大家好,我是NikoMroncz,Xometry择幂科技销售工程总监。自2010年起,我一直从事3D打印领域工作,而SLS始终是我的首选技术。这得益于其广泛的适用性、PA12材料的优异性能,以及极高的性价比。本文将分享关键技巧,助您设计出更坚固、精准且适合SLS3D打印的部件。
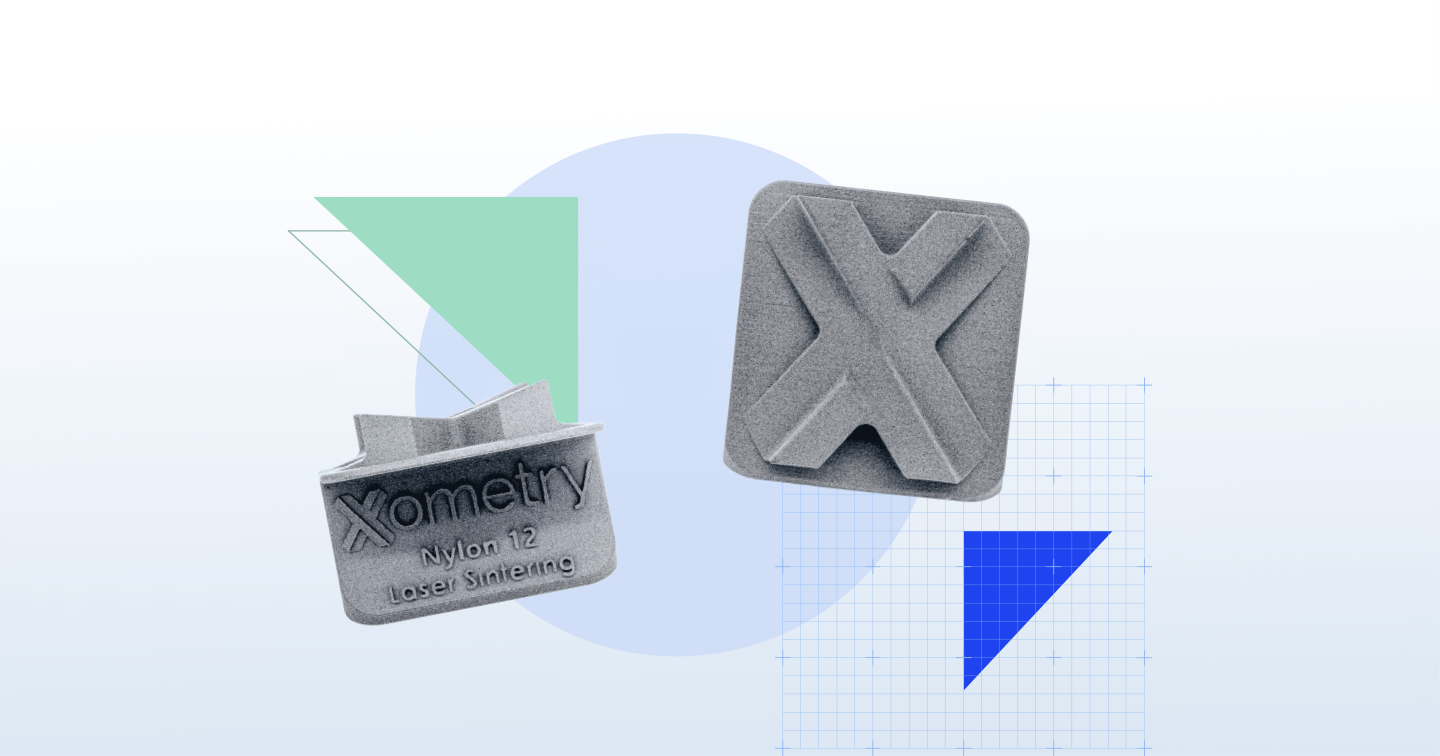
选择性激光烧结(SLS)是一种基于粉末的3D打印工艺,无需支撑结构即可制造复杂的高强度零件。因此,它成为功能性原型和终端应用产品的理想选择。SLS可实现卓越的机械性能,尤其在使用如PA12、PA11或增强复合材料(例如PA12玻璃填充)时更是如此。
与其他3D打印技术(如熔融沉积成型FDM)相比,SLS技术具有更高的设计自由度、更优的表面质量和各向同性的机械性能。此外,由于可在构建舱内嵌套排列多个零件,SLS尤其适合批量生产。不过,使用SLS技术进行设计时需格外谨慎,以避免出现热变形、粉末残留或结构强度不足等问题。
