A few years ago, 3D printing had been a far fetched dream even in industrial applications. It was hardly used even for prototypes but now, the times have come where technology is seeping into the daily lives of people. From housing for electronics to many interesting DIY projects, 3D printing has become the go-to option for professional product designers to hobbyists.
Why 3D printing in the consumer segment?
Easy customisation
3D printing offers easy customisation. For example, previously, when one needed a pair of earphones that fit exactly, one had to get them custom made which would cost extra money and time. Something even more complicated is, if one ear fits and one doesn't. The best solution is getting the earphones 3D printed. This not only applies to earphones but also to many wearables like watches, shoes etc.
Rapid prototyping
If a jewellery designer wants to check and analyse how his or her design looks in the final stage, they can easily do it with the help of 3D printing by designing its prototype for a cost as low as 1/20th of the original. That holds the same for any consumer goods from PET bottles to expensive jewellery. Cheap 3D printing technologies like FDM are efficient for prototypes and technologies like SLA provide high definition.
3D printing in consumer products
The customer applications of additive manufacturing can be divided into two main categories:
Commercial use of 3D printed consumer products
In this segment, the consumer buys a 3D printed desired product, irrespective of the process. Meaning he doesn't build a part step by step but purchases an already existing item from the market. There are many examples of this type.
3D printed eyewear
Canadian eyewear manufacturer Specsy has successfully harnessed 3D printing to the optic industry. Their AI-enabled app scans the consumer’s face and customises the eyewear he/she selects to his exact size and liking. To do so, the manufacturer used SLS 3D printing which is ideal for complex designs. The rest is just assembling various parts of the eyewear and delivery to the customer.
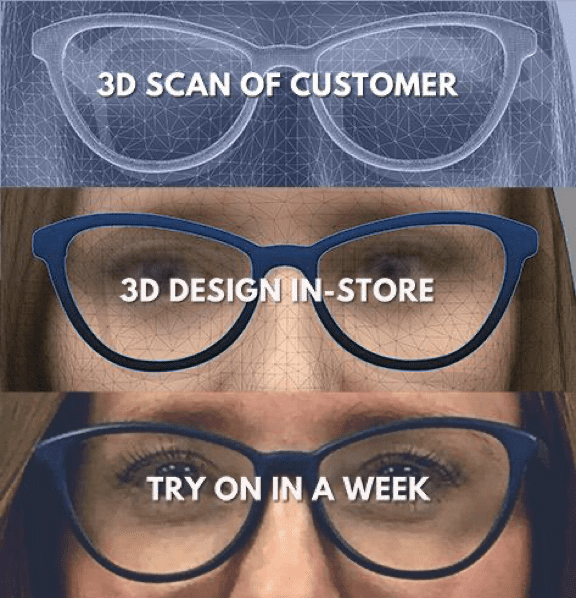
3D printed dental aligners
US-based teledentistry startup SmileDirectClub, teamed up with HP, produces transparent and clean dental aligners according to the 3D printed mould of the customers’ dental alignment. The process starts with the company providing the customers with their moulding kit (called “home impression kit”) which is in turn sent by the customers on using, along with a few digital photographs.
HP’s Multi Jet Fusion 3D printing machines print the exact dental alignment from the customer information and the transparent retainer is designed according to the information.
