Hi everyone! My name is Romain, I’m 22 years old and I am the creator behind RCproto. Ever since I first discovered machining at the age of 10, my passion for machines and mechanics has only grown stronger.