若想获得高质量的SLS零部件,卓越的设计是关键。许多常见问题——如翘曲变形、薄壁结构强度不足或难以脱粉等——往往源于零件设计方式。其中一个最重要的考量是避免大面积平面设计,这类结构极易发生翘曲变形。若必须使用平面结构,可以通过增加加强筋来提供支撑,但这并不能完全消除风险。牢记这些设计要素,您将能有效提升打印品质和部件性能。以下是一些关键性的SLS设计技巧,助您获得更优质的打印效果。
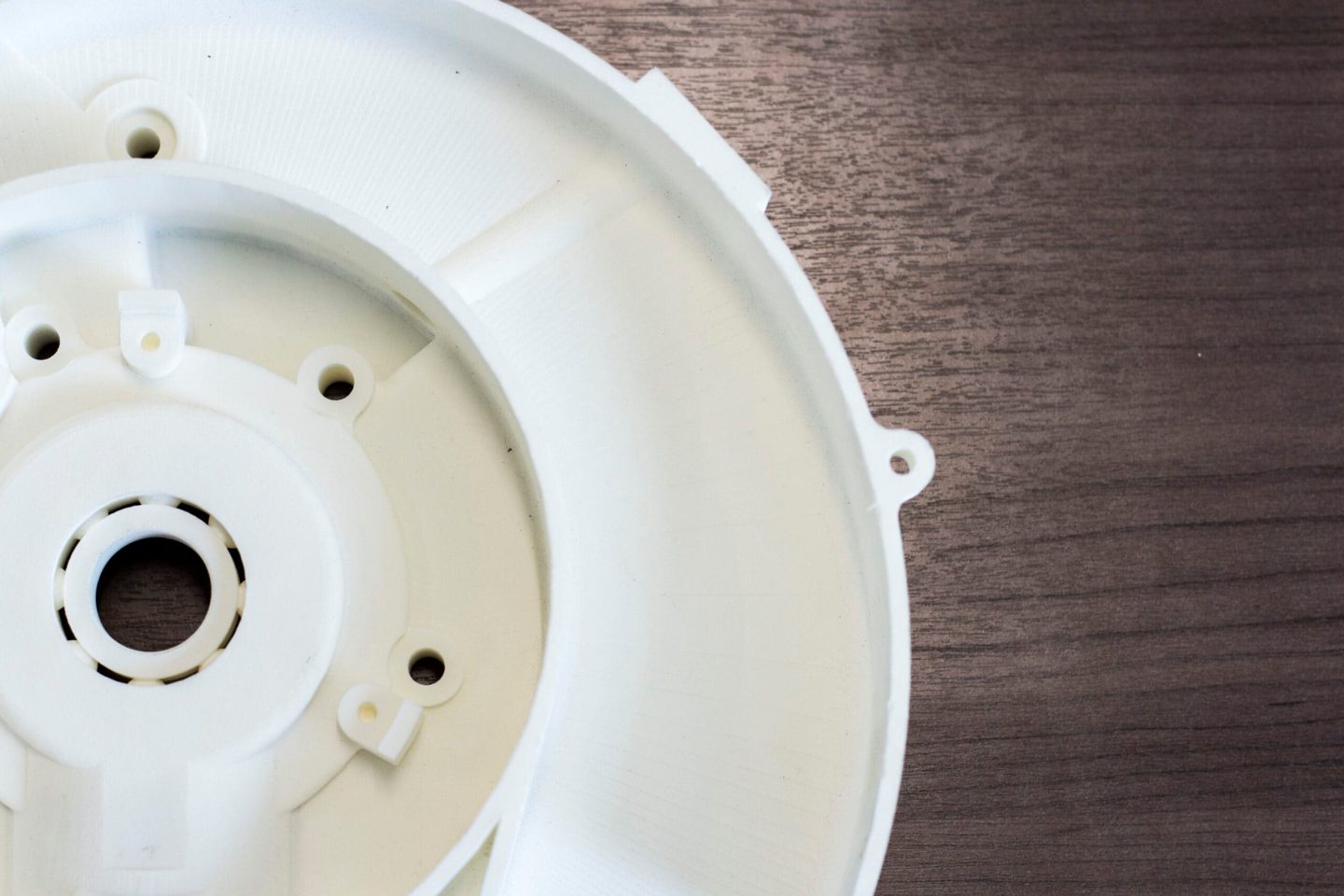
1 保证适当的壁厚度
壁厚在SLS零件的结构完整性、精度和可制造性中起着关键作用。若壁厚过薄,可能会因材料支撑不足和烧结过程中的热应力导致翘曲、开裂或脆化。
壁厚小于0.5mm时问题尤其突出,因为激光产生的热量会使薄壁区域过度增厚,导致意外的尺寸偏差。薄壁结构在后处理(如喷砂处理)过程中也容易变得脆弱。
另一方面,过厚的壁可能使热量滞留时间过长,导致内部应力、翘曲和收缩。这可能导致零件尺寸精度不佳或表面缺陷。厚壁结构还会增加材料成本并延长冷却时间,进而影响整体生产效率。
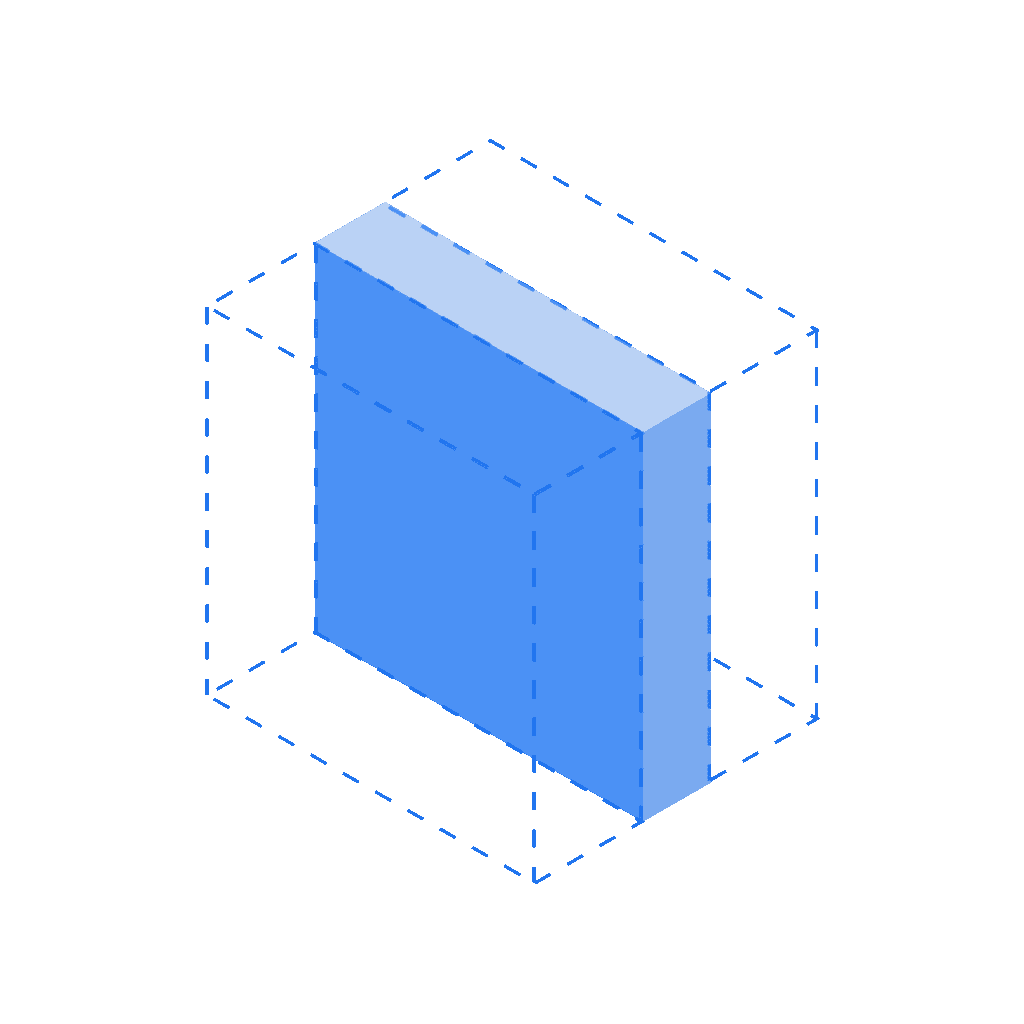
经验法则:
