This article explores the post-processing operations available for SLS and MJF printed parts, their application, and their pros and cons
SLS and MJF are powder-based 3D modeling technologies that are used to create parts from thermoplastics and elastomers. Like in many other manufacturing methods, post-processing is carried out in SLS and MJF to complete the manufacturing process.
Processing operations are usually carried out on SLS and MJF 3D printed parts for various reasons such as improving surface finish, improving mechanical properties, improving aesthetics and even enabling electrical conductivity. Another reason for post-processing is that certain materials with certain desirable properties are not available for SLS or MJF printing. The available materials are processed to give them the desired properties.
De-powdering and bead blasting
This is the standard procedure for printed parts. After printing and cooling, parts are removed from the build platform and de-powdered using a brush. SLS and MJF don’t require support structures for parts to be printed, therefore, support structure removal which is a crucial post-processing operation in other 3D printing technologies is not necessary. After de-powdering, the parts are bead blasted to remove any remaining powder, using high-pressure compressed air containing tiny glass beads.
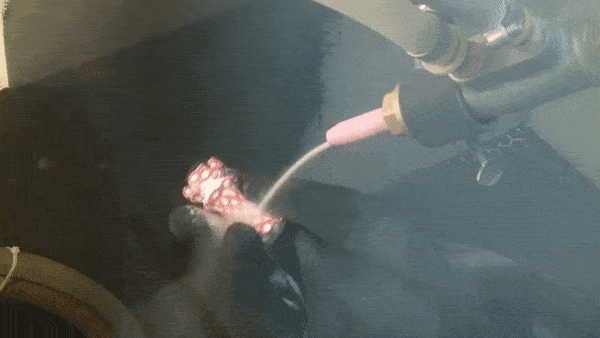
Media tumbling
Also known as vibro-polishing, media tumbling is a finishing process in which a printed part is placed in a vibrating tumbler that contains several small ceramic chips. The part is left in the tumbler for some hours. As the tumbler vibrates, the chips vibrate against the part, gradually polishing the outer surface. Media tumbling is used to reduce roughness and achieve a smooth satin-like surface finish. The mechanism of action of this process may have a small wear effect on the dimensions of parts that have fine details.
Pros
- Produces a smooth satin-like surface finish
- Can process several parts at once
Cons
- Not suitable for parts with intricate details as such details may wear off
Dyeing
Dyeing is the fastest and most cost-effective way to colour SLS and MJF printed parts. The main purpose of dyeing is to improve aesthetics. In this process, an acid dye is used to pigment a part in a heated water bath. The part is submerged in the dye for about 10 minutes for proper penetration. Like media tumbling, this process can be carried out for several parts at the same time.
Dyeing does not pigment parts full through as dye can only penetrate parts to a depth of 0.5mm. If the part is deeply scratched or cut.
SLS Nylon is usually printed white or grey and can be dyed a variety of colours. MJF parts, on the other hand, are printed in grey. Underneath the surface, however, these parts are jet black. For this reason, MJF parts are usually dyed black.
