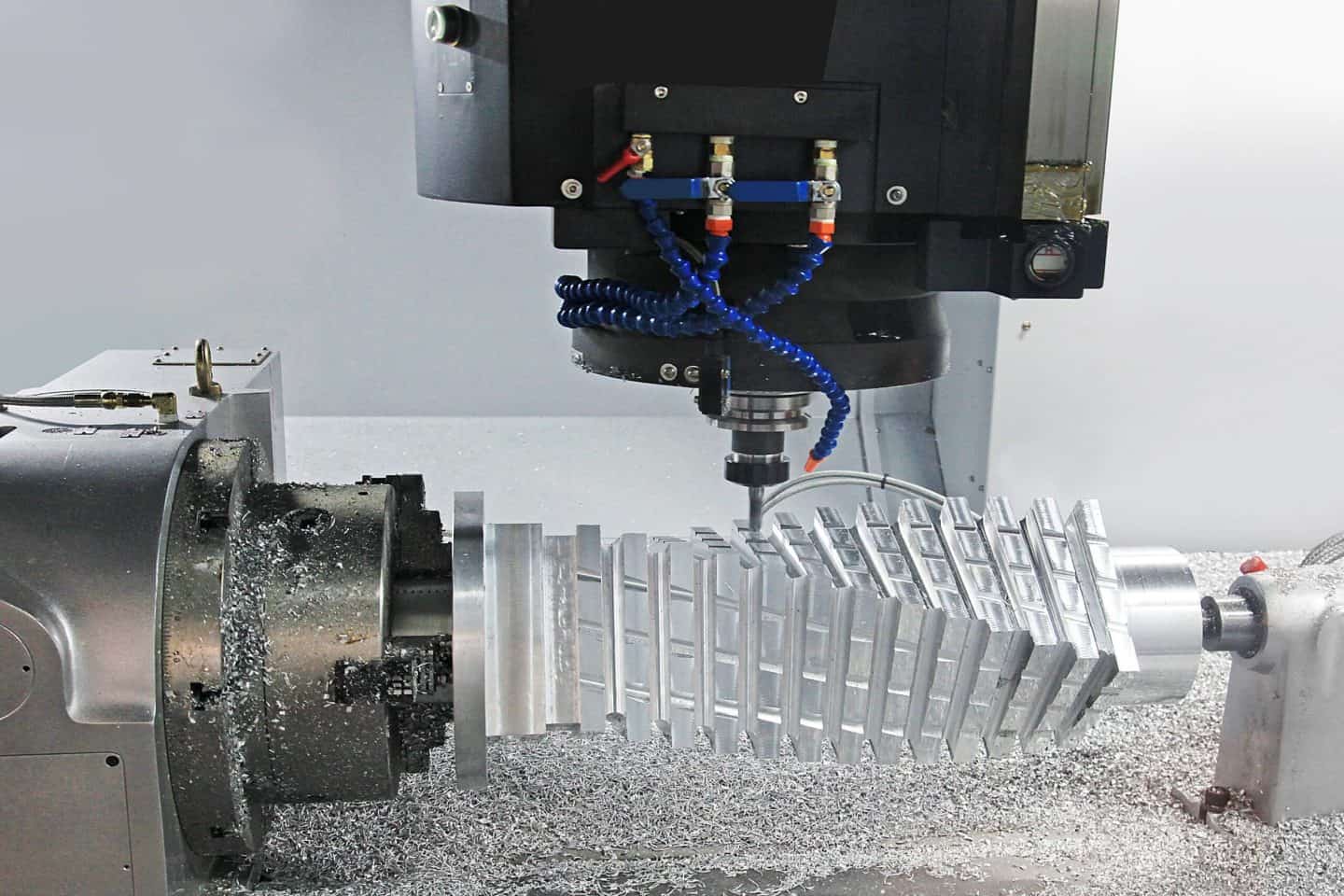
CNC加工因其先进功能,包括多轴操作、精密刀具和与复杂软件的集成,而在生产复杂零件方面表现出色。这些特征使其能够加工传统方法难以或无法实现的复杂几何形状、内腔和底切。
从航空航天领域的带复杂冷却通道的涡轮叶片,到医疗领域的定制骨科植入物,再到电子产品的精密外壳,CNC加工通过提供精度和效率助力各行业创新。其能够无缝切换切削工具并利用CAD/CAM系统,确保了高精度和适应性,成为原型开发和大批量生产的理想选择。
本指南提供了应对复杂零件加工挑战的全面方法。它将帮助您评估设计复杂性、挖掘优化潜力,并实施简化生产的策略。遵循这些步骤,您可以在高效满足规格的同时,最大程度降低成本并避免生产延误。
第1步 您的设计真的复杂吗?