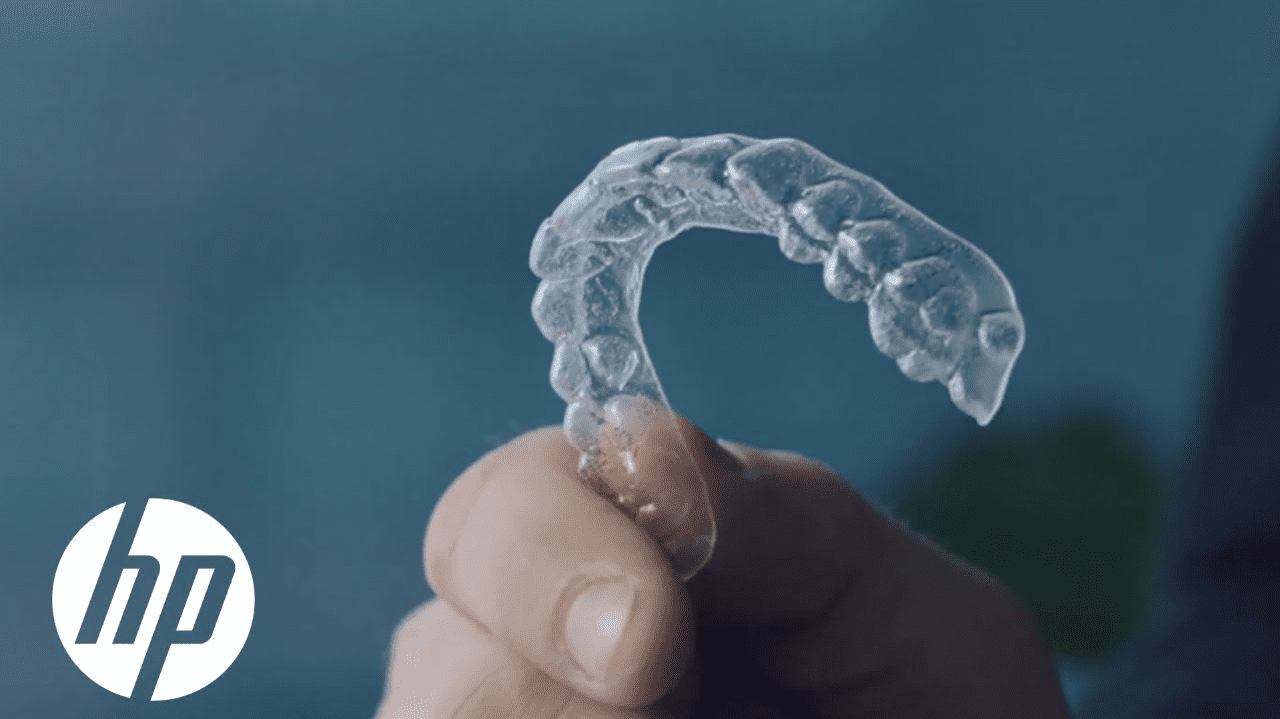
3D printed insoles
A famous footwear brand Dr. Scholl’s utilises AM in producing its customisable insoles. The company’s collaboration with technology company Wiiv and through a mobile app technology called Wiivv fit, scans the customer’s foot and maps at least 400 mapping points and exactly finds out customer-specific foot shape and size.
The company then prints the customised insoles and delivers them to the customers. The company uses FDM technology to achieve the customisation cheap and efficient.
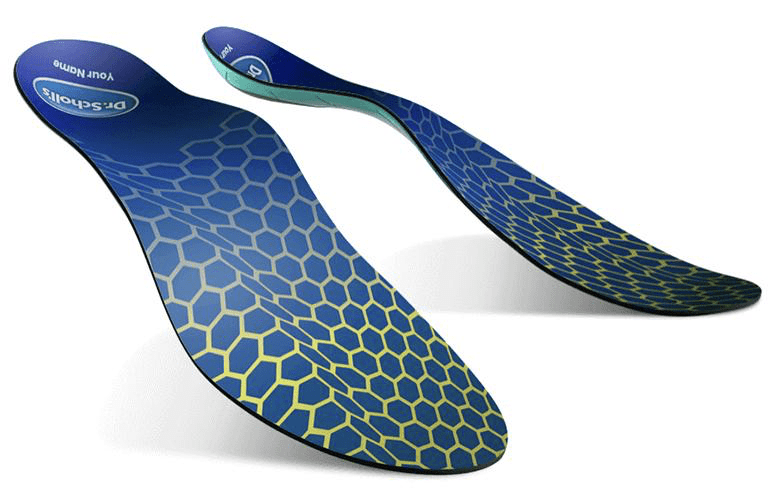
3D printed mascara brush
With the use of SLS technology, beauty and cosmetics company Chanel is mass-producing mascara brushes that are unique in their design and functionality. AM also enabled the company to iterate its design and research 100 times.
The unique feature of this brush is its microcavities that absorb more mascara and avoid the need to re-dip. The granular texture of the individual stands also facilitates the uniform distribution of the mascara on the eyelashes.
