Selective Laser Sintering (SLS) and Multi Jet Fusion (MJF) are the two most ubiquitous 3D printing technologies for polymers and elastomers. While they share some similarities, there are some differences between these technologies that make each one more suitable than the other in different situations.
3D Printing technologies description
Selective Laser Sintering
In SLS technology, a printer, using cross-sections of a 3D CAD model as a guide, deposits a layer of material powder on a building platform. A high-power CO2 laser sinters this layer according to the required shape from the CAD model. Another layer of material is deposited on the previous layer and sintered again. This process of layering and sintering is repeated until the part is formed.
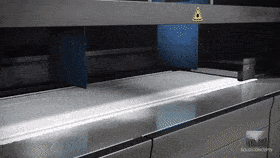
Multi Jet Fusion
MJF (Multi Jet Fusion), also known as HP MJF, is similar to SLS. However, in MJF, after each layer of powder is deposited and heated to a near sintering temperature, an inkjet array jets a liquid fusing agent on the layer. This fusing agent promotes the absorption of infrared rays. A detailing agent is also deposited along the exterior edges of the part. An infrared source then sinters everything together before a fresh layer of powder is deposited on the previous layer. These processes are repeated until the part is created.
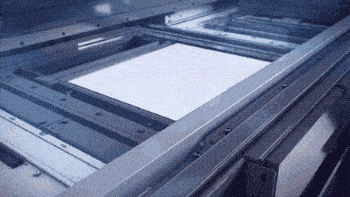
Similarities between SLS and HP MJF
The major similarities between the technologies are:
- They are both powder fusion technologies involving the use of powdered material
- They both require a heat source for sintering
- Neither of them requires object support during printing, thus allowing the construction of complex geometries
- They both work by layering
- They work mainly with thermoplastics and elastomers
Differences between SLS and HP MJF
Materials
SLS has been around for a much longer period, having been originally patented in 1997. This technology has gone through several advancements that enable it to cater for several materials such as PA 11, PA 12, PA 12 Glass-filled, PEBA 2301 3D, Alumide, TPU, etc. This offers the flexibility of choice for the SLS process.
MJF, on the other hand, is relatively new as it was made commercially available as recently as 2017. Therefore, this technology can work with only a few materials such as PA 12, PA 11, and TPU.
Dimensional accuracy and feature resolution
Both technologies offer high dimensional accuracy. Putting MJF vs SLS however, SLS parts have a slightly finer feature resolution than MJF. However, as both technologies are susceptible to warping, flat large surfaces should be avoided for printing.
Processing time
SLS and MJF have roughly the same print time for the production of one part. However, for the time taken for the entire process including setting up the machine, printing, and cooling, MJF requires a shorter time. This is because MJF printers have a removable build platform that allows for the printed part to be cooled outside of the machine. Also, for the production of many parts, MJF is faster as this technology can print dozens of parts at the same time.
Concerning recyclability, 80% of the powder recovered from MJF printed parts is recyclable, compared to SLS with 30 - 50% recyclability.
Surface finish
The surface finish of parts from both technologies is grainy, with MJF parts having a slightly smoother finish. SLS parts are usually white or grey and can be dyed in a wide variety of colours. The fusing agent used in MJF is black to enhance the absorption of infrared rays. Because of this black colour, MJF parts usually have a greyish appearance and are usually dyed black.
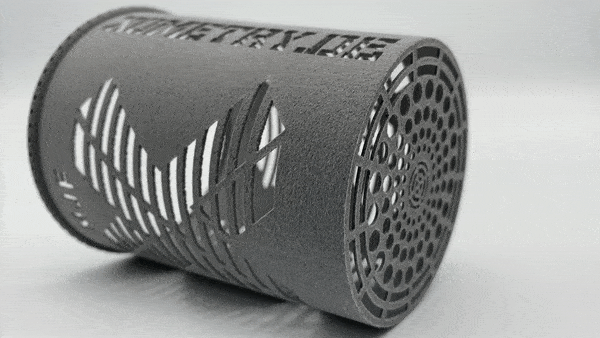
Properties of 3D printed parts
MJF and SLS parts have slightly varying mechanical and physical properties. The properties of SLS vs MJF are given in the table below.
Property | MJF | SLS |
Tensile strength (Mpa) | 1700 (X,Y) 1800(Z) | 1650 (X,Y) 1650 (Z) |
Tensile Modulus (Mpa) | 48 (X,Y) 48 (Z) | 48 (X,Y) 42(Z) |
Strain at break (%) | 20 (X,Y) 15 (Z) | 18 (X,Y) 24(Z) |
Melting point (°C) | 187 | 176 |
Part size
SLS printing is able to produce larger parts (up to 600 x 350 x 560 mm) than MJF printing (up to 380 x 284 x 380 mm). On the other hand, MJF can print features as small as 0.5 mm, while SLS can print a minimum feature size of 0.8 mm.
Cost
The production costs of single parts in MJF and SLS are approximately the same, but MJF parts become cheaper at scale. This is because of the HP MJF printer’s ability to print several parts simultaneously.
Head over to our Instant Quoting Engine to upload your models for SLS or MJF 3D printing, and compare prices in a few seconds.
How to choose the right 3D printing technology
Property | SLS | MJF |
Materials | Can print several materials including PA 11, PA 12, PA 12 Glass-filled, TPU, PEBA 2301 3D, and Alumide | Can currently print only PA 11, PA 12, PA 12 Glass-filled, and TPU |
Dimensional accuracy | Produces parts with slightly higher dimensional accuracies than MJF. | Produces parts with very high dimensional accuracies. |
Processing time | Takes longer to produce parts than MJF, especially for larger quantities | Takes a shorter time than SLS to produce parts. This is due to the presence of a removable build platform in MJF printers that allow parts to cool outside of the printer. These printers can also print many parts simultaneously |
Finishing | Parts produced have a grainy surface finish | Parts produced also have a grainy surface finish but are slightly smoother than their SLS counterparts |
Part size | Can produce parts as large as 600 x 350 x 560 mm, and features as small as 0.5 mm | Can produce parts as large as 380 x 284 x 380 mm, and as small as 0.5 mm |
Cost | The production costs of single parts in MJF and SLS are approximately the same, but MJF parts become cheaper at scale. |
Xometry offers both of these 3D printing technologies for many materials. Uploads your CAD files and get an instant quote for your project using our instant quoting engine.