在寻求解决方案之前,请先评估零件是否真的复杂,或是否存在简化设计的可能。使用以下检查清单评估:
- 零件是否有薄壁或细高结构?
金属材料壁厚低于0.8mm或塑料低于1.5mm的薄壁易变形,可能需要专用夹具或降低切削速度。 - 是否包含深孔?
深宽比超过3:1的孔会导致刀具偏斜、热量积聚和排屑问题。 - 是否存在难以触及的内腔或底切?
这些结构需要长柄刀具、多轴加工或EDM等替代工艺,增加成本和时间。 - 是否涉及复杂曲面几何?
曲面或复杂表面通常需高级编程、五轴机床和多道工序,延长加工时间及成本。 - 是否有微米级特征或极小圆角?
小于2.5mm的特征或尖锐内角需专用刀具和技术,增加复杂性及刀具磨损。 - 零件是否体积庞大?
大型零件(通常>1000mm或超出标准CNC机床工作范围)需要专用设备、稳固夹具和谨慎搬运。热膨胀和加剧的刀具磨损需温控和频繁换刀。 - 是否存在切削中断或窄槽?
刀具接触不均或窄槽会导致磨损和表面质量问题,需精心规划刀路。 - 是否全尺寸标注严苛公差?
全严苛公差会增加成本和时间。建议仅将高精度要求应用于关键特征上。
若勾选多个选项,恭喜——您确实遇到了复杂零件!但别担心!我们将探讨如何优化设计并简化制造,同时保持其功能性。
Ryan Stevens
机械工程师和技术撰稿人
材料选择也会影响加工难度钛合金或淬火钢等高硬度材料会加速刀具磨损,需降低切削速度;不锈钢等高韧性或低导热性材料需特殊排屑和散热策略。材料刚性还可能增加刀具负荷和振动,需加强夹具。
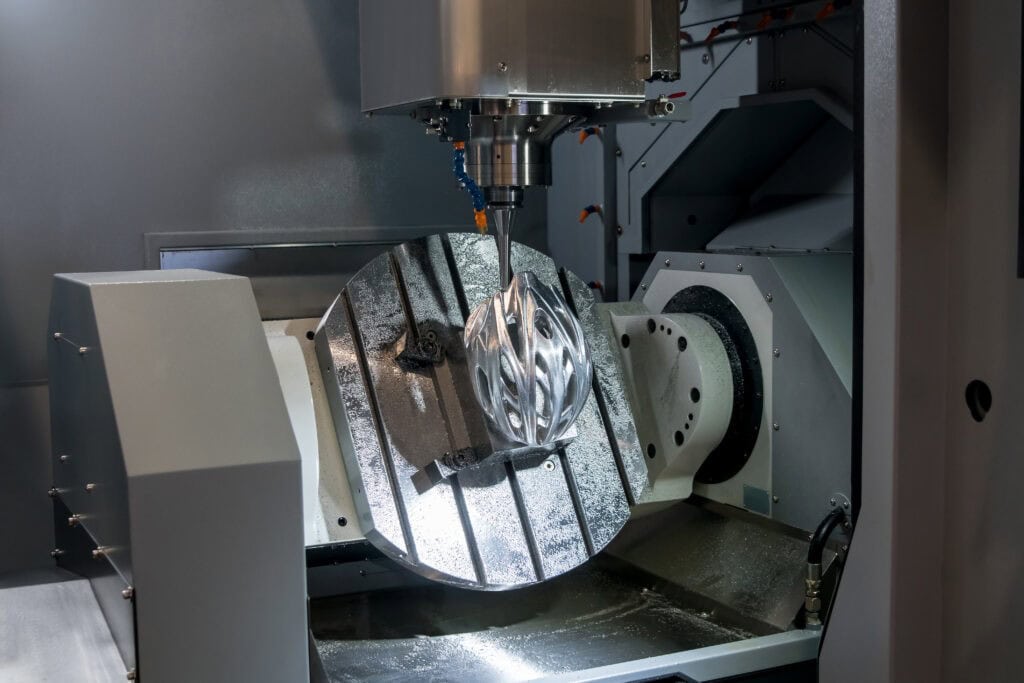
金属加工五轴高速加工中心
第2步 您的设计可优化吗?
