- Industry: Automotive
- Manufacturing processes used: CNC machining, sheet metal cutting
- Challenge: Rapid delivery of parts to meet driving simulator order requirements
- Solution: Working with Xometry to find the best suppliers and source high-quality, mass-produced parts
Since 2004, Develter Innovation has been developing state-of-the-art driving simulators. These simulators are aimed at both professional drivers, to improve their driving behaviours, and people with reduced mobility, to help them return to driving in a safe manner. Regardless of the target audience, the team always designs its products with enhanced road safety in mind.
To develop this simulator, Stephane Develter worked with Alcide System, managed by Frédéric Vanhove, as his design office. This work initially addressed the electrical part, with studies and harnesses, then covered more and more components, until Develter trusted Alcide System with the full design and production.
A Multi-faceted Product
Develter sought to extend its range of simulators to respond to the needs of several audiences. Initially, and after several trials, the simulator base was standardised using identical parts. By adapting different components, the simulator now meets a wide range of needs. For example, by changing the steering wheel, the simulator can be used to meet the requirements of a transport company, or to help people learn to drive again after paraplegia.
All the accessories have been awarded the “CE” mark, which means that the products can be marketed throughout the European Union. In 2022, the company won the Road Safety Innovation Award (prix de l’innovation en matière de sécurité routière), and in 2023, the Auto Moto magazine Professionals Award (prix Pros de l’Auto de auto moto). These awards are testimony to the added value of the Rehab simulator.
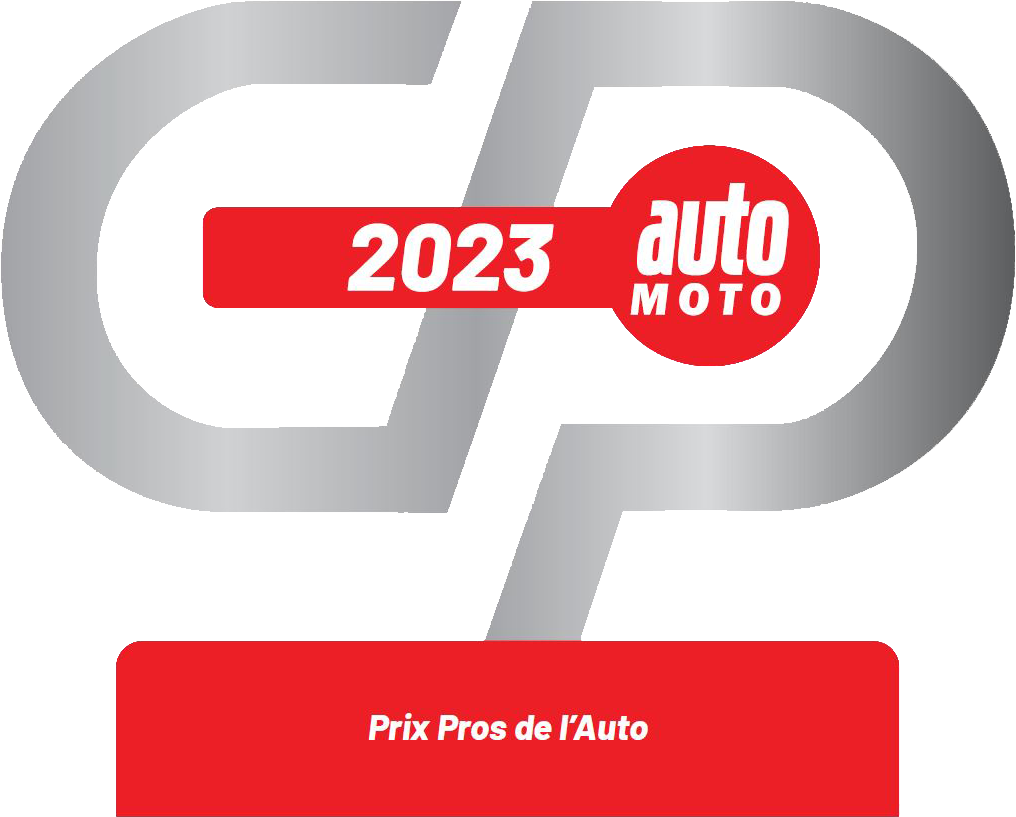
Functional Challenges in the Development of the Simulator
The concept of continuous development brings the challenge of manufacturing parts quickly and using a variety of technologies.