- 设计壁厚至少为0.7mm(PA12)–2.0mm厚度(),具体视乎材料而定。
- 若提供支撑结构,壁厚可薄至0.6mm,但为确保可靠性和重复性,建议优先选择1.3mm。
- 大多数情况下,壁厚无需超过4mm,过厚会导致热量积聚和翘曲。
- 保持壁厚一致以避免翘曲。
- 在薄弱区域添加加强筋或圆角以增强强度。
2 有效粉末清除的设计
由于SLS工艺无需支撑结构进行打印,过量的未烧结粉末会残留在中空部件、内部通道及空腔结构中。若未进行合理清理,被滞留的粉末会增加部件重量,影响机械性能,并使后处理工序复杂化。残留在零件内部的粉末可能干扰运动组件的运行或功能性结构特征,使得优化粉末排出通道的设计变得尤为关键。
为降低重量及材料消耗,可将零件设计为中空结构而非实心体。然而这类中空结构必须设置排屑孔以促进残留粉末的排出。若开口数量不足,粉末可能在内部压实结块,造成难以甚至无法彻底清除的问题。
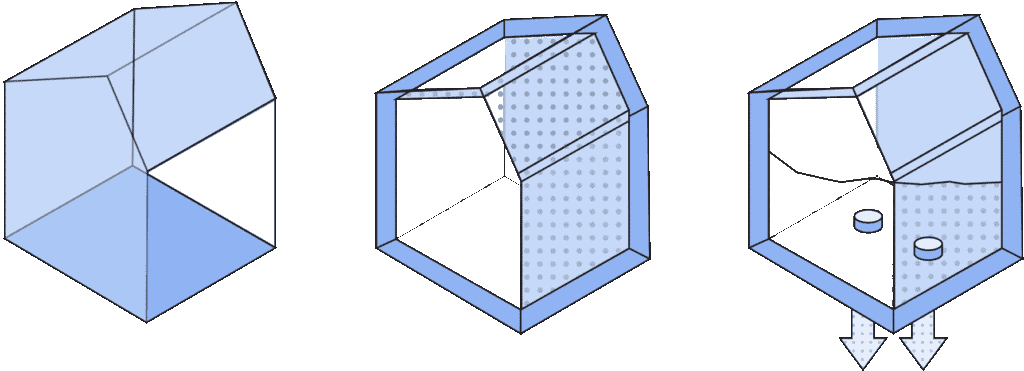
此外,足够大的排屑孔便于采用介质滚磨等后处理技术,可对中空零件的内表面进行抛光处理。
经验法则:
- 最小排屑孔径:3.5mm。直径越大越好!
