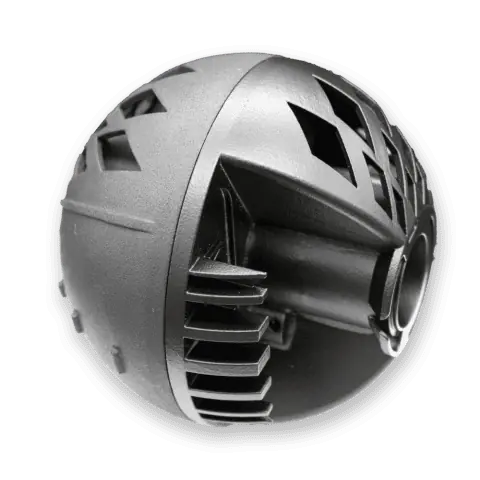

工业级3D打印服务
Xometry择幂科技为原型设计和批量生产零部件提供优质3D打印服务,最快 3天内完成。
我们有能力通过树脂光固化成型 (SLA), 激光烧结成型 (SLS), 惠普尼龙多流射熔融成型 (MJF) , 热塑性材料熔融沉积成型 (FDM), 金属激光烧结成型 (SLM)等工艺来生产部件。
3天内完成快速3D打印
5种3D打印工艺在线服务
超过70种材料可选
Xometry择幂科技庞大的制造网络涵盖了中国及海外10,000多家制造商。凭借多项3D打印工艺以及超过七十种制造材料,可提供您所需的生产能力,助您进行原型设计和生产。
Xometry择幂科技一站式按需制造服务的优势
专业团队支持
无论是初期的设计检查到下单后与制造伙伴的顺利沟通,我们提供经验丰富的完整制造团队确保订单顺利进行。我们提供DFM(可制造性设计)反馈及改进建议,以优化您的零件和生产流程。
严格质量保证
Xometry择幂科技已通过 ISO 9001:2015 认证。庞大的制造伙伴网络、专业的内部工程师团队和特设的质量检测实验室确保我们运送的每个定制部件都具有一流的质量。
庞大制造网络
Xometry择幂科技拥有超过10,000家制造伙伴遍布全球30多个国家,具有不同的制造能力及资质认证,随时满足不同的产能需求,快速投入生产。我们的制造网络严格遵守保密协议,保护客户隐私。
快速交付制造
Xometry择幂科技为绝大多数亚洲国家/地区提供定制零部件。立即上传设计图纸,获取定制零部件实时报价,填写您的送货地址并完成下单,我们将尽快为您生产交付。
灵活采购流程
Xometry择幂科技为可靠的企业客户提供灵活的付款选项、多种满足您需求的付款方式以及针对特定价格和数量建立框架协议的能力,从而确保成本可预测性和更简化的采购流程。
认证检验报告
Xometry择幂科技可以提供各类客户所需的证书(符合订单要求的金属和塑料原材料证书、热处理协议、RoHS 证书等)及各类检验报告(CMM、首件检验报告 - FAIR、测量报告等)。
3D打印材料
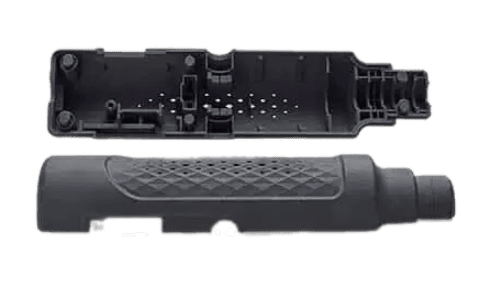
刚性塑料
- 8100-SLA
- 8220-SLA
- 8360X-SLA
- 9400E-SLA
- Ledo6060-SLA
- 高韧性类ABS-进口Somos-SLA
- Therm1-SLA
- TAURUS-SLA
- 黑色树脂-SLA
- P12进口材料-SLA
- PA12-SLS
- PA12 GF-SLS
- PA11-SLS
- PA6 GB/PA66-SLS
- PA2200-SLS
- 尼龙PA12-MJF
- 尼龙PA11-MJF
- HP TPU-MJF
- ABS-FDM
- ASA-FDM
- PA12CF-FDM
- PEEK-FDM
- PLA-FDM
- ULTEM1010-FDM
- ULTEM9085-FDM
- PC-FDM
- PETG-FDM
- PPSU-FDM
- PPS-FDM
- PC-ABS-FDM
- PC-PBT-FDM
- PC-FR-FDM
- PA6/66-FDM
- PA6-CF-FDM
- HPPA-CF-FDM
- HPPA-GF-FDM
- ABS-GF-FDM
- PET-GF-FDM