在确认零件复杂度后,下一步需思考如何优化设计以提升可制造性。以下提供可操作建议与软件工具,在保证功能性的同时简化生产流程:
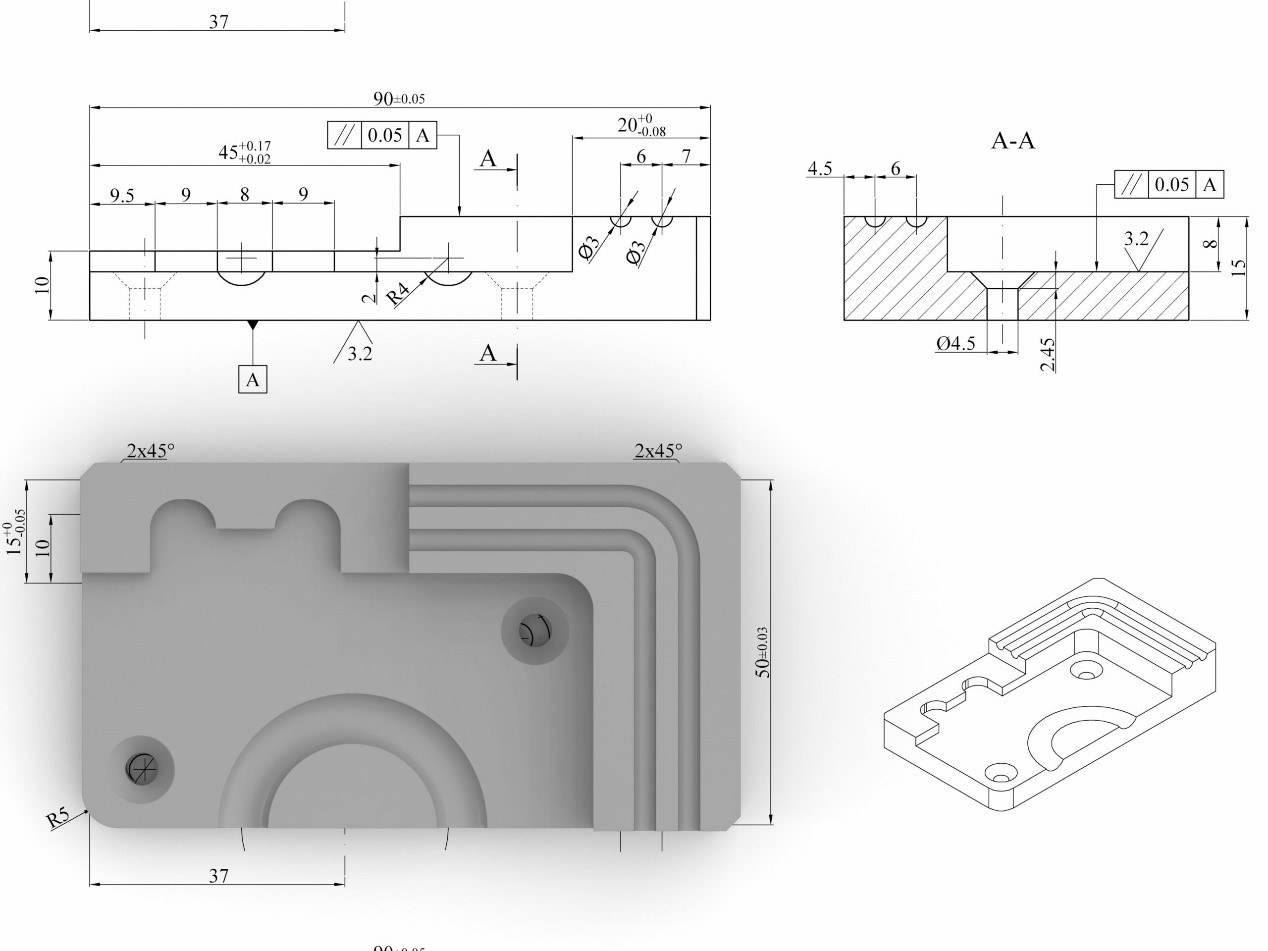
1. 简化壁厚与深腔特征
低于推荐值的过薄壁厚在加工中易因切削力发生变形,导致精度偏差和刀具损坏。深腔特征会导致刀具可达性受限、排屑困难以及热量积聚,这些问题会增加加工时间与风险。简化此类特征可提高材料稳定性,减少刀具磨损,从而实现更高加工效率。
具体做法:
- 设置最小壁厚:金属为0.8mm,塑料为1.5mm以避免出现偏转。
- 保持型腔深度与宽度比在3:1以内以获得更好的可达性和间隙。
- 使用CAD软件SolidWorks或AutodeskFusion360模拟优化。
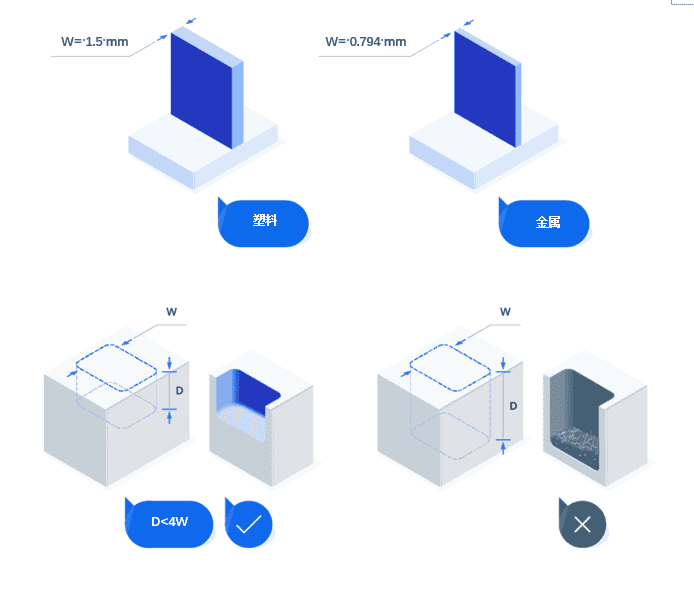
2. 优化复杂几何形状和表面特征
复杂几何形状,如例如自由曲面或曲线几何体需使用五轴机床和多道工序,增加时间与成本。加工此类特征时刀具磨损更高,且需专用编程,性价比低。