For example, it took three generations of simulators to achieve the exact desired feel of the brake pedal. The initial position sensor has been developed into a force sensor that gives a feel almost identical to that of braking a car. To achieve this, different elastomer springs were installed along the pedal, as well as a gas cylinder to replicate the compression sensitivity.
In addition, all tolerances had to be adapted to fit bearings to guide the various gearbox axles. Unlike a conventional car, it had to be possible to run wires to collect data from the simulation, which required specific machining. All the stresses on the gear stick were designed and tested to ensure correct feedback.
“Discussions with Servane Freneat (Key Account Manager for France) about the gear knob were crucial in finding the best manufacturing process and achieving a result that was as close as possible to a production part,” explains Vanhove. “Unlike other companies and suppliers, I actually got to deal with a human contact.”
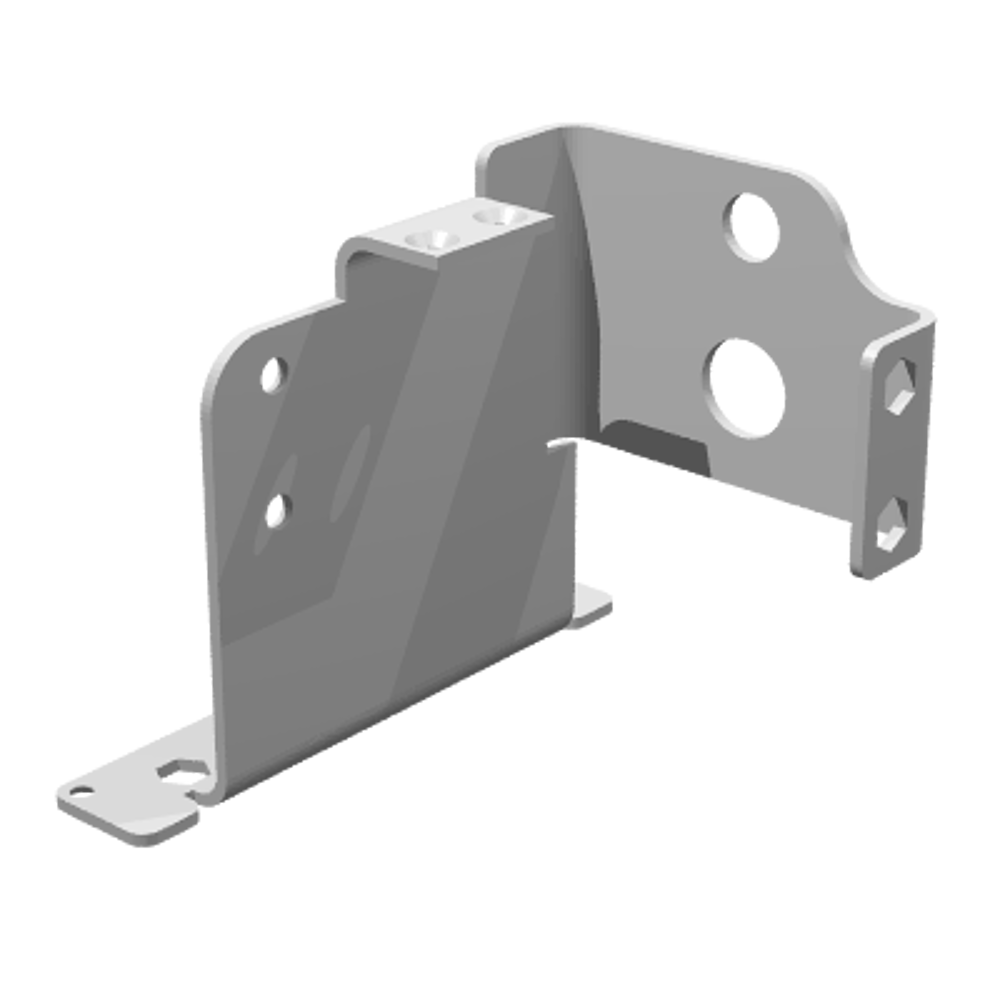
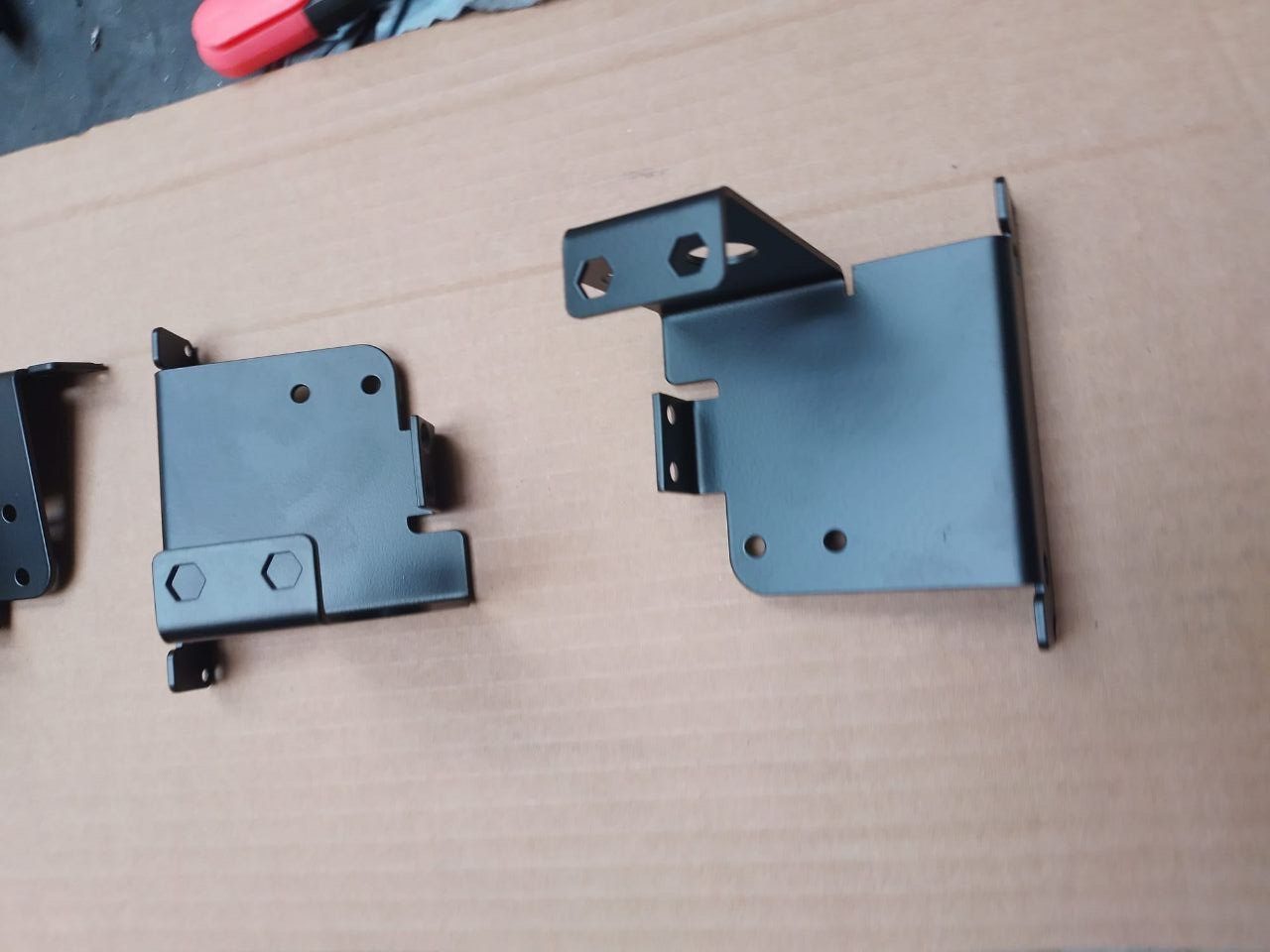
Xometry’s Speed and Flexibility
“I used the Instant Quoting Engine to get an initial idea. I got a quote back very quickly and was able to change the materials to see how it affected the cost,” says Vanhove.
