A cutting fluid is a substance designed specifically for metal-working and machining processes that serves as both lubricant and coolant during these processes. This fluid is usually applied as the machining process is taking place. Cutting fluids may be applied by flooding, a fluid jet, mist spraying, etc.
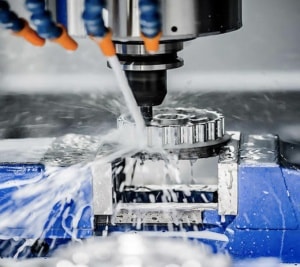
Types of cutting fluids
There are various types of cutting fluids differentiated by phase, composition, source, and method of application. However, they can be broadly classified as follows.
Soluble oils (emulsions)
Soluble oils are stable emulsions formed by the addition of mineral oil to water in specified proportions (usually 1-20% of oil to water). Other components that make up soluble oils are:
- Emulsifiers such as sodium sulfonate, which allow the oil droplets to mix with the water by decreasing the surface tension of the water;
- Additives which act as coupling agents or which improve corrosion resistance;
- Biocides which prevent the growth of bacteria;
- Anti-wear additives which improve lubrication.
Soluble oils are the least expensive and most common type of cutting fluids used in machining operations. They have good cooling and average lubricating properties. They are best suited to light cutting operations.
Straight oils
Straight oils are non-emulsifiable mineral oils used without the addition of water. Animal and vegetable oils are initially used as pure oil lubricants in metal cutting. Although their biodegradability makes them environmentally-friendly, they’re expensive and decompose fast. As a result of this, they are now only used as additives to petroleum and mineral oils to improve lubrication. Mineral oils are petroleum-based hydrocarbons obtained from the refining of crude oil. They may contain additives such as chlorine, phosphorus, and sulphur which are extreme pressure additives to reduce tool wear.
Synthetic fluids
These water-based fluids contender mineral and petroleum-based oils. They are formed by the solution of organic and inorganic chemical compounds in water, together with additives. Additives include lubricant additives, rust inhibitors, and corrosion inhibitors. All these additives improve properties such as lubrication which would otherwise be compromised by the water content of the fluids.
Semi-synthetic fluids
Semi-synthetic fluids are a combination of synthetic fluids, water-based fluids, and soluble oils emulsions. They contain a mixture of 5-50% mineral oil, additive, and chemical compounds which dissolve in water to form microemulsions with particle sizes of 0.1-0.01mm. Semi-synthetic fluids combine the properties of both soluble oil and synthetic fluids.
Functions of cutting fluids in CNC machining processes
Cooling
During metal cutting machining processes, heat is generated in the workpiece, chips, and cutting tool due to the friction between the cutting tool and the surface of the workpiece. Heat is also generated as a result of the plastic deformation of the metal at shear zone. This heat has a number of undesirable effects including thermal expansion, chemical reactions such as oxidation, welding of surfaces and many more. A cutting fluid serves to cool the tool and the workpiece, thereby preventing these effects.
Lubrication
The main cause of heating during machining is friction. The combination of heat and friction tends to weld surfaces together. Cutting fluids reduce friction by creating a thin layer between the chip and the tool, effectively reducing contact between them. Lubrication also reduces abrasion of the cutting tool and lowers the energy consumption of a machining process.
Prevention of corrosion
Rust and corrosion inhibitors present in cutting fluids prevent the corrosion the machine parts and the machined surface. Mineral oils cutting fluids prevent oxidation by forming a very thin protective layer over exposed surfaces.
Improvement of tool-life
By dissipating heat, reducing friction and abrasion, and preventing corrosion and rust, cutting fluids greatly reduces tool wear, subsequently improving tool life.
Removal of chips
During certain machining processes such as milling and drilling, chips tend to accumulate around the cutting zone. A build-up of these chips may inhibit cutting. Cutting fluids also serve to flush away chips from the cutting zone.