具体做法:
- 用简单几何体替代过度复杂的特征。
- 在早期阶段应避免使用浮雕商标或装饰性元素——这些可以通过后处理阶段再添加,以减少材料去除量和加工时间。
- 使用CAM软件,如HyperMill或Mastercam生成高效刀具路径,减少设置变更并提高加工精度。
3. 减少内腔与受限可达特征
内腔与内凹结构限制刀具移动,从而难以使用标准刀具加工。此类特征通常需要用到定制刀具、额外的设置或其他工艺,如电火花加工(EDM),这些都会导致成本和时间的增加。
具体做法:
- 将零件分成模块,单独加工后再组装。
- 针对无法避开的内腔,使用加长刀具并通过Fusion360优化加工策略。
- 对极难加工的区域,考虑采用非传统方法,如EDM。
4. 避免极小尺寸特征
对于标准CNC刀具而言,加工小于2.5mm的特征结构具有挑战性,这类加工需要使用磨损速度快的微型刀具,且主轴转速需降低。此外,超精密微特征结构通常需要借助高精度的检测和验证手段,这进一步增加了生产复杂度。
具体做法:
- 对零件进行重新设计,在可行范围内去除小于2.5mm的微型结构特征。
- 通过SiemensNX或SolidWorks等模拟工具验证重新设计后的结构功能性。
- 对于无法规避的微特征,建议采用微放电加工或激光切割等特种加工工艺替代传统方法。
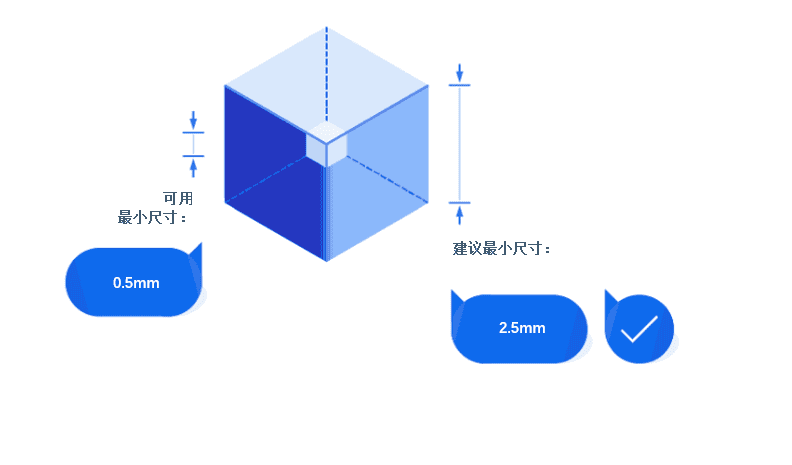
5. 保持内部圆角半径的一致性
尖锐的内角需要更小型的刀具,这类刀具更容易发生断裂和磨损。不统一的半径还会在零件中产生应力集中点,可能引发结构薄弱。保持半径一致可实现更顺畅的切割,减少刀具磨损,从而提高加工效率和零件耐久性。
具体做法:
- 设计拐角时确保圆弧半径至少达到刀具半径的130%。
- 利用Fusion360内置的设计规则,自动调整拐角半径以保障可制造性。
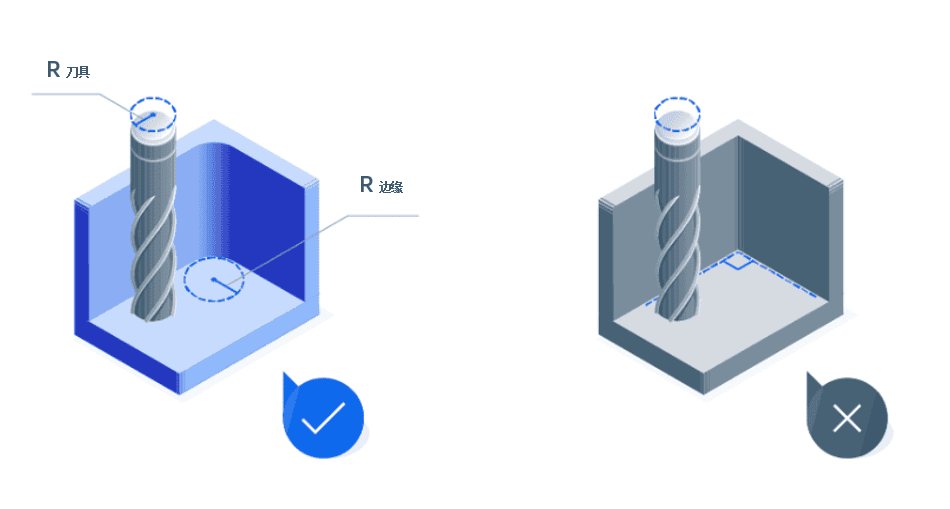
6. 选择标准孔径尺寸、螺纹长度及合理孔位布局
非标孔径尺寸、过长螺纹设计和不当孔位布局会增加加工时间和复杂度。确保孔位正确对齐并遵循行业标准可简化刀具需求、改善加工可达性并降低成本。
