Selective laser sintering (SLS) belongs to the powder bed fusion (PBF) category of 3D printing technology that involves a high power laser to sinter small particles of polymer powder into a product based on a 3D CAD model. Due to its high resolution, high productivity and easy availability of materials make SLS technology ideal for a range of applications like rapid prototyping to end-use parts.
How selective laser sintering 3D Printing works
Selective laser sintering involves fusing of layers of material powder (typically ~0.1 mm thick), spread evenly across the build area using a counter-rotating leveling roller. The part building process takes place inside a closed nitrogen gas filled chamber (or any inert gas) in order to minimize oxidation and degradation of the powder.
Step 1 - Preheating the powder
- The powder in the build platform is preheated and maintained just below the melting point and/or glass transition temperature of the powdered material with the help of infrared heaters present above the build platform.
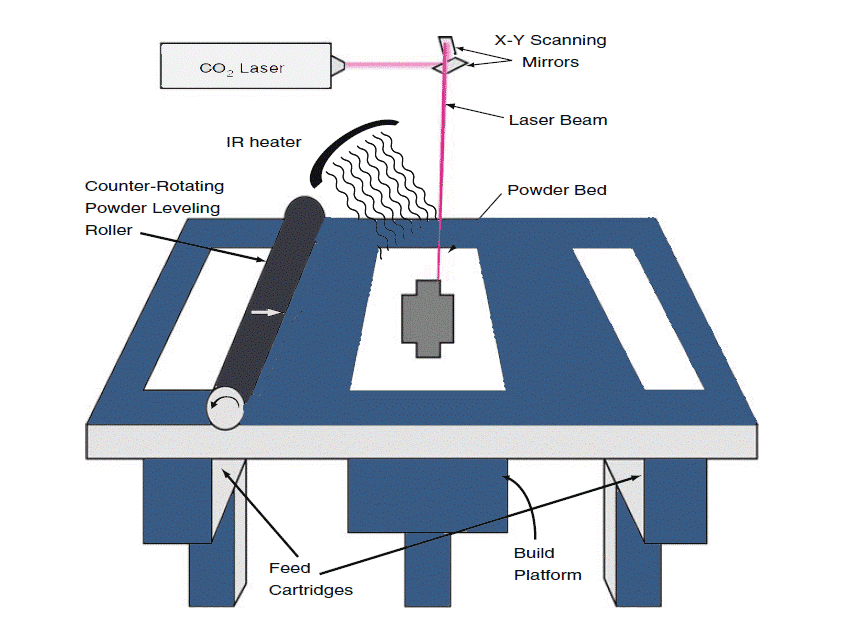
Step 2 - Printing the SLS 3D parts at high temperature
- As soon as the thin powder layer is formed and preheated, a focused CO2 laser beam is directed onto the powder bed and moved using galvanometers in such a way that it fuses the material thermally to form the cross-section layer by layer depending on the CAD design. How thick a layer should be is decided in the slicing software.
- Surrounding powder remains loose and supports the next layers which eliminates the need for the support structures.
- After a layer is completed, the build platform is lowered depending on the layer thickness (slicing) and a new layer of powder is laid and leveled using the counter-rotating roller.
- The CO2 laser beam scans the subsequent cross-section of the layer. This process goes on until the whole part is built.
Step 3 - Cooling and post-processing the SLS 3D parts
- Finally, the completed parts are removed from the powder bed and the loose powder is cleaned off. Further finishing operations are performed, when necessary (dying, colouring, bead blasting, food grade finishing).
Materials for SLS 3D Printing
Selective laser sintering is a popular technology among 3D printing processes as it can be used with a wide range of materials. The most currently used materials can be classified in two categories:
- Rigid materials: such as Nylon 11 (PA11 Food Grade), Nylon 12 (PA12 Food Grade, PA12 Alumide Grey, PA12 Glass-Filles) and PP Polypropylene
- Flexible materials: such as Flex Whitish TPU/TPE
Nylon PA12 is one of the most popular 3D printing materials. This plastic material has good mechanical properties such as toughness, tensile strength and impact strength, making it a reference material for SLS technology.
