Injection moulding and 3D printing are the two most widely used manufacturing technologies for the production of plastic parts. This article gives a brief overview and comparison of both the technologies and lists several factors that need to be considered to choose the best technology for your project.
What is the difference between 3D printing and injection moulding?
3D printing
3D printing is additive manufacturing, which means the initial material is built layer by layer. 3D printing creates three-dimensional objects from reading a virtual computer design and reproduces it into a tangible part by using material filaments or powders.
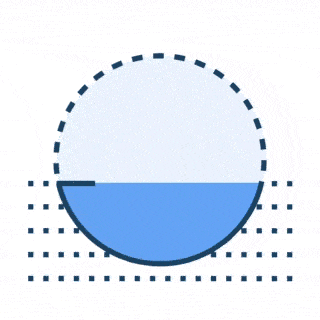
Injection moulding
Injection moulding makes use of moulds. First, an object’s inverse is machined out of a material (e.g. aluminium, tool steel) that is safe to handle the molten build material (the material the finished object is made of). Then, the molten build material is poured into the mould. Once the material has cooled in the mould, the part is ready.
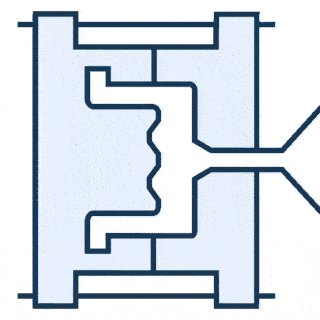
How to choose: Injection moulding or 3D printing?
When it comes to the selection of either injection moulding or 3D printing for production, here are the prime factors that need to be considered.
Batch size
The number of parts required is a key factor in deciding the process. Injection moulding is known for its effectiveness in high volume production runs (1000+ parts per run). For low volumes (below 10), 3D printing is more appropriate and cheaper. For simple 3D printing processes like FDM or SLS used with affordable plastics like ABS, PC, Nylon, single parts or small quantities (identical and non-identical), 3D printing is undoubtedly the option to go for. MJF is also another viable option for midsized quantities (10-1000) and is very common.
Conclusion: Injection moulding is a perfect option for bulk production whereas, for small batches of units, go with 3D printing.
Design complexity
An injection moulding process requires a mould to be built (inverse to the part) according to the required part design. Designing a CAD model for injection moulding is not easy as there are many considerations. For example, right angles in the part design make it tough to remove from the mould and also delicate areas have to be treated with utmost care. Whereas, attaining complex designs is where 3D printing excels. No matter how complex the design is, 3D printing makes it possible with minimum effort.
Conclusion: Check if your design is manufacturable with injection moulding, if not – it should be adjusted, otherwise go with 3D printing.
Turnaround time
Injection moulding requires longer turnaround times as it involves the analysis of the design and building of the perfect mould according to the design (10-20 days). The turnaround times for 3D printing are very less compared to injection moulding. You can get your 3D printing order at Xometry delivered in as quick as 3 days.
Conclusion: If you need the part immediately, go with 3D printing.
Customization
Once the mould is built for injection moulding, it involves a lot of money and time to modify the re-design of it. When coming to customization of parts or modifications to the existing design, injection moulding is not recommended. Whatever you get from the mould is the final part and it’s very complex to modify it. On the other hand, 3D printing offers a lot of scope for customization and all it takes is a modified or customized CAD file. Hence, it is good for prototypes, test pieces.
Conclusion: 3D printing is advised for prototyping and customization.
Material strength
Parts manufactured through injection moulding consist of a single poured layer, which adds strength to the shape because there are no fissures or points of weakness. Whereas in 3D printing, the part is made layer by layer which impacts its overall strength. 3D printing can create visible ridges and structural faults during manufacturing that typically don’t occur with plastic injection moulding.
Conclusion: If the material strength is a priority, go with injection moulding.
Surface finish
Even though 3D printing’s layers are small and close together, they are still noticeable. This creates a ridged surface on finished objects no matter how fine the layer detail is. This presents a problem if you want to manufacture objects that will rub against other objects, like machine parts in contact and moving. In such cases, post-processing for smoothening is required and it is an extra step.
Comparatively, in injection moulding, there is no fuss about ridges and layers as the material is poured into a single layer and almost has a uniform and smooth surface finish. Additionally, injection moulded parts can be effectively post-processed.
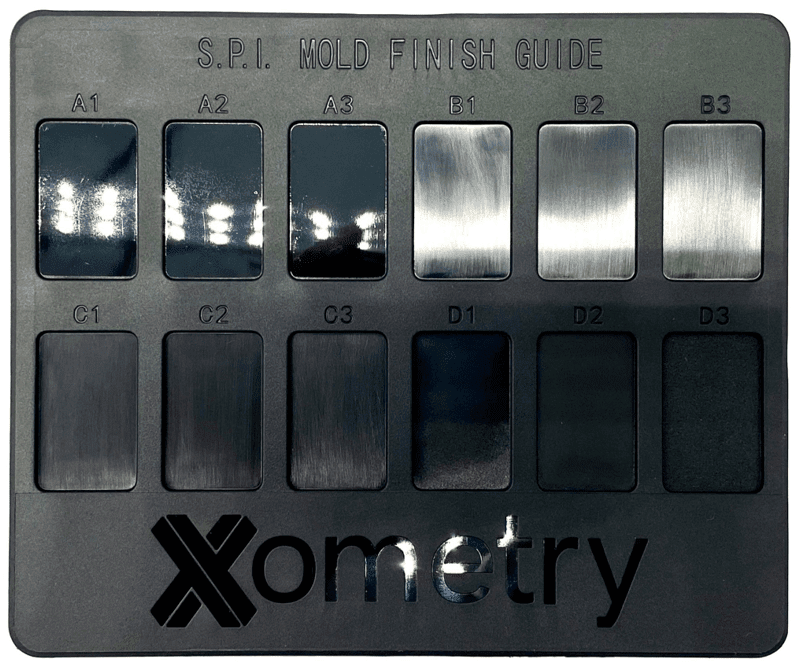
Conclusion: Injection moulding is preferred in terms of a good surface finish.
Material wastage
Since injection moulding pours material as many fits into the mould, it uses exactly as much as is needed for each design. That makes it a very efficient way to mass-produce objects without worrying about waste. On the other hand, some 3D printing technologies lose some materials in building the support structures and even though the material powder can be reused, it can only be done a few times without the material properties changing.
Conclusion: 3D printing produces little waste like support structures, failed prints that have to be removed during post-production, but when using it to produce a single unit or a small batch, the wastage is not so important, whereas, for large batches, the wastage is significant. Hence, if you want to have a large batch, it's good to go with injection moulding as there is no material wastage.
Summary
When you should choose 3D Printing | When you should choose Injection Moulding |
A small batch of units to print | Bulk production |
Complex part design | Priority to material strength |
Parts to be printed immediately | Good surface finish |
Prototyping and customization | No material wastage |
There is a general misconception in the manufacturing world that 3D printing can replace injection moulding and be a standalone winner in every aspect. Both these technologies have their own set of advantages and disadvantages. We at Xometry offer both injection moulding and 3D printing services with dedicated teams working to support you. Upload your designs to get a quote for your project.