具体做法:
- 采用标准孔径和螺纹规格,螺纹长度控制在直径1.5倍范围内以保证最佳加工效率。
- 沿机床轴线对齐孔位以优化刀具可达性并减少偏转。
- 避免在边缘或薄壁附近开孔,防止加工变形。
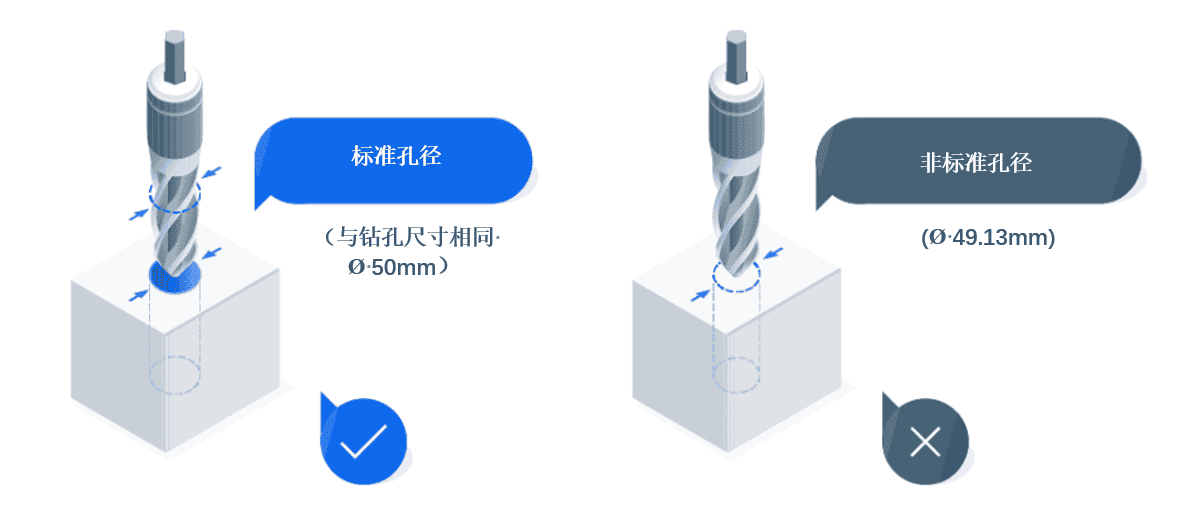
7. 选择性应用公差
在整个零件上,甚至是非关键特征位置设定严格公差要求将增加加工时间、刀具磨损和检测成本。这也将极大地提高生产成本。通过仅在功能区域或关键部位实施严格公差控制,既可确保必要精度要求,又能在非关键区域有效节省时间和成本。
具体做法:
- 仅对配合/关键表面或对齐点等特征应用严格公差(例如±0.01mm)。
- 对于非关键区域,使用标准公差,例如ISO 2768中的中等或精细级别。
- 在Creo或SolidWorks中使用GD&T工具分析并优化公差标注位置。
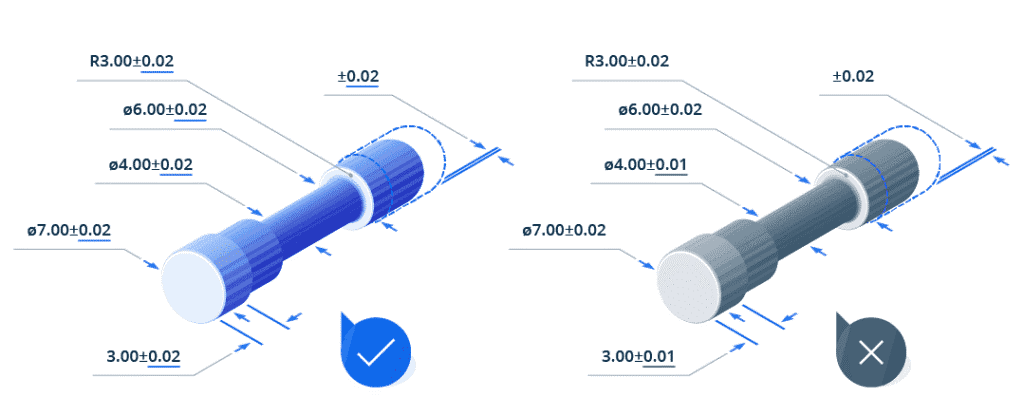
第3步 如何帮助制造商?