They were pleased with the quality of the first part, so asked Xometry to produce the vast majority of the parts making up the simulator: “The mechanics of the pedals, the push-pull mechanism, the gearbox, the H7g6 adjustments, as well as the parts that make up the chassis (laser cutting in 10mm thick steel), folded sheet metal painted black for the bulkhead… Everything that isn’t automotive equipment, springs or thermoformed plastic parts was produced by Xometry.”
The automation of the Instant Quoting Engine combined with the responsiveness of the Xometry team allowed Develter to meet the deadlines set. “The responsiveness has always been there and allows us to fulfil our customer orders,” says Develter.
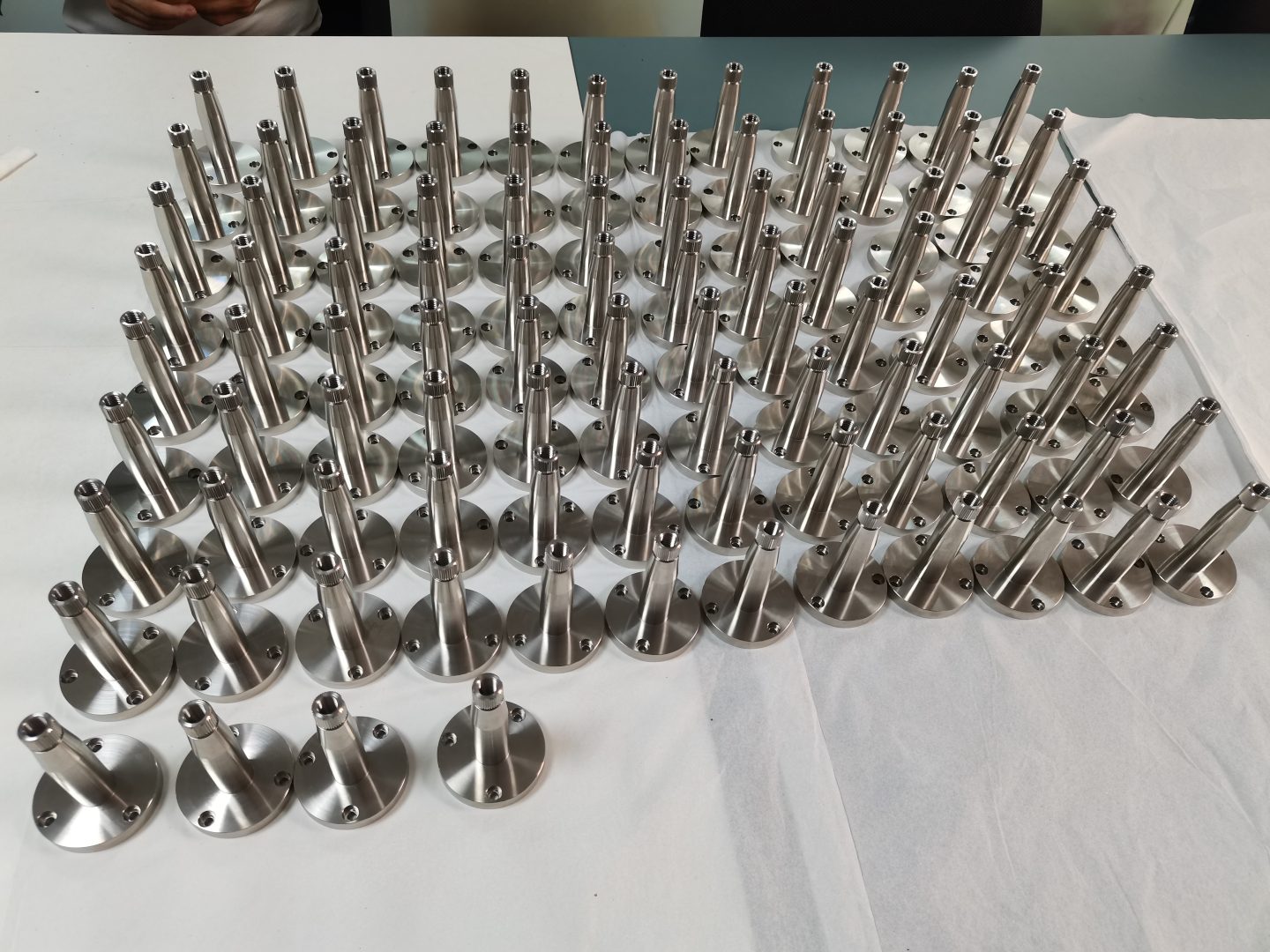
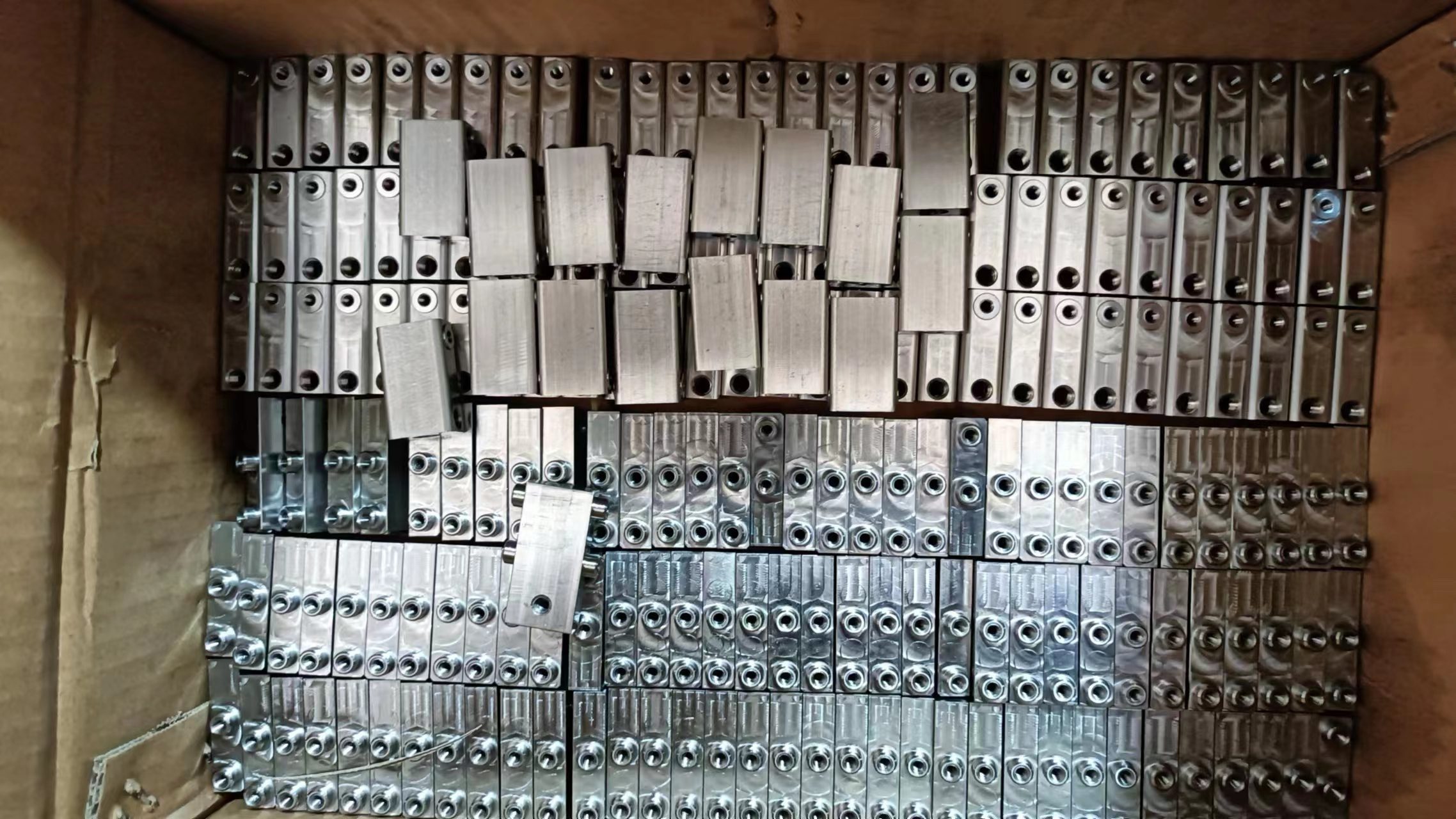
Gearbox parts
What Does the Future Hold for Develter Innovation?
