Xometry helps the automation company Asitech in its growth project: from custom-made prototypes of automated equipment to small series, through the fabrication of metal parts with CNC machining.
- Industry: Electronics, Machine Building, Manufacturing
- Technology used: CNC machining
- Challenge: To move from prototype production to small production runs
- Solution: Use IQE to test the most efficient solutions and global network to produce aluminium and steel components
When it comes to Automation, the needs of manufacturing companies are often different. Asitech, the Italy-based company that has been providing automation and systems for the industrial sector for more than 20 years, knows this too well. Here is the story of the company and its recent collaboration with Xometry.
Automation Between Past and Future
The company was founded in 1998 as Automazioni Noris, and in 2002 founder Noris Abele together with other partners formed Asitech, Automazione Sistemi e Impianti. Initially, the focus was on civil and industrial electrical systems, then it expanded to automation, following Mr. Noris’ passion for machines.
“Almost all our production is custom,” Elena Ceruti confirms, “we build machines according to the needs of our clients, which range from manufacturing to chemical-pharmaceutical. We used to work only on prototypes and one-off pieces, but we have been expanding our offer for a few years now, because some customers ask us for small, more substantial series. Our core business remains industrial electrical systems and automation, but they also ask us for lighting or photovoltaic systems.”
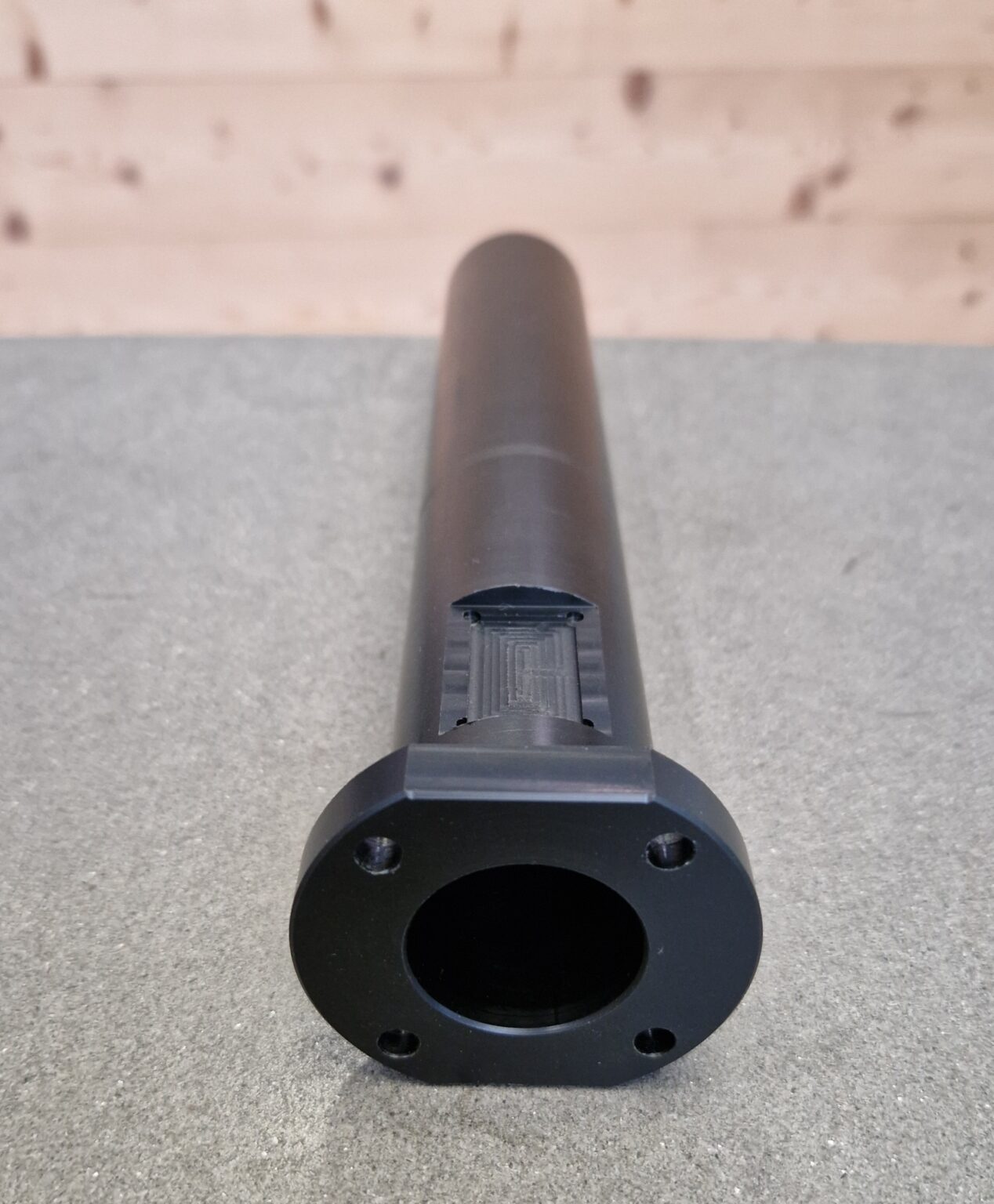
POM grip for heating paddle
Standardized Processes for Unique Products
Asitech’s production processes have a standard pattern: it always starts with an interview with the customer to understand together how to optimise processes. Then, a design is made and shared with the customer for approval; after which, the in-house laboratory comes into play for production. Finally, the plant is assembled in-house, with the testing phase taking place for both plant and software parts.
