- Industry: Aerospace
- Manufacturing process used: CNC milling
- Challenge: Facilitating cost-efficient, reliable and environmentally friendly biomedical research in space.
- Solution: CNC-milled aluminium rings for the Inflatable Atmospheric Decelerator (IAD) component.
Atmos: Aerospace pioneers in biomedical research
Atmos is an emerging aerospace company specialising in the development of innovative technology for re-entry control of space capsules. The company was founded about two years ago by Sebastian Klaus, an aerospace expert with a passion for re-entry technology, which has now grown into a team of 20 people. Atmos has developed an inflatable heat shield, called the Inflatable Atmospheric Decelerator (IAD), which makes it possible to bring space capsules back to Earth from orbit in a cost-effective and safe way. This is a major step towards reducing the costs of space missions and facilitating access to space.
Thomas Kern, Head of Structures at ATMOS says: “The cool thing is that we are doing pioneering work here, so we are actively helping to establish commercial transport into space and back—sort of like the DHL of space.”
Research in space: affordable, reliable and environmentally friendly
Researching biomedical sciences in space, particularly for monoclonal antibodies, stem cells, organoids, and protein crystallisation, offers unique opportunities. Launching experiments in space has become easier and cheaper. However, the challenge is to bring the experiments back to Earth safely and affordably. High costs, long lead times, and problems with repeatability and reliability complicate the return process. The prices for existing solutions, such as SpaceX’s Dragon, are relatively high as there is currently a monopoly in this field. This is set to change with Atmos developing a cost-effective solution to bring space capsules back to Earth safely and economically.
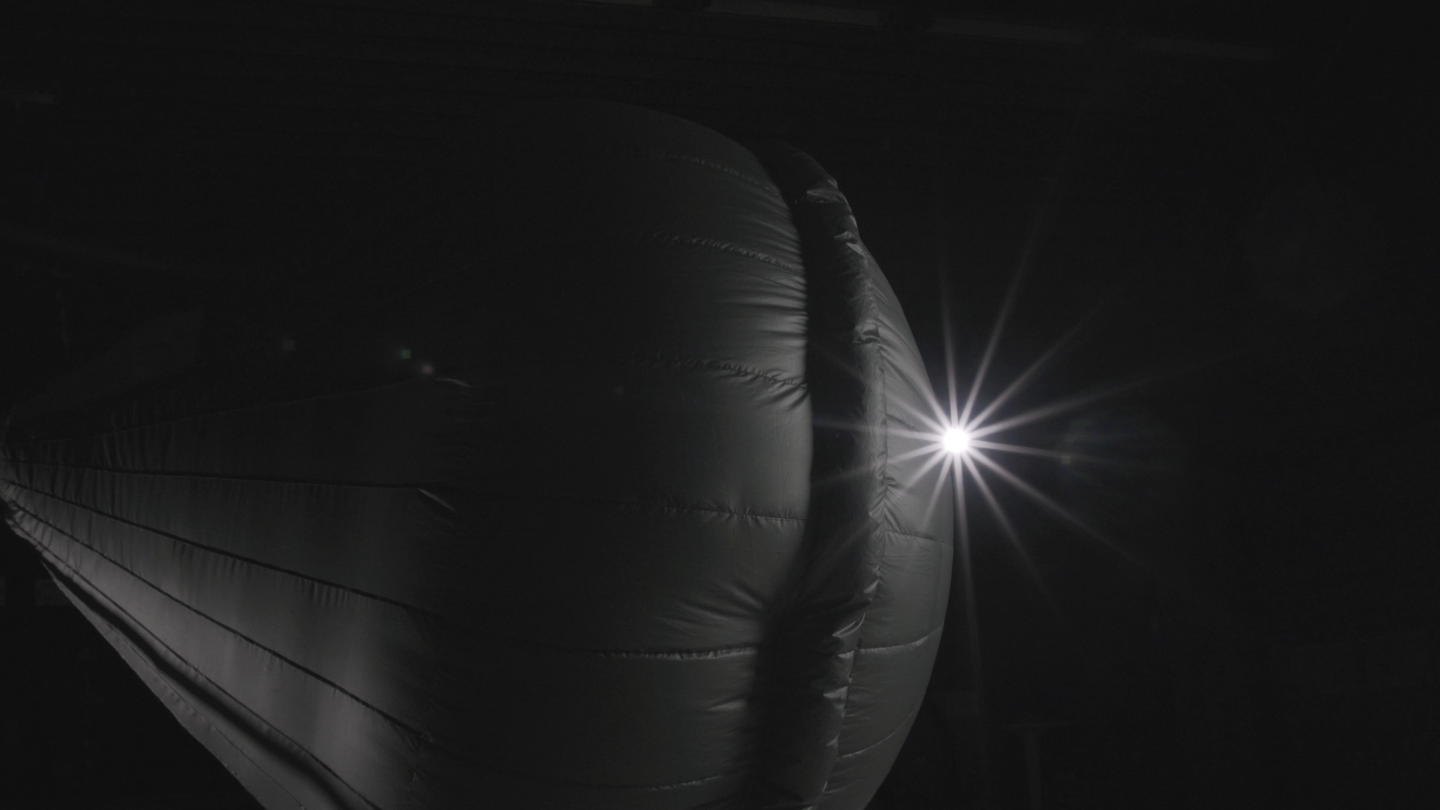
Phoenix Return Capsule and Inflatable Atmospheric Decelerator