Develter continues to innovate. Among the most noteworthy new features for 2023 are a sensory system to give simulators a better feel and the ability to divide the simulation cabin into two parts, to allow patients to stay in their wheelchairs.
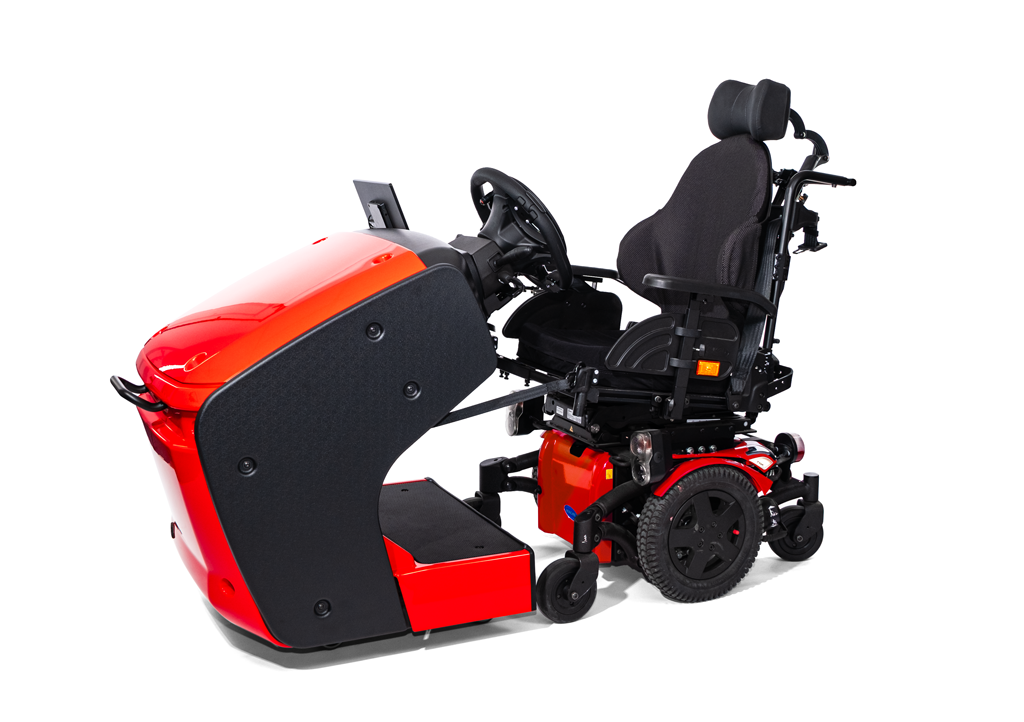
From next year, the company plans to market a new, more ergonomic version of the simulation software, with updated settings. It is also setting up an international distribution network to market the REHAB EVOLUTION II. This strategy is modelled on the success it has enjoyed in France in the rehabilitation market with MEDIMEX, where over 100 simulators have been installed.