- 在边缘或相对侧设置多个排屑孔,确保有效清除粉末。
- 确保内部通道光滑,防止粉末堆积。
3 优化孔洞与通道几何结构
SLS技术能制造复杂内部通道和孔洞,但不当设计会导致收缩、变形或堵塞。圆形孔洞可能在烧结时收缩,通道方向不当会导致粉末残留或精度损失。
SLS的收缩率高达3%-4%,相较其他工艺更高。建议将孔洞设计为标准钻头尺寸,必要时可通过机械铰孔修正以提高精度。
若需在通道内集成连接点(如进气口),应设计流线型水滴状空气动力学支撑结构。这能在保障连接强度的同时最大限度减少气流阻碍。
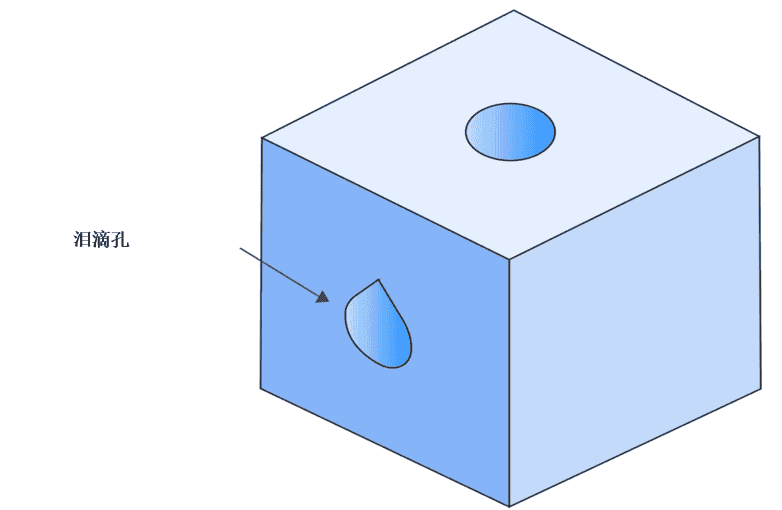
经验法则:
- 最小孔径:1.5mm。
- 采用泪滴形或菱形孔代替圆形孔。
- 尽可能采用垂直方向开孔以保证精度。
4 确保配合部件留有适当间隙
活动或互锁部件需要精确的间隙才能正常运作。若间隙过小,烧结过程中部件可能熔结在一起,导致功能失效。
相反地,若间隙过大,则会导致装配松动、契合不当,降低机械稳定性。
SLS工艺优势之一在于,其可在同一次构建中直接打印相互配合及活动的部件,省去单独打印和人工组装的步骤,从而实现单一制造周期内产出完整功能组件的特性。然而,为确保打印后的组件不会烧结成一个整体,必须通过合理间隙设置使多余粉末完全清除。