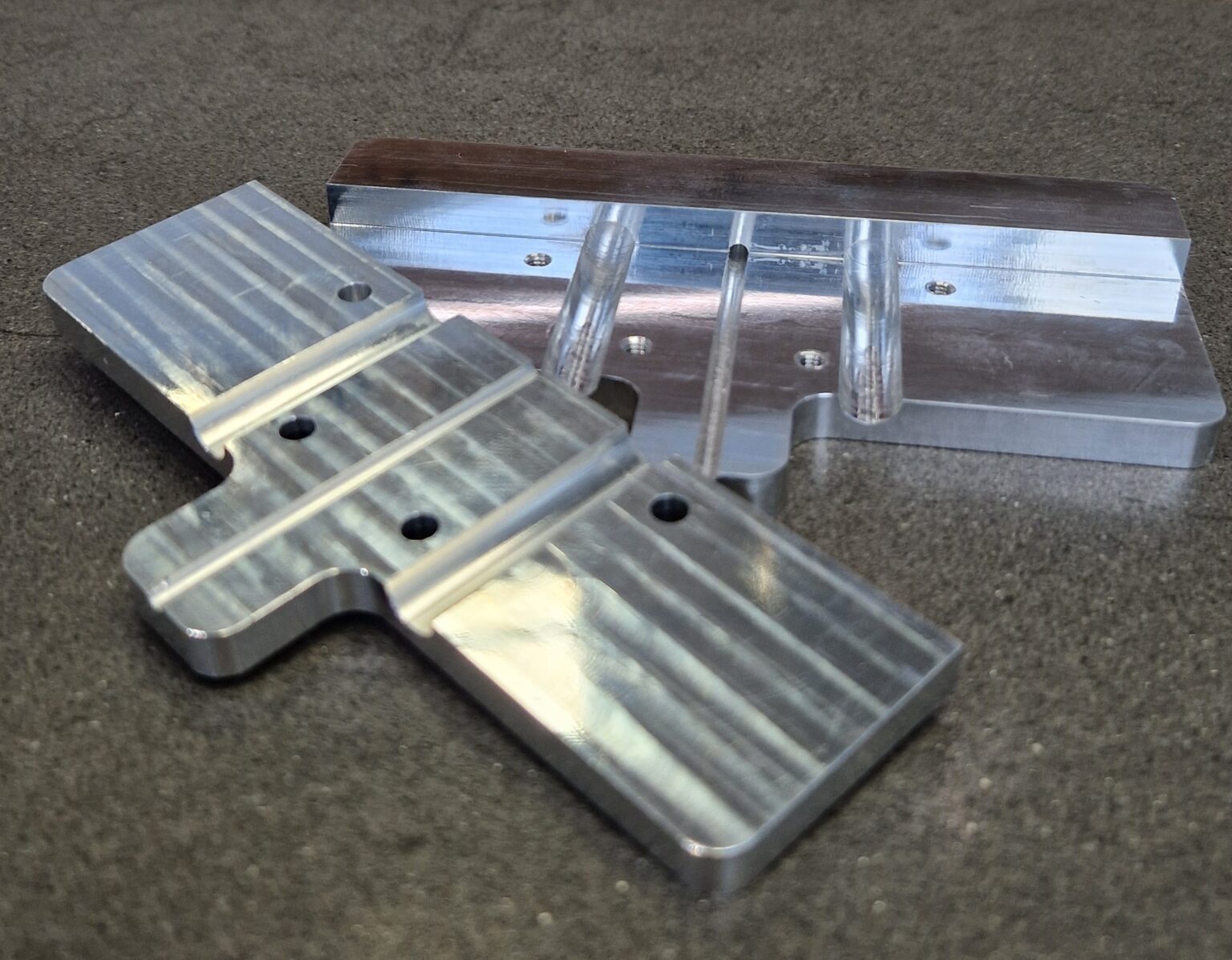
Aluminium heating components
Instant Quotes: the Collaboration With Xometry
Asitech is in a phase of change: from the production of single prototypes to the production of small series, always on-demand. That’s when, searching the Internet for suppliers who could help in this new production challenge, the company’s engineers discovered Xometry.