Enhancement of surface finish
By preventing thermal expansion and property changes in a workpiece, cutting fluids contribute to a good surface finish of machined parts.
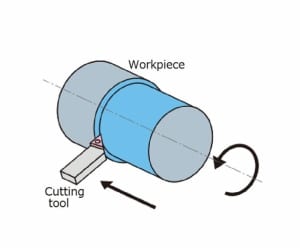
Figure 2: Contact between the cutting tool and workpiece in turning operation
Properties of a cutting fluid
The following are some of the properties a good cutting fluid should have.
High thermal conductivity
Thermal conductivity is a measure of how well a substance can conduct heat. In the case of cutting fluid, how well it can conduct heat away from the workpiece and the tool.
High heat capacity
The higher the heat capacity of cutting fluid, the more heat it can absorb before it gets hot or boils.
Low viscosity
The low viscosity of a cutting fluid allows for easy flow. It also prevents the formation of sludge by the mixing of chips with the fluid.
Non-corrosive
A good cutting fluid should not attack the workpiece or tool.
Corrosion and oxidation resistant
In addition to not being corrosive, a good cutting fluid must also prevent corrosion and oxidation of parts.
Non-toxic
Considering the fact that it is likely to come in touch with either humans or the environment, a good cutting fluid must not be toxic to both.
Chemically nonreactive
Cutting fluids must not carry out chemical reactions with the surfaces they come in contact with. This not only damages these surfaces but also degrades the fluid.
Odourless
To avoid any lingering smell on either the machine or the machined part, a good cutting fluid must be odourless.
Sufficiently clear (transparent)
A good cutting fluid should be sufficiently clear so as not to inhibit the view of the workpiece.
Stability
A good cutting fluid should not degrade quickly with use or when stored.
Methods of application and usage of cutting fluids in CNC machining
The functions of cutting fluids mentioned above apply to CNC machining processes. However, there are various machining processes with various methods of application.
CNC Milling
In CNC milling operations, your workpiece stays stationary while the cutting tool moves. In this operation, cutting fluid is best applied by flooding.
CNC drilling
The main purpose of cutting fluids in CNC drilling is chip removal and cooling. Lubrication is not really necessary as the possibility of built-up edges forming is low. Jet application of the cutting fluid is recommended.
CNC turning
This process occurs at very high speeds therefore cooling is crucial. Considering that the workpiece rotates. Jet application of the cutting fluid is suitable.
Selecting the right cutting fluid for your CNC machining process
The selection of a cutting fluid depends on a number of factors including cutting tool type, workpiece material, and machining operation.
Cutting tool type
Carbide tools can get very hot. This makes them more susceptible to thermal shocking, the phenomenon in which different parts of the cutting tool expand by different amounts. Synthetic cutting fluid with very high cooling capabilities is recommended for this tool type.
High-speed steels also get hot, but not as hot as carbide tools. Soluble oils and semi-synthetic fluids are suitable.
Workpiece material
Metals are the most common workpiece materials which require cutting fluids. The following are some of the most machined metals and their suitable cutting fluids.
- Steel – Mineral oils containing lubricant additives
- Alloy steels – Sulphur brass oil or mineral oil
- Aluminium – Soluble oils or mineral oils without active sulphur (active sulphur stains aluminium)
- Copper – Soluble Oils
- Stainless steels – Mineral oils containing excellent Extreme pressure additives
- Cast iron – None
Machining operation
Relatively easy machining operations such as turning, milling, forming, and drilling take place at relatively high speeds. At such speeds, a high level of cooling is required. Only modest lubrication and extreme pressure properties are required. As such, synthetic fluids are best suited for such operations. Although soluble oils may be used
On the other hand, difficult machining operations such as broaching and thread cutting require good lubrication. These operations take place at low speeds and high pressures, therefore cutting fluids with excellent lubrication and extreme pressure properties are required. Mineral oils containing extreme pressure additives are the best choice.