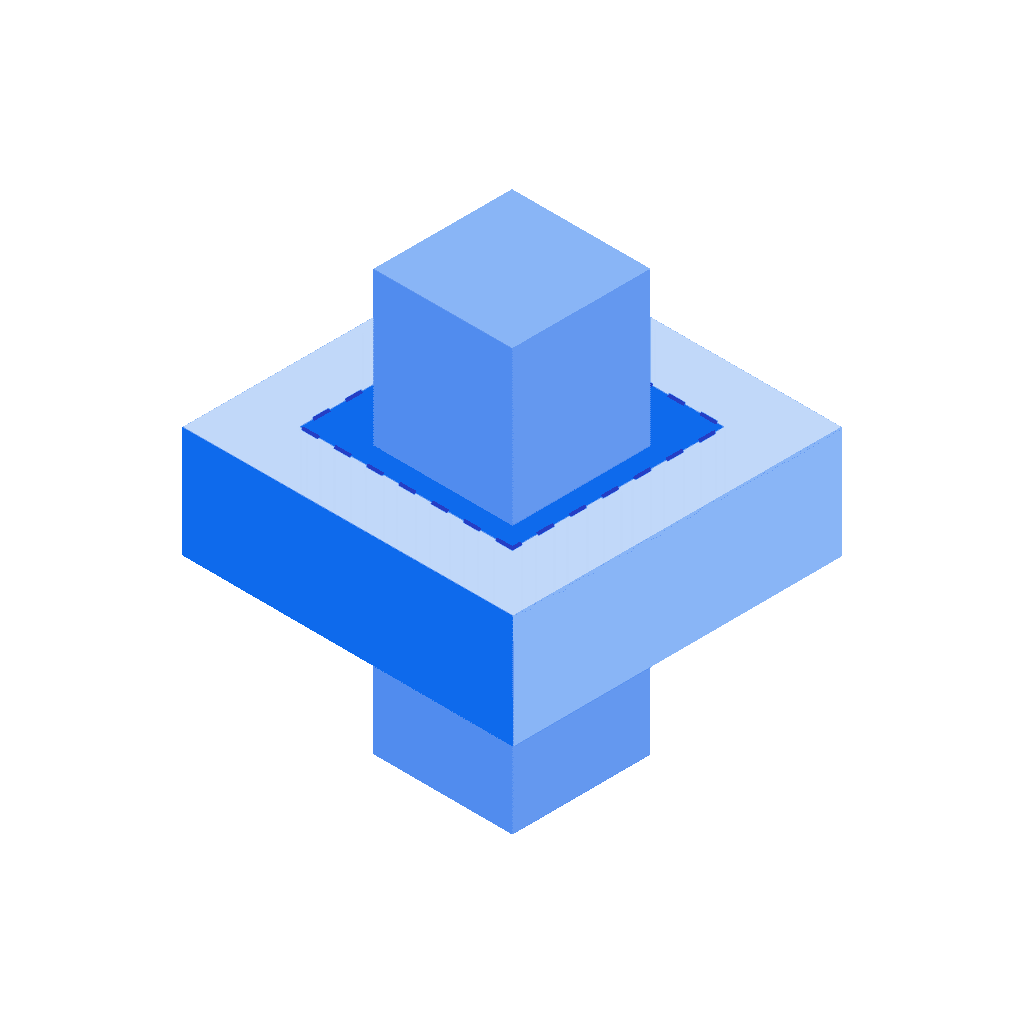
经验法则:
- 配合部件间隙:0.5mm(最小)。
- 压配结构特征:0.3mm间隙(适用于紧密配合)。
- 铰接/连接部件:0.6mm间隙以避免粘连。
5 避免大悬垂和无支撑跨距
尽管SLS技术不需要支撑结构,但过长的悬垂或未支撑跨距可能因重力和残余热量影响而下垂、变形或表面粗糙。
为提高打印质量并保持尺寸精度,设计应优先采用渐变过渡的自支撑几何结构,而非突然的悬垂。拱形、穹顶或倾斜表面(通常与构建平台成45°或更小角度)等结构特征能更有效地分散应力,降低下垂风险。
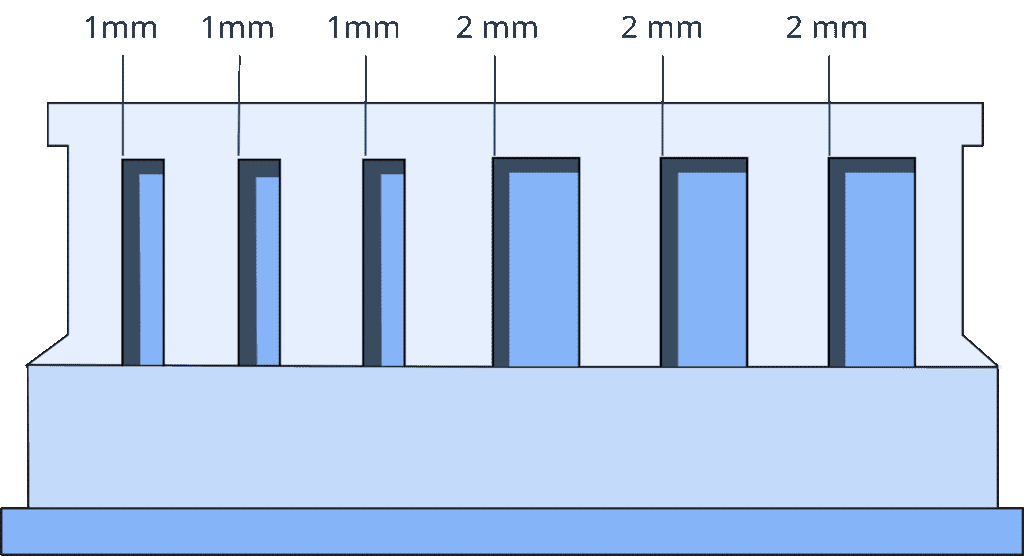
经验法则:
- 悬垂角度保持在45°以下以获得最佳效果。
- 设计类似倒角和圆角的自支撑几何体结构。采用30°或以下的角度,并在拐角处添加圆角或倒角。
- 将无支撑的桥接跨度限制在2mm以保证结构稳定性和表面质量。
6 为小细节选用正确的特征尺寸
像浮雕文字、徽标和表面纹理等精细细节,若尺寸过小可能导致模糊或无法辨认。确保合适的特征尺寸可提升可见度,并在打印后保持清晰的细节表现。