通过确保设计文档清晰且具备可制造性,您可以减少误差和延期的风险。此外,了解制造商的运作方式,例如其在不同材料和机床类型上的加工能力,能帮助您做出更明智的设计决策。这种方法不仅能提高项目效率,还能确保最终零件完全符合您的规格要求。
提供完整的CAD模型
CAD模型是零件制造的蓝图。如果尺寸、公差或标注不清晰或缺失,制造商将被迫进行假设,可能导致错误或延误。为确保精度和效率,请遵循以下最佳实践:
- 包含所有相关细节,如公差、材料厚度和表面处理要求。
- 对螺纹、配合表面或需后处理的区域等关键特征进行清晰标注。
- 使用STEP或IGES等兼容格式文件,以便轻松导入CNC编程软件。
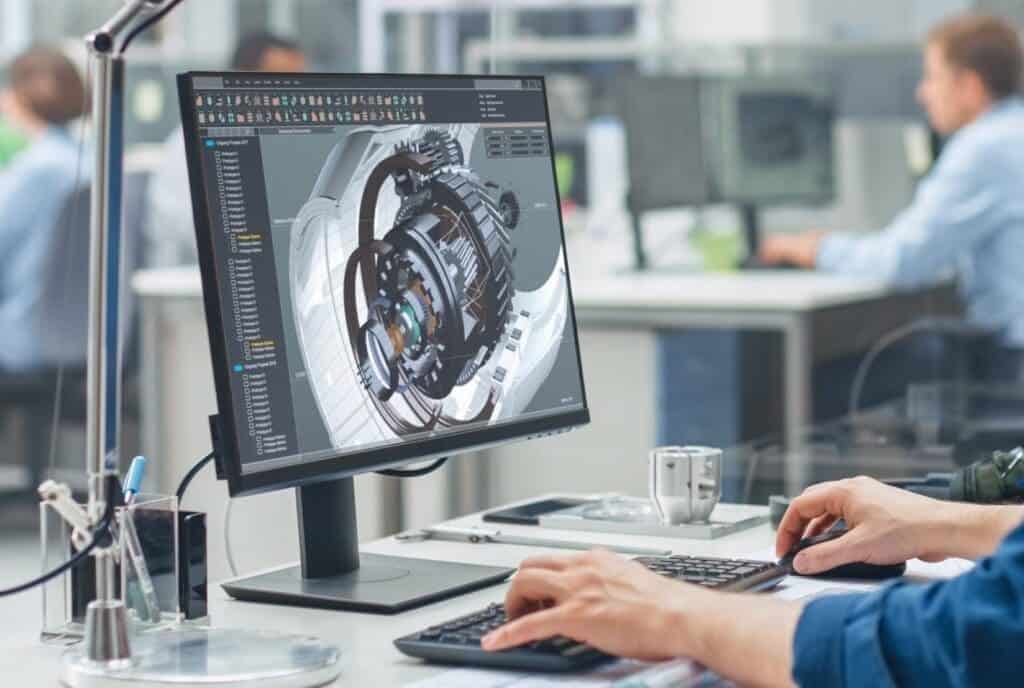
工程师正在使用CAD软件进行机械部件设计
尽可能使用标准特性
复杂的CNC加工零件通常具有复杂的几何形状、严格的公差、多材料组合,有时尺寸较大,往往需要多轴加工和先进工艺才能完成。下表概述了CNC加工中关键复杂性因素的概况,说明了这些因素对产品设计、可制造性、成本及整体加工难度的影响。
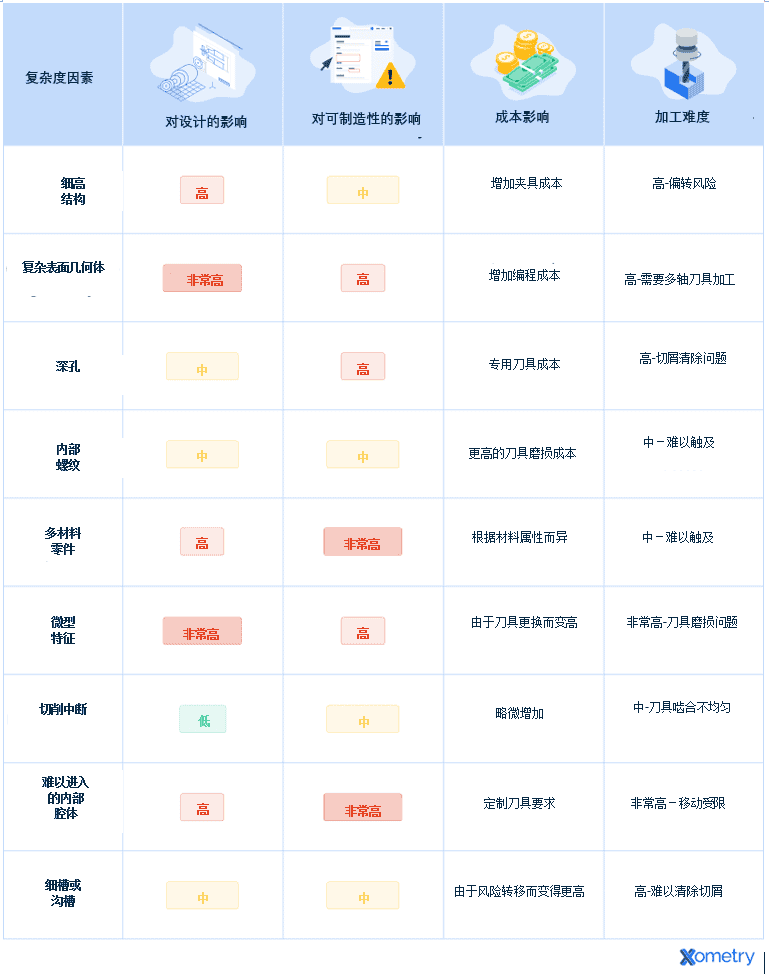
第4步 复杂零件的最佳CNC加工替代方案有哪些?
尽管CNC加工通用性强且高效,但某些复杂零件或几何结构若仅依赖CNC技术,可能面临加工困难或效率低下。此时需考虑采用更适配特定加工难点的替代技术。下文列举当CNC加工达到能力极限时可用的关键替代方案。
技术 | 描述 | 优势 |