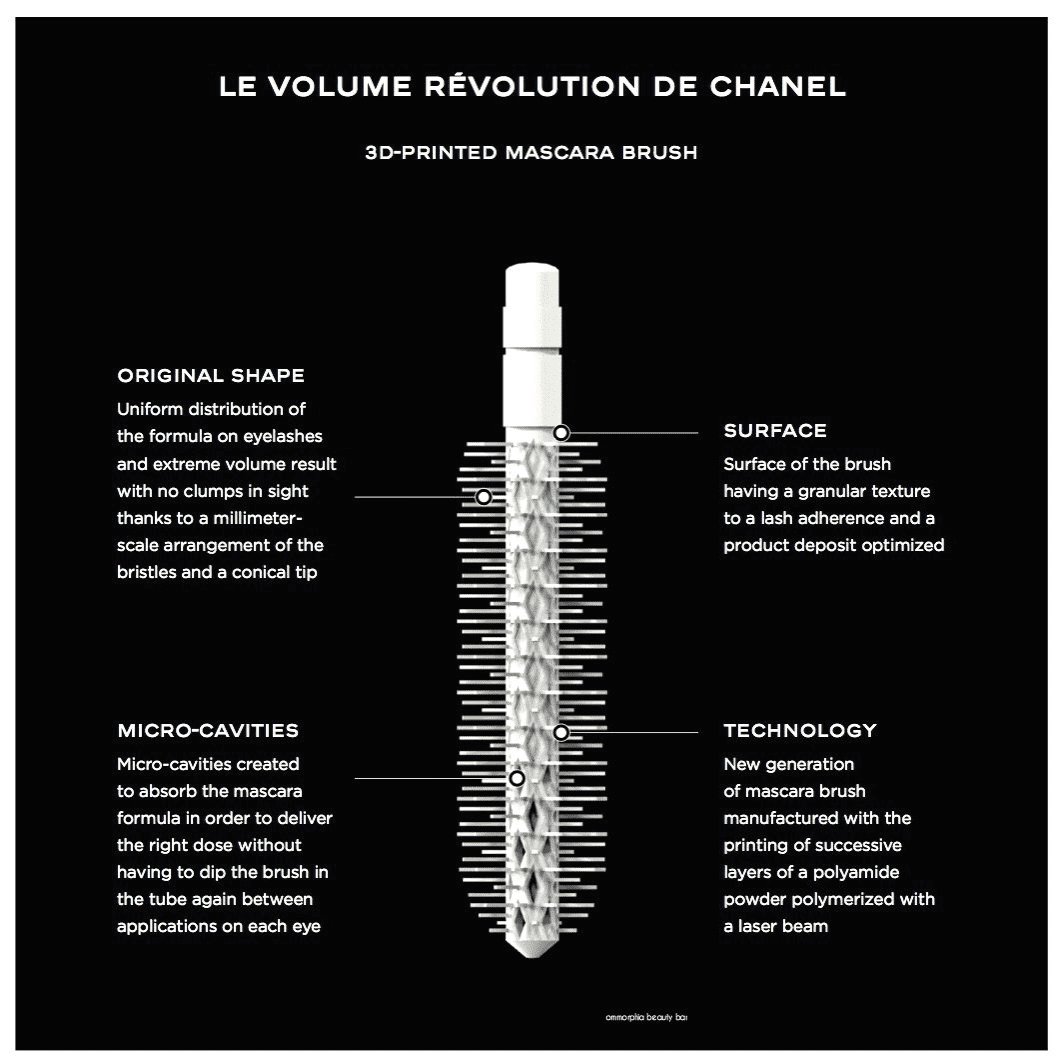
3D printed shaving razors
Famous personal care brand Gillette is utilising SLA technology in the manufacturing of its razor handles. They are being customised according to the needs of individuals to give them optimum experience and resistance against wear from daily usage.