在SLS工艺中,细节可以通过直接雕刻或浮雕方式呈现在零件上,最小深度或高度需达到1mm。此深度对于后处理尤为重要,因为小于1mm的雕刻或浮雕在介质滚磨或其他表面处理过程中可能被磨损。文字也可直接打印在SLS零件上,但为了最佳可读性,字母高度至少应为2mm。
此外,为文字添加微小拔模角度可进一步提升耐久性,确保精细特征(如小写字母“i”上的圆点)能承受后处理及日常使用。
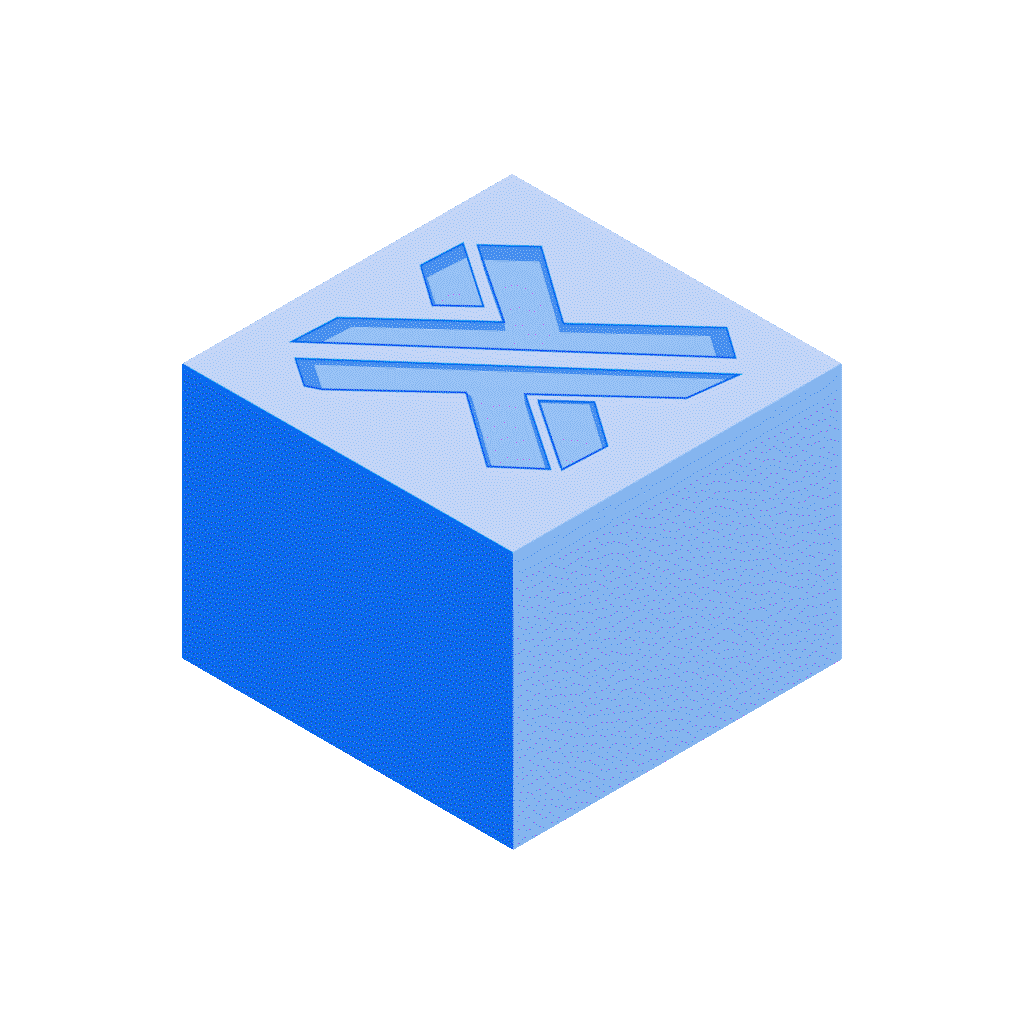
经验法则:
- 浮雕文字高度(字号)或雕刻深度:1mm。
- 保证可读性的最小字号:2mm。
- 推荐使用无衬线字体以优化可读性。
7 加固细长结构特征
细长且无支撑的结构特征(如细针、薄壁和精细细节)在热应力下容易断裂或变形。高温打印与冷却收缩的共同作用会削弱这类特征,导致弯曲或变脆,尤其在后处理或搬运过程中更易受损。加固这些结构可提升耐用性与整体稳定性。
经验法则:
- 最小针脚直径:0.8mm(建议1mm或以上)。
- 可添加加强筋或角撑板等支撑结构以加固薄弱特征,并将其与主体结构相连接。
- 避免设计无额外支撑的高、窄结构。