Advantages of SLS technology in 3D printing
SLS is one of the most reliable, precise, and fast methods for prototyping, small batch production and also for industry grade applications. Selective laser sintering technology has a set of advantages that makes it unique.
SLS prints do not require support structures
Since selective laser sintering printing technology belongs to powder bed fusion, its designs do not need any support structures. While printing, all the empty spaces are filled with the unused loose powder, making SLS prints self-supportive.
Hence, designs with empty hollow spaces, overhanging features and very thin features which usually require support is no longer a problem printing with SLS, thus offering the product designers a large scope for design freedom.
Parts with complex internal components, channels, can be built without compromising the design as there is no fuss of support structures. SLS can be the best solution for printing complex designs instead of printing in multiple parts which generally is an issue when the alternatives like FDM are used.
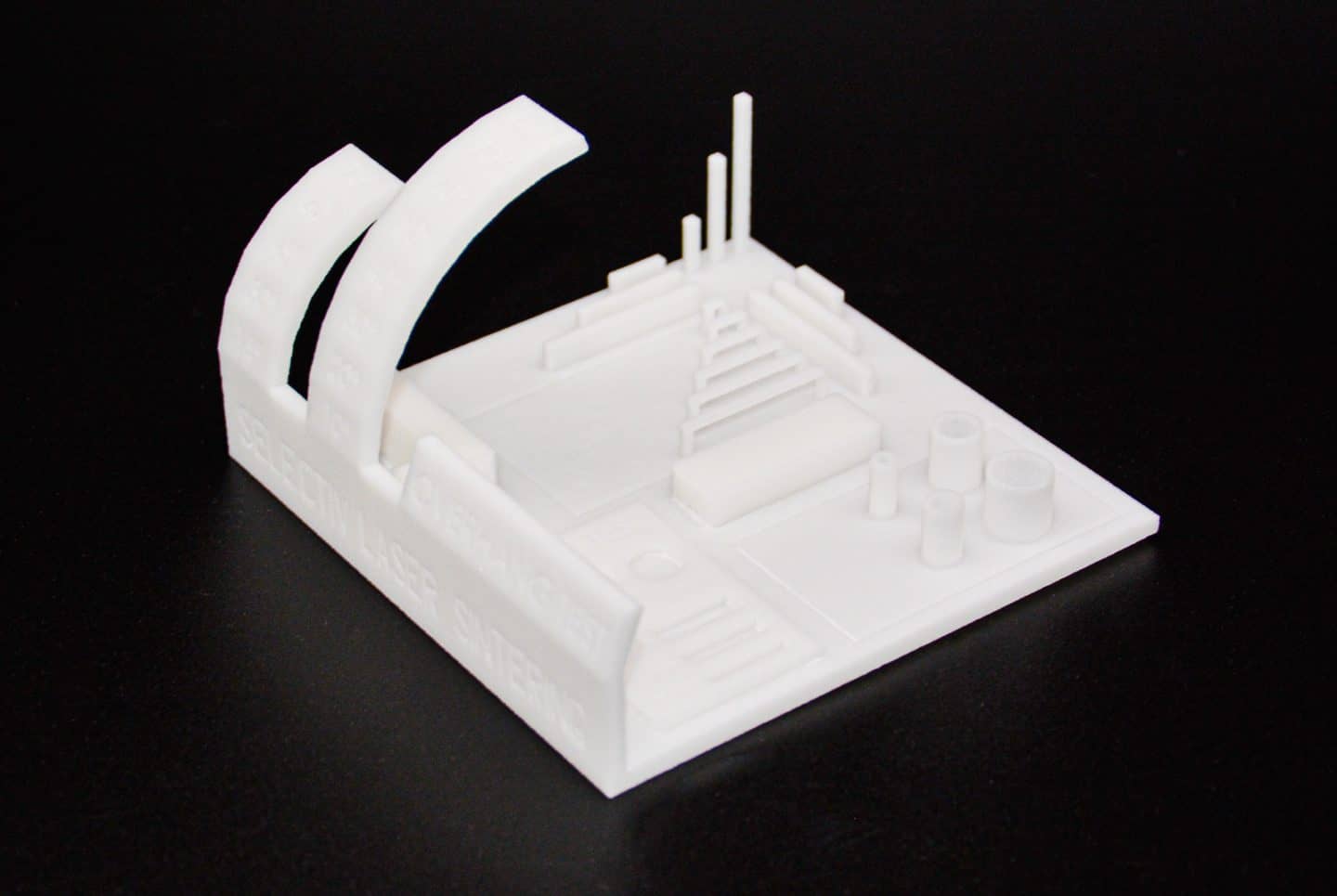
SLS is a fast 3D printing technology
SLS is one of the fastest 3D printing technologies as the polymer powders used in SLS only require very little exposure to the laser in order to be sintered. In fact, speed has to be quantified with respect to the print resolution.
For example, an FDM printer can also print fast if it is set to print thick layers and compromising on the resolution. With SLS, there is no such compromise for resolution with faster print speed..
SLS parts are perfect for dying and colouring
SLS prints generally possess a porous surface making them excellent for the coloring. Also, dyeing using a hot bath process is very effective. Since the surface is porous, the colour sticking is also efficient.
SLS has excellent mechanical properties
SLS prints have very strong layer adhesion compared to its alternatives like FDM. Hence, SLS prints have isotropic properties which means that the tensile strength, mechanical hardness and elongation of the SLS printed part are almost equal along all directions (3 axes).
Due to the excellent mechanical properties, SLS printed parts are often used as an alternative for typical injection moulded plastic parts. SLS prints also offer decent chemical resistance (e.g. Nylon PA 12).