- PET-CF-FDM
- Victrex AM™ 200FIL-FDM
- WANHUA PA12-FDM
- BASF ULTRAFUSE® PPSU-FDM
- BASF ULTRAFUSE® PC/ABS-FR-FDM
- Kimya ABS-ESD-FDM
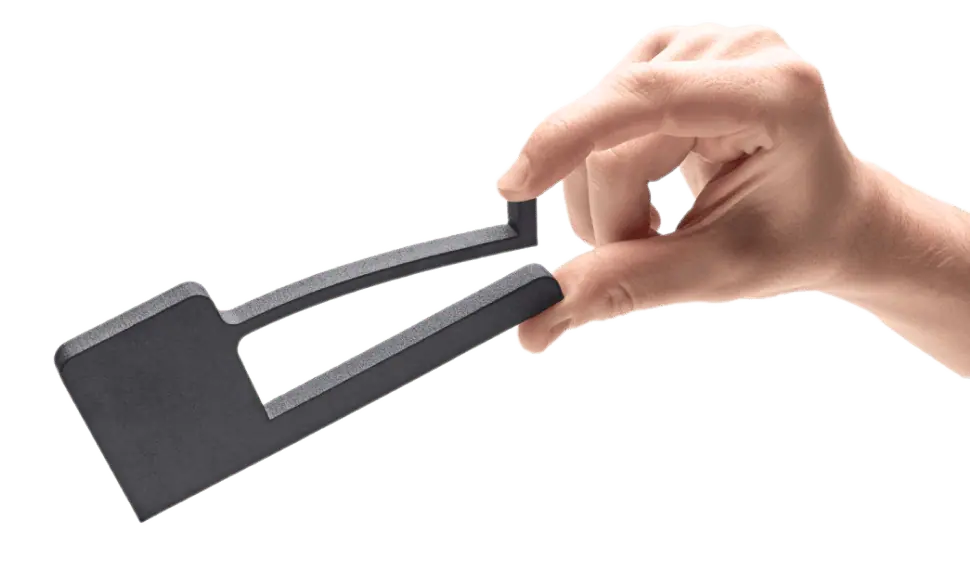
柔性塑料
- TPU 88A-SLS
- HP TPU-SLS
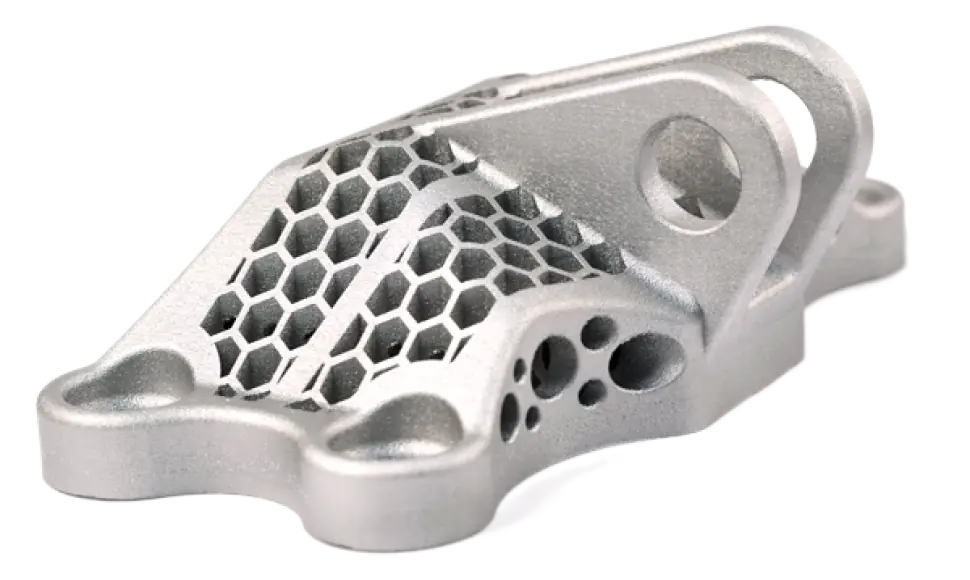
金属
- 铝合金-Aisi10mg-SLM
- 不锈钢-316L-SLM
- 钛合金-TC4-SLM
3D打印工艺对比
Use the dropdowns in each column to select and compare services side by side.
强大且实用的快速原型设计和小批量生产
|
高精度原型设计
|
强大且实用的快速原型设计和小批量生产
|
价格实惠、大尺寸设计需求
|
设计复杂的金属部件
|
---|---|---|---|---|
工艺简介惠普尼龙多射流熔融 (MJF) 3D打印是最广泛使用的工业增材制造工艺之一。与 SLS 一样,MJF通常用于生产坚固、实用的塑料部件。 | 工艺简介树脂光固化成型 (SLA) 3D打印工艺利用光固化热固性树脂来构建高精度、高分辨率的部件。其表面光洁度是业内最高标准之一,推荐用于美观的原型。 | 工艺简介激光烧结成型(SLS) 3D打印是最广泛使用的工业增材制造工艺之一。与MJF一样,SLS通常用于生产坚固、实用的塑料部件。 | 工艺简介热塑性材料熔融沉积成型 (FDM) 是一种3D打印技术,因能提供多种材料选择,精确度高,能够打印大型部件以及具有成本优势,而广为人知。FDM工艺的3D打印部件非常适合小批量生产和快速原型设计,通常无需进行任何后期处理。 | 工艺简介金属激光烧结成型(SLM) 3D打印工艺可以有选择地通过熔融铝或不锈钢及其他材质的细小金属粉末使来创建复杂的零部件。 |
交付周期4 日 | 交付周期3 日 | 交付周期5 日 | 交付周期4 日 | 交付周期6 日 |
最大制造体积380x380x284 mm | 最大制造体积1400x700x550 mm | 最大制造体积350x520x350 mm | 最大制造体积780x750x1000 mm | 最大制造体积420x420x450 mm |
公差0.3% | 公差0.3% | 公差0.3% | 公差0.5% | 公差0.2% |
标准层厚度0.08 mm | 标准层厚度0.02 mm | 标准层厚度0.1 mm | 标准层厚度0.25 mm | 标准层厚度0.05 - 0.1 mm |
是否可以实时报价是 | 是否可以实时报价是 | 是否可以实时报价是 | 是否可以实时报价是 | 是否可以实时报价是 |
最小特征尺寸 | 最小特征尺寸0.50 mm | 最小特征尺寸0.60 mm | 最小特征尺寸0.50 mm | 最小特征尺寸0.75 mm |
最小壁厚
| 最小壁厚
| 最小壁厚
| 最小壁厚
| 最小壁厚
|
优势
| 优势
| 优势
| 优势
| 优势
|
缺点
| 缺点
| 缺点
| 缺点
| 缺点
|
了解更多 | 了解更多 | 了解更多 | 了解更多 | 了解更多 |