- 使用渐变性过渡而非截面的突然变化。
- 优化零件在成型舱内的方向,例如将细长特征平行于构建平台打印,而非直立放置。
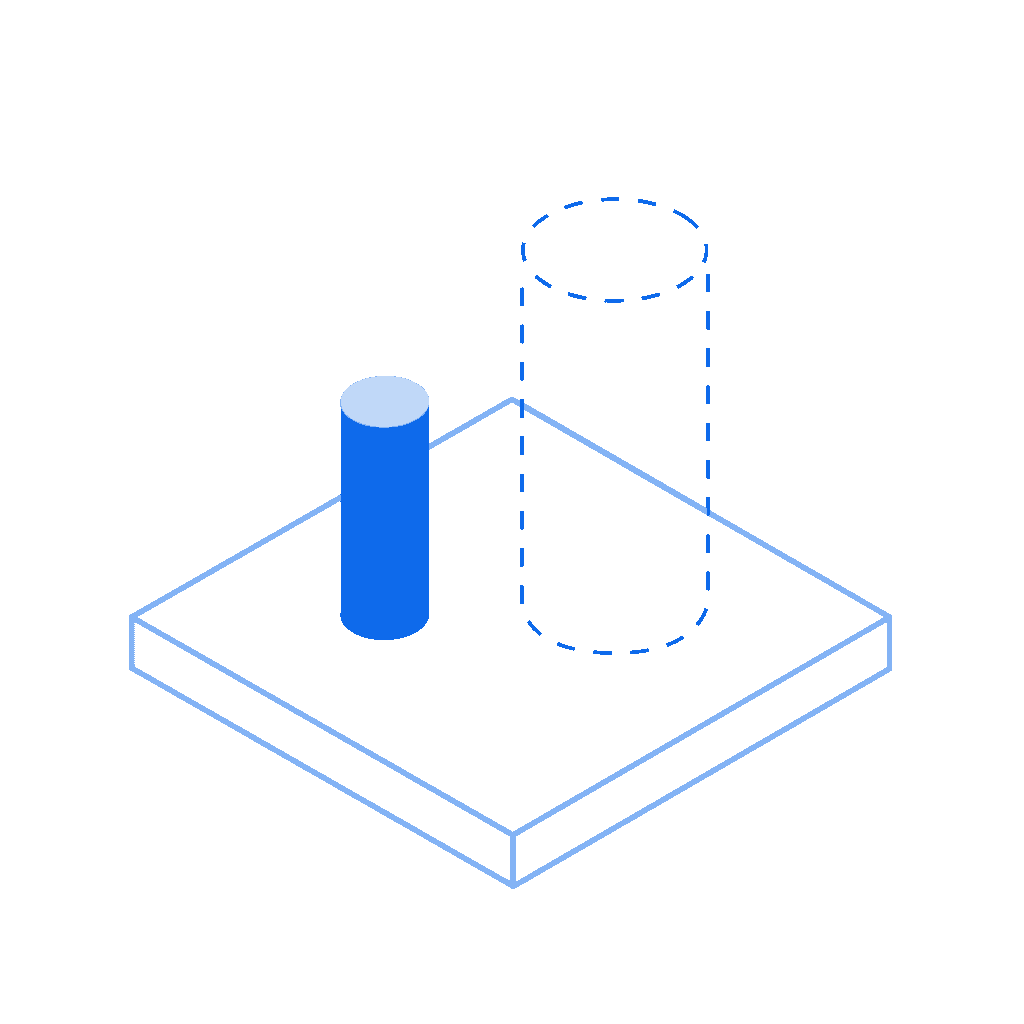
8 考虑收缩率和尺寸精度
SLS零件在冷却过程中可能发生轻微收缩,这会影响精度和公差。这是由于烧结过程的热特性导致的,材料在冷却时会收缩。在设计时考虑预期的尺寸变化有助于防止误差,并确保最终更好的配合效果,特别是对于需要组装的零件。
如果您自行打印零件,请记住可实现的尺寸精度取决于打印机和零件尺寸。SLS能够实现高精度,通常特征尺寸精度可达±0.3%,最低±0.3mm。但公差应仅限于真正需要的区域(如配合面或功能接口)。在整个设计中过度应用公差会增加打印工作量和成本,而不会带来实际效益。
如果通过Xometry择幂科技生产零件,我们的制造合作伙伴将在打印过程中处理收缩率和尺寸精度问题。
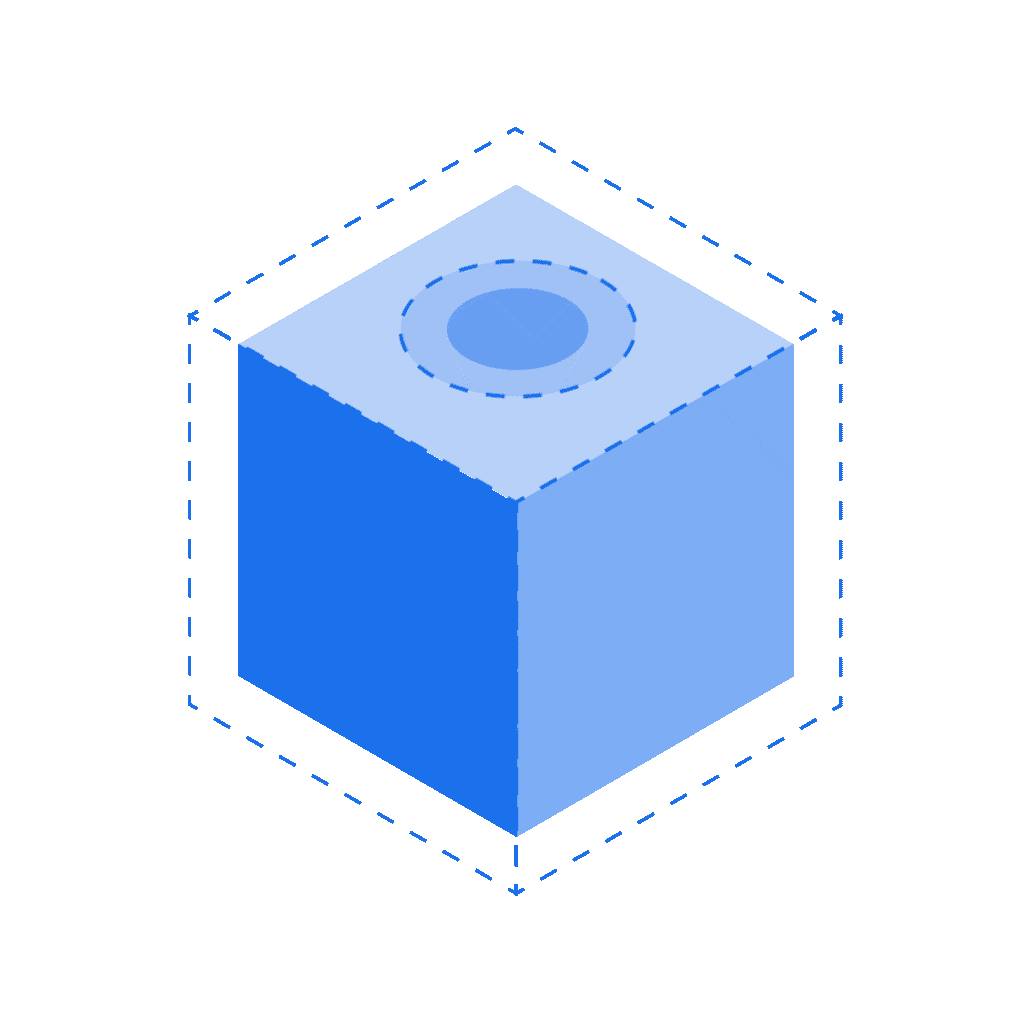
经验法则:
- 尺寸公差:±0.3mm
- 在CAD模型中预留预期收缩量(通常3-4%)
- 避免尖锐边缘以减少热应力,确保零件更坚固。
SLS技术规格参考指南