增材制造(3D打印) | 通过逐层堆积材料来制造零件,非常适合制造结构复杂且高度精细的零件。 | 适用于复杂的内部结构、轻量化零件及快速原型制作。包含多种技术(如MJF、SLA等),每种技术均有其独特优势。 |
电火花加工(EDM) | 通过电火花放电蚀除材料,擅长加工硬质材料和复杂细节。 | 尤其适用于尖锐棱角、深型腔或难以触及的特征加工。 |
混合制造(如CNC加工与切割) | 结合CNC加工与激光或等离子切割技术,制造具有精密几何形状和复杂切口的零件。CNC加工负责铣削与成型,激光/等离子切割用于高精度切割或轮廓加工。 | 通过高精度加工与高效切割的融合,为复杂轮廓和形状提供更强的灵活性。通过整合多个工艺到单一工作流程中,减少制造步骤和交付周期。适合需要精细切割和高精度机械加工的零件。 |
铸造 | 将熔融材料浇注到模具中,以形成所需形状。 | 具有高性价比的大批量生产方案,且能实现复杂的内部空腔结构。 |
注意:在Xometry择幂科技,我们提供铝和塑料的铸造服务,但不提供钢的铸造服务。 |
根据上表,增材制造擅长创建复杂的内部结构,而EDM和激光切割则更适合加工精密且难以触及的特征。铸造是大批量生产复杂零件的理想选择,而混合制造则提供了灵活结合多种技术优势的能力。通过理解这些替代制造方法的优势和局限性,工程师可以选择最佳方案来高效生产复杂零部件。
确保复杂零件制造成功的关键
如果您不知从何开始,获取实时报价是一个良好的开端。如果制造成本令您惊讶,这通常表明仍有优化空间。然而,如果模型中复杂的线条、孔洞、螺纹和边缘表明它本就需要高成本,那么值得用最先进的设备将您的设计变为现实。
请务必确保每一个细节都清晰地体现在您的模型、图纸以及对制造商的其他要求中。