Pros
- A wide range of colours are available, especially for SLS parts
- Does not affect part dimensions
- Several parts can be dyed at once
Cons
- Does not result in a glossy surface finish
- Dye penetrates parts by only 0.5 mm. So this layer can wear off
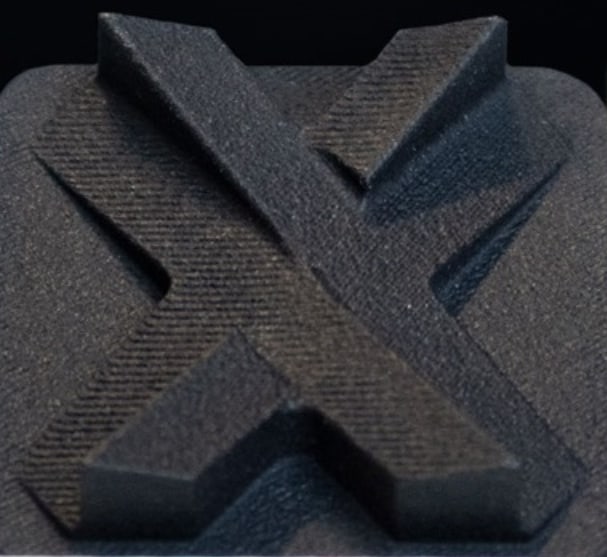
Dyed green SLS Nylon PA 12
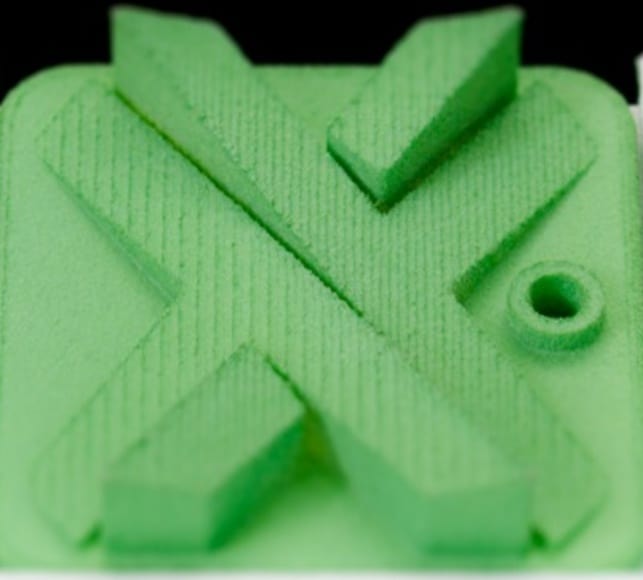
Painting and Lacquering
Painting and lacquering are used to obtain various aesthetic finishes such as a metallic sheen or a high gloss. Lacquering also improves water tightness, surface hardness, and wear resistance. Because of the porous nature of MJF and SLS printed parts, it’s best to apply several very thin layers of lacquer instead of a single thick layer.
Pros
- Painting gives parts a glossy look
- Lacquering improves physical properties
Cons
- Parts have to be processed individually
- Parts require careful pre-processing surface preparation
Water tightening
Properly printed SLS and MJF parts are reasonably watertight. To further enhance this property, coatings can be applied to the parts. The best coatings for this purpose are silicones and vinyl-acrylates.
Pros
- Provides excellent water resistance
Cons
- Coatings are thick and may affect parts
Metal coating
SLS and MJF parts can be metal plated to increase strength and electrical conductivity. Electroplating can be done with copper, gold, nickel, chrome, stainless steel. Metal-coating is achieved through electroplating; a process in which a metal is dissolved in a solution and the metal particles are attached to the surface of the printed part by an electric current.
Pros
- Improves strength and enables electrical conductivity of parts
- Results in an excellent surface finish
Cons
- May increase part weight
- More expensive than other forms of coating
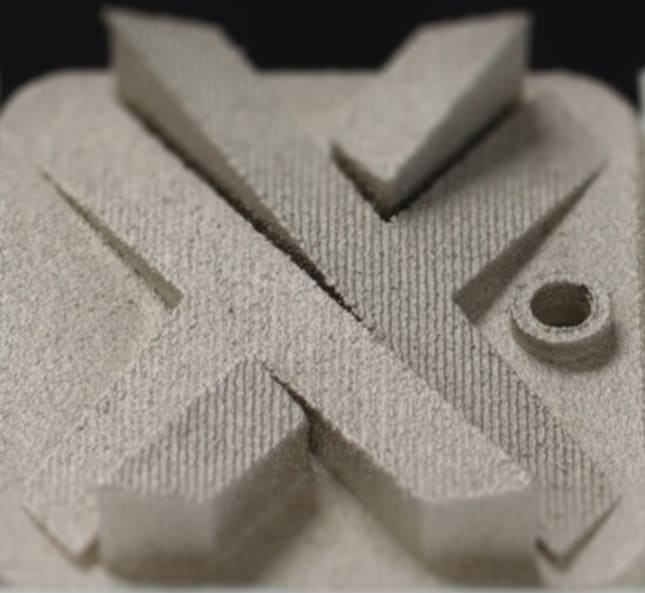
Conclusion
At Xometry, we offer several post-processing operations for your SLS and MJF 3D printed parts. Head over to our instant quoting platform to upload your models and get a quote for your parts.