The Phoenix Return Capsule is a core element of an innovative space return service that enables the cost-effective and reliable return of valuable biomedical research experiments from space to Earth. This service is aimed at pharmaceutical companies, researchers and institutions working in life sciences, particularly in the field of monoclonal antibodies, stem cells, organoids, and protein crystallisation.
The Inflatable Atmospheric Decelerator (IAD) is another key component of this system. This system serves as a heat shield and high-speed parachute, protecting valuable cargo during re-entry into the Earth’s atmosphere. Unlike the usual method of rocket-assisted landing, which is becoming increasingly standard in the industry, this technology does not use propellant. This is not only better for the environment, but also makes the solution lighter and more cost-efficient. In fact, the IADs are so light that they can be used to recover and reuse complete microrockets. The technology can also be retrofitted to make virtually any rocket stage, space station, or satellite fit for return flight and reuse.
The Inflatable Atmospheric Decelerators (IADs) are integral to the ATMOS service. This technology functions as both a heat shield and a high-speed parachute, protecting valuable cargo during the re-entry phase into the Earth’s atmosphere. Unlike the usual method of using propulsive power to land, Atmos’ IADs do not use propellant.
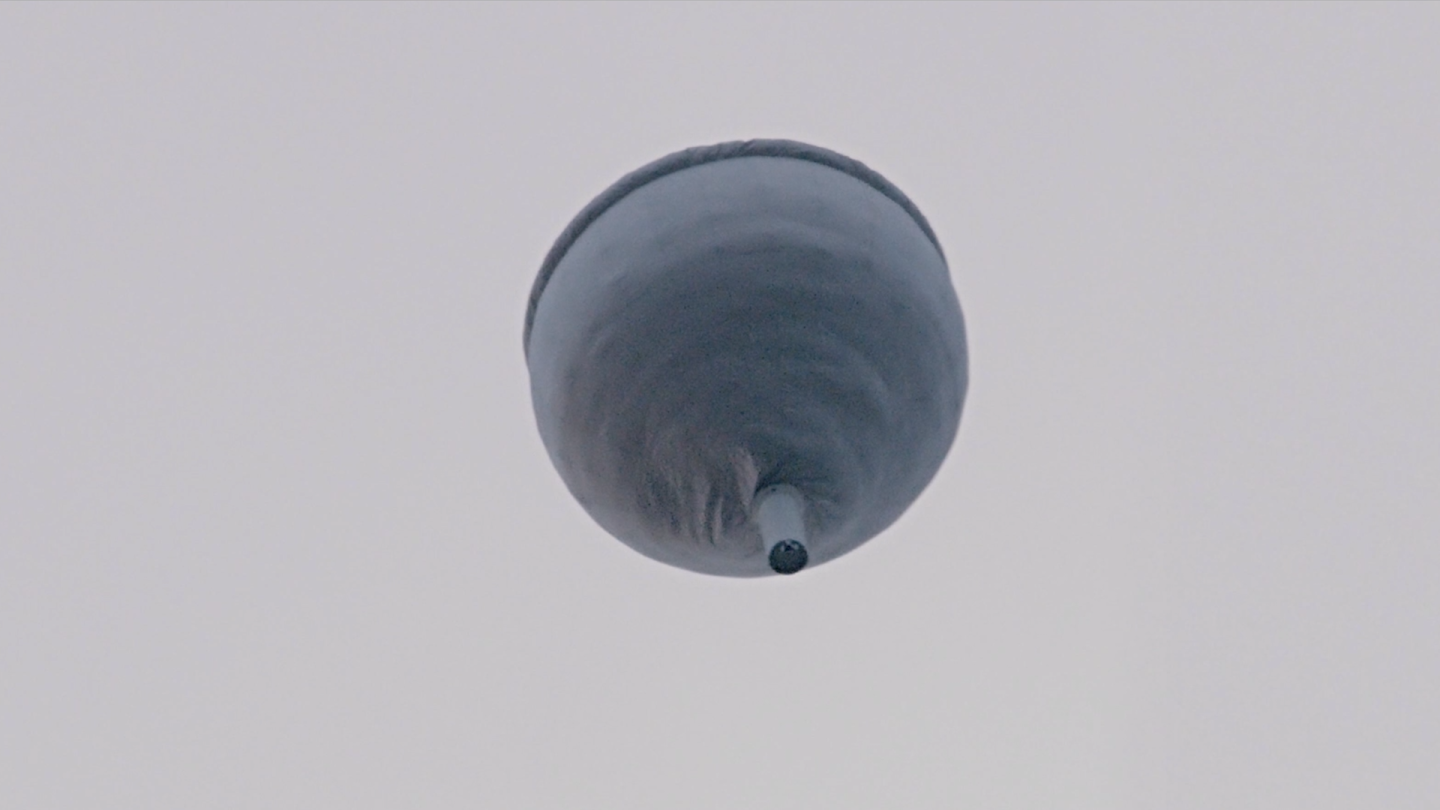
This not only makes the solution more environmentally friendly, but also lighter. In fact, the IADs are so light that they can be used to recover and reuse complete micro-rockets. This technology can also be retrofitted to make virtually any rocket stage, space station or satellite fit for return flight and reuse.
Atmos was looking for a reliable partner to produce the custom rings for the IAD. They came across Xometry, whose on-demand platform enables companies to find fast and cost-effective solutions for the production of parts.