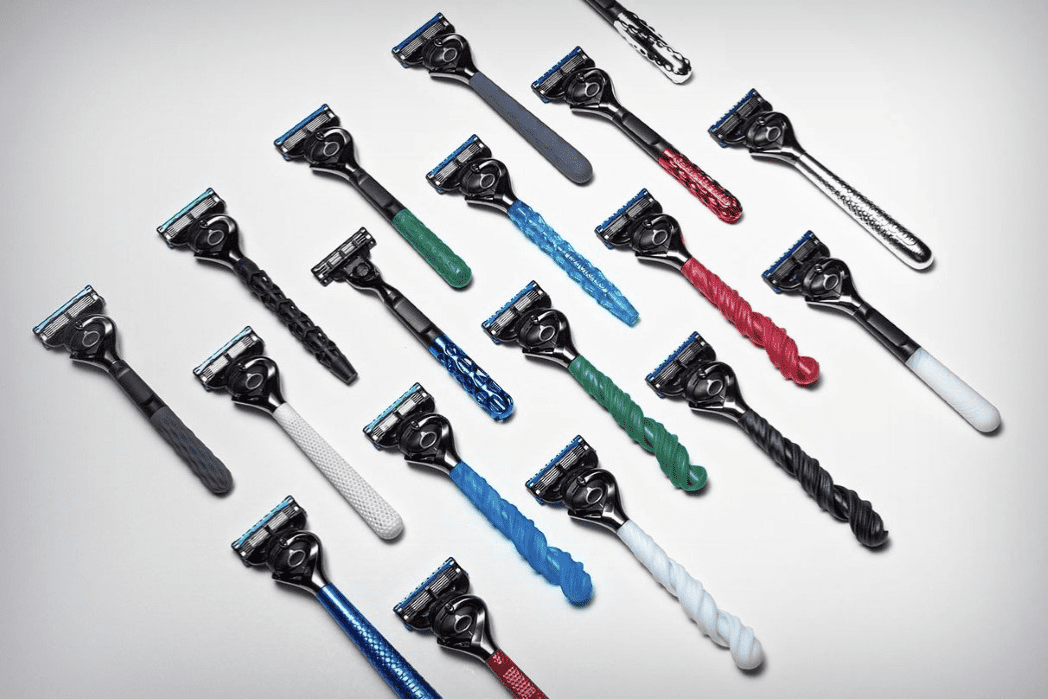
3D printed bicycle components
Reynolds Technology Ltd, along with Renishaw PLC, has built a stainless steel bicycle frame with optimised 3D printed parts. It has also made Titanium frames and dropouts for the bike with the use of metal 3D printing. Additive manufacturing gave much scope for experimentation and the design was made hollow, allowing for light-weight and efficiency.

3D printed bike helmets
London based startup Hexr helmets has started using AM in its bicycle helmets. They are using a honeycomb structure in their helmet design, which allows them to customise each item to the customers’ head size and shape.
Thanks to polyamide material and SLS technology, the helmets are very lightweight and efficient. They proved to be one of the toughest in the market.
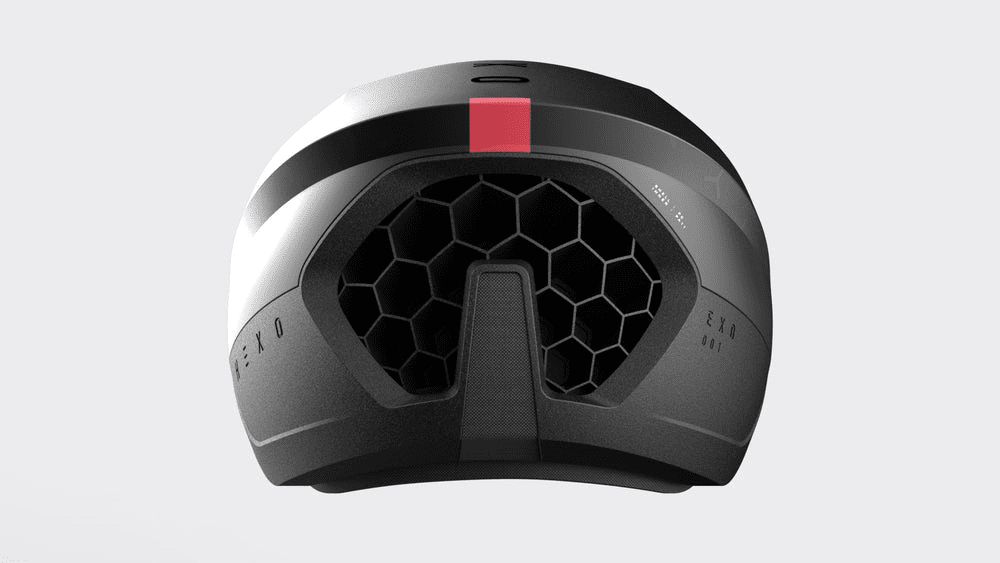
A consumer using a 3D printer
This section focuses on how customers can use 3D printing technologies on their own i.e in-house printing.
