挑战
宝马在其唯一一家位于美国南卡罗来纳州的制造工厂,在涉及到制造和组装每一个部件,从发动机到装饰等美学细节,拥有着不可逾越的技术质量和高重现性。
该公司对于装饰、标志、徽章,和对准,特别是在生产装配过程中使用高度定制的夹具。然而,与汽车表面的复杂曲线相匹配的数控加工工具生产成本非常高,尤其是在较小的体积下更是这样,并且需要很长的交货期。
为了以更低的成本制造适形工具,宝马在2016年开始将3D打印和真空复模结合到他们的工装组件中。然而,通过创建混合了多种制造过程的工具,工程师开始花费几乎四分之一的工作时间,或每周10小时,采购零件和管理供应商。工装设计工程师Ryan Lambert开始寻找一个多工序制造商谁可以创造短期运行或一次性零件为他们的定制夹具,并从采购管理的过程中节省时间。
Xometry定制夹具
Lambert很快找到了Xometry实时报价引擎℠(Xometry Instant Quoting Engine℠),并在多个制造过程中上载和引用了他的定制零件。Xometry庞大的制造合作伙伴网络提供了一个单一来源的平台,宝马可以在几分钟内报价和订购一个专门的汽车装配夹具。
对于夹具的部分,保持和应用修剪或贴花直接,Lambert使用Xometry的3D打印服务。制造夹具的附加工艺,如SLA、SLS和FDM允许创建特定的几何形状,通过保持它与车辆的曲线齐平,安全地夹紧、插入和压下装饰。以前,一个非共形CNC加工的零件需要保持距离,这可能会导致应用不精确。使用3D打印还有助于使工具更轻,因为它用超轻填充塑料取代了以前加工的零件。
为了制造对准工具,Lambert设计了结合3D打印、CNC加工和碳纤维零件的工具。这些工具在装配过程中对准车辆的各个部分,每天可达数百次。通过使用3D打印和碳纤维,该部件减轻了25-50%的重量,并减少了工人每天数百次举起沉重工具的疲劳。
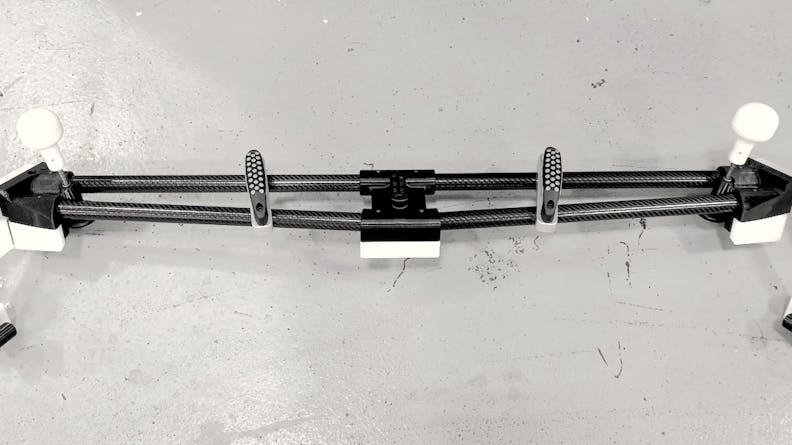
它可以用碳纤维油管、CNC加工的塑料和金属零件以及3D打印的Ultem组件快速且经济有效地开展生产
宝马团队还使用了Xometry的真空复模能力,以创造夹具车身外壳。在模制聚氨酯中制造小体积工具外壳提供了比CNC加工更耐用和更便宜的解决方案,也允许设计和制造适合其他定制组件的定制几何形状。
Xometry对Lambert和他的团队的另一个关键好处是能够与Xometry工程师及时交流,并确保零件以制造为目的进行优化。Lambert说:“Xometry有一个很棒的团队,支持我完成所有的项目,无论是设计或材料建议,还是在进入制造之前发现问题。”
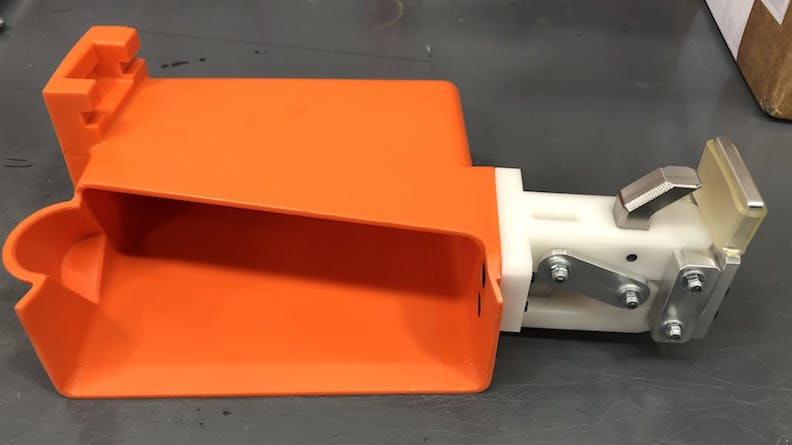
“Xometry择幂科技对宝马来说太棒了,因为我可以在一次上载中上载我的定制工具的完整组装,然后为每个零件配置独特的材料和工艺。”
Ryan Lambert,
宝马工装设计工程师
使用Xometry提供的更快、更价廉、更可靠的定制解决方案
自2016年开始与Xometry择幂科技合作以来,Lambert与Xometry择幂科技合作设计和制造的多材料、多工艺夹具组件取得了成功。由于Xometry择幂科技可以为其网络中的多个制造合作伙伴提供组件(分别专注于3D打印、CNC加工和真空复模的合作伙伴),它可以为宝马提供有竞争力的市场价格,为公司节省高达25%的定制夹具费用。通过其广泛的制造选择,Xometry择幂科技允许宝马测试新的生产解决方案,而不局限于宝马内部提供的工艺。
随着Xometry择幂科技作为管理每个合作伙伴的单一来源供应商,宝马工程师现在可以每周将多达10个小时的时间返回到设计和测试等增值活动中。刀具可靠性也提高了,应用误差率从10%下降到4%以下。这是现在工具轻了25-50%的结果,这意味着工人现在可以用稳定的手每天举起它们数百次。
“Xometry择幂科技使得工作更加轻松和专业。他们负责执行,所以我不需要与供应商周旋或对其进行管理。我们只需采购即可,Xometry择幂科技负责其余的。”
Ryan Lambert,
宝马工装设计工程师