Xometry CNC-milled the 18 rings from 7075 aluminium. This high-strength aluminium provided the necessary stability and low weight. These rings help Atmos ensure that the space capsules are correctly secured to the IAD during the re-entry process.
“The rings are critical components, everything literally depends on them,” states Kern.
Uncomplicated and efficient parts procurement with Xometry
Kern describes the collaboration with Xometry as follows: “I have to say, I think the Xometry concept is excellent.”
He knows exactly what is involved in procuring parts the traditional way: the fiddly process of making an enquiry, then having to wait for an indefinite period of time until a quote is created manually, only to receive a price that does not meet expectations after perhaps two weeks of waiting, resulting in a substantial loss of time.
“But with Xometry, it helps that there is an algorithm to instantly provide a price and a binding quote when you upload your part design. I thought that was amazing. Then you just complete your order and get a delivery date, which was met in our case,” adds Kern.
Kern continues: “Wow, what a great process to work with!”
Reaching for the stars: capsules, rings and looking to the future
Atmos has ambitious plans for the future, including the first flight of the Phoenix capsule by the end of 2024, and the company has already attracted investors who share this vision. With the support of Xometry and other partners, Atmos hopes to make a significant contribution to opening up space for future generations. As a result, the technology can be further developed and expanded. The next step could then be to transport rocket upper stages. Looking even further into the future, it could even be used in mining to establish a cargo transport system, which is interesting for rare elements or platinum. The future is bright for Atmos and Xometry will always be ready to help with its expertise and high-precision parts.