Desktop 3D printing
Apart from the expensive printers available in the market, there are cheap and efficient counterparts of those that are mainly aimed at in-house production for small-time designers and hobbyists alike. The cheapest of printers of FDM is already available at about 200€, providing a lot of scope for innovation and self customisation of products they use.
Desktop SLA machines are also available but are a little expensive. All the customers need is a little design knowledge and a few tips on how to use the printer.
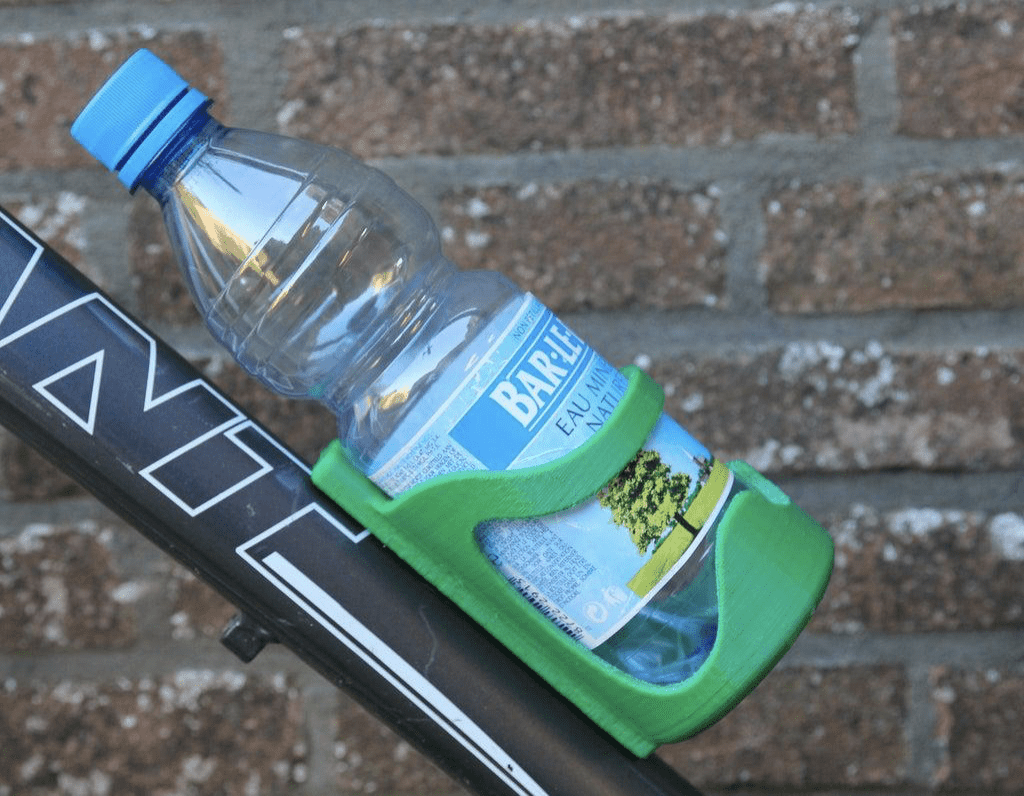
Print from digital catalogue
In order to print anything on a 3D printer, one does not need mandatorily to possess good skills at designing, but a good internet connection. One simply needs to download designs and follow the exact instructions on how to achieve the product. Designs like the above water bottle holder are available on the internet for many simple consumer goods like flower vases, cell phone cases etc.
Conclusion
3D printing makes the complex manufacturing process very simple and easily understandable to the customer. Be it the daily goods one purchases or the goods one manufactures oneself, there is always room for innovation with additive manufacturing.
Xometry Asia offers 3D printing services for many materials. Upload your CAD files and get an instant quote for your project using our instant quoting platform.