One of the processes Xometry offers includes injection molding. Injection molding is a feasible solution for mass manufacturing of high-quality parts by using many thermoplastics. For more information, please see Xometry Part Design Guide and injection molding options on our website. If you are designing for injection molding, you should avoid the 5 common mistakes that designers and engineers often make.
Without draft angle
Draft angle is required in the mold to release the plastic parts from the mold. Plastics usually shrink toward the center of the part. Without the draft angle, the part will stick to the mold and cannot be released correctly. If possible, design 1° draft angle on each side as any draft angle will help release the part.
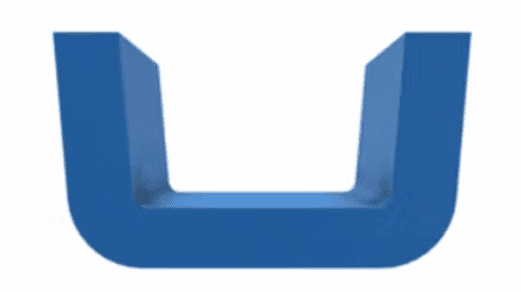
Uneven wall thickness
Different wall cross sections are common in part design and can lead to unexpected part characteristics during molding. It is difficult for plastics to flow and transit between uneven wall thickness. Thick wall sections produce different contractions, which can cause the deformation of the parts. Please ensure that the wall is thicker near the gate area and thinner at the end of filling. Aim for a wall thickness of 0.080 to 0.120 inches and use rib and angle brace features in part design.
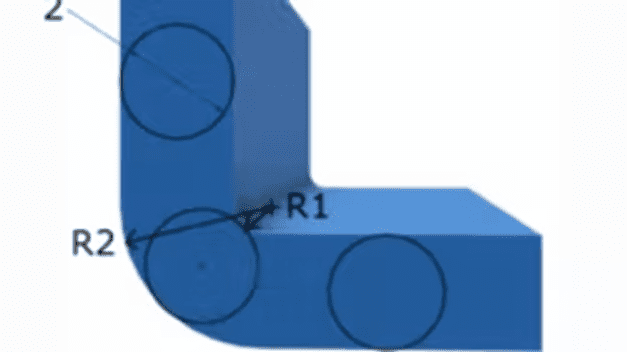
Unnecessary dent
Due to the complexity of present part design, dents are designed but are often overlooked. Dents in the mold need to be dealt with before the parts are demolded, otherwise, it will damage the parts. When molds are treated, many methods, such as core design, sliders, cores or lifts, can be used to solve the sag problem. A simple rule of design is as follows: Dents + complex molds = higher cost.
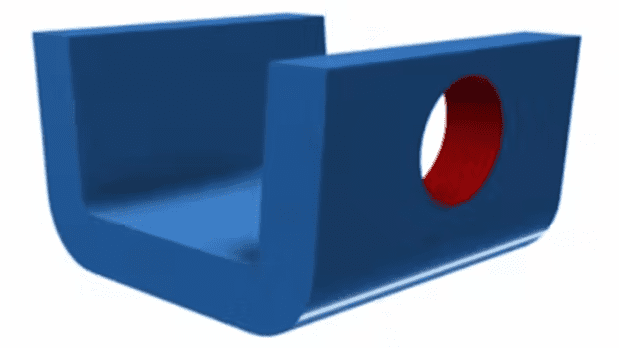
Wrong material
Another common mistake often happens when choosing materials. The choice of material should be based on the location of the parts. Parts that will be used outdoors should be equipped with UV stabilizers to prevent cracking. The parts that bear the load should have fillers to strengthen them, such as fiberglass. Parts with bearing surfaces should have additives such as lubricants.
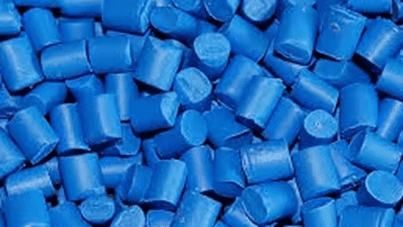
Fillet radius is not included
During parts design, the fillet radius is often ignored. The fillet radius can strengthen the area, making it sturdier in the long run. The radius reduces stress concentration and fracture in plastic parts. It also makes the parts look artistic and reduces the risk of injury while they are carried.
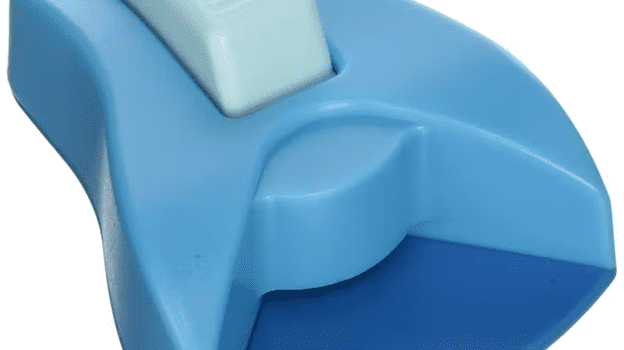