下表总结了Xometry择幂科技针对不同零件特征的SLS3D设计规格快速参考。所有这些因素在设计高质量打印件时都至关重要。
规格 | 详情 |
最大构建体积 | 340x340x605mm。建议:320x320x580mm |
最小特征厚度 | 0.50mm |
建议最小壁厚 | 0.50mm(带支撑),0.60mm(无支撑) |
层厚度 | 0.10–1.50mm。当壁厚较高时,~0.1mm,水密零件1.5mm |
一般公差 | ±0.3%(±0.3mm) |
此外,足够大的排屑孔便于采用介质滚磨等后处理技术,可对中空零件的内表面进行抛光处理。
选择Xometry择幂科技实现您的设计零件3D打印
SLS是制造复杂且高质量零件的宝贵技术。通过预判并理解设计、加工和后处理阶段可能遇到的挑战,您可以大幅提升SLS设计的成功率。
在设计可制造性时,需考虑壁厚等细节因素。在设计阶段解决所有可能导致缺陷的因素,避免打印件出现翘曲、裂纹和薄弱点。同时优化设计以减少材料浪费,并为具体应用选择最合适的材料。这能确保SLS打印的零件坚固耐用且功能完备。
若您已准备好将SLS设计提升至新高度,请探索Xometry择幂科技专业的SLS 3D打印服务,立即启动您的3D打印项目吧!