“One of the main reasons was your Instant Quoting Engine, which impressed us and helped us a lot,” recalls Stefano Grigis. “The first project with Xometry was a spiraling machine for a big heating mat company. We required aluminium and stainless steel parts to be CNC-machined for the mechanism that allows the heating element to be rolled up. We were concerned that some of the heating vanes could “burn” the excess fabric. In addition, we also made a test with a DMLS 3D printing in stainless steel.”
Ceruti adds that the project Xometry contributed to is one they are most proud of. Through collaboration with Xometry, Asitech was able to quickly source precise prototypes, leading to the development of a new machine that optimised the customer’s process. This innovation resulted in a significant increase in production, doubling the output. The success of the project culminated in a large order for 36 additional units.
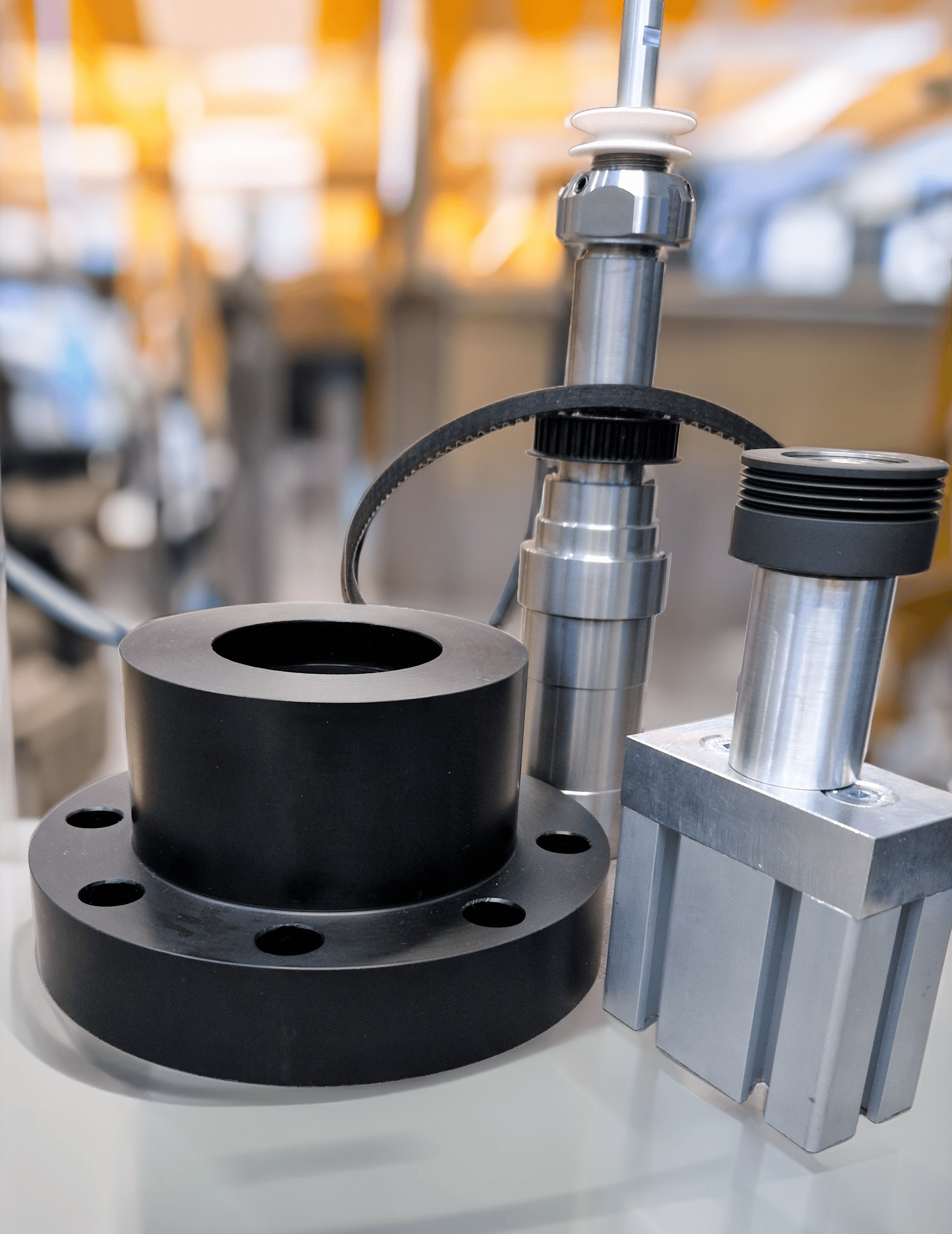
Spiraling machine component asembly
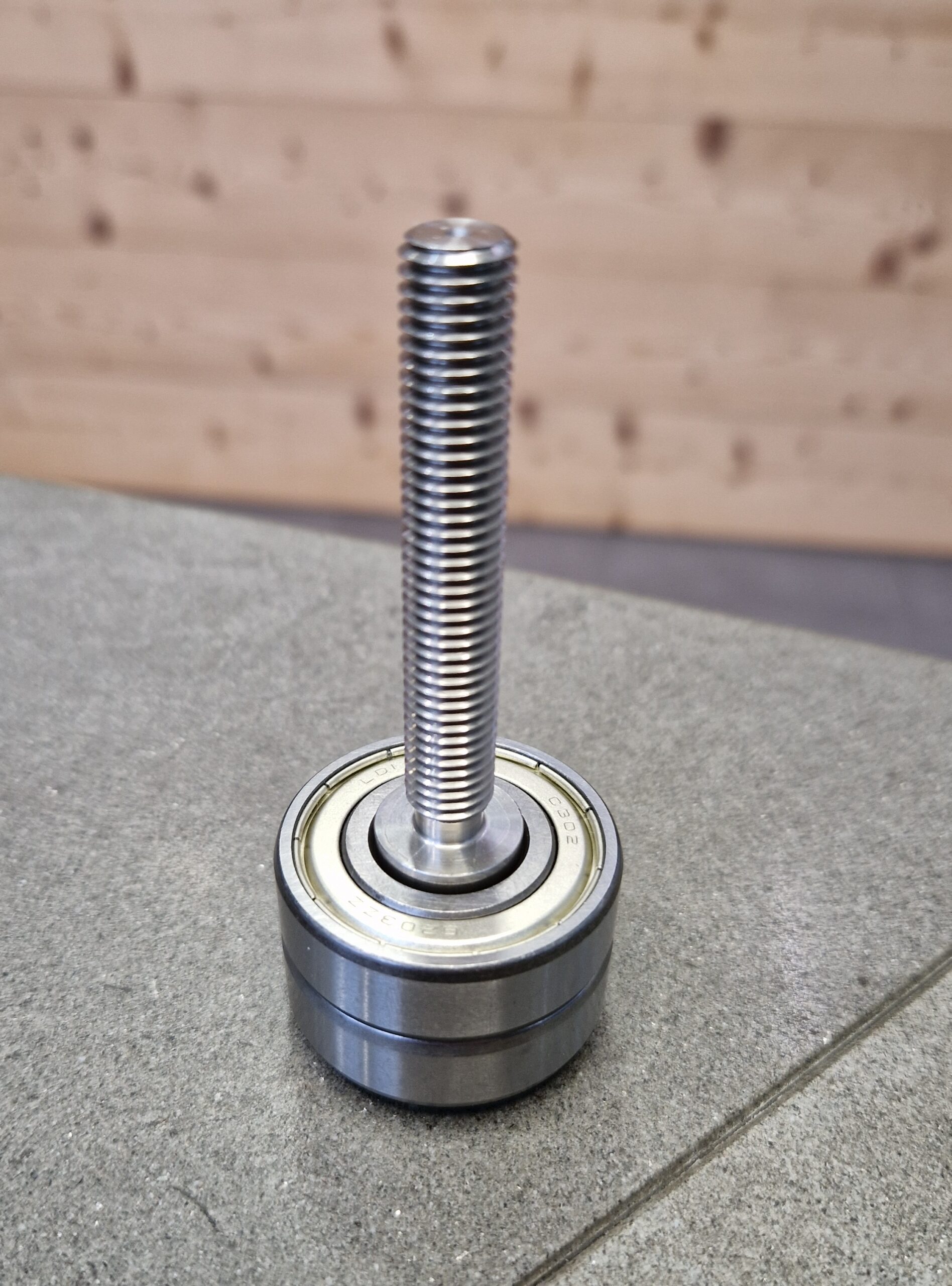
Steel pin for disc brake
In light of these experiences, Grigis emphasises the advantages of our platform: “First of all, we very much appreciated the speed of the platform: in zero time, I can get a quote for 1, 10 or 100 pieces, and test how much it might cost to produce with one material over another, which is crucial in the design phase but also to make realistic proposals for our customers. Then of course the relationship with our dedicated agent, to refine the quote and manage testing with different materials.”
The Future of Asitech
Elena Ceruti shares the company’s vision, “Our work is very much based on customer demands and industry dynamics, so it is always difficult to make projections. In the immediate future, funds related to Industry 4.0 and 5.0 will be a major growth accelerator, so we are confident. For our part, there is a willingness to stay abreast of new industry regulations and to explore the full potential of small batch production to offer increasingly efficient plants.”