Disadvantages of SLS technology in 3D printing
Apart from the advantages it offers, there are also a few common disadvantages that Selective laser sintering technology possesses.
SLS parts are porous and have a brittle structure
Although SLS prints have a good tensile strength, they are much less flexible and can undergo less deformation before failure. The same porosity that makes SLS prints excellent for dyeing also compromises their structural integrity. For this reason, SLS prints are best used as prototypes and not recommended as functional parts.
SLS prints have a high shrink rate
As per the working mechanism of SLS, the print powder needs to be exposed to elevated temperatures in order to sinter. As it starts to cool, contraction or shrinking takes place, resulting in a dimensionally inaccurate part. Shrinkage rate is as high as 3% to 4% which is comparatively more than the alternatives.
This needs to be considered in the design phase and the volume of the model is adjusted accordingly. The stress due to the contraction can also accumulate in sharp edges and corners, resulting in warping or distortion.
Higher waste production due to SLS powder material
The powder inside the build chamber needs to be pre-heated so that it can be sintered with just the slightest exposure to the laser. Elevated temperature sintering of the powder surrounding a part being built can cause particle grains in the loose powder bed to fuse which compromises the quality of the powder.
Since you will always end up with a portion of unused powder with every single print, you will inevitably accumulate so much unused nylon powder that has to be discarded. With this single detail, selective laser sintering printing already generates more waste compared with MJF that doesn’t preheat the powder. The loose nylon powder is also a respiratory hazard which you’ll need to protect yourself from.
Xometry’s SLS 3D printing services
Xometry offers selective laser sintering services online, for on-demand 3D printing projects, for both prototypes and large batches. With a network of more than 10,000 partners all over the World, Xometry is able to deliver SLS 3D printing parts in up to 3 days. Upload your CAD files to Xometry Instant Quoting Engine to get an instant quote with various manufacturing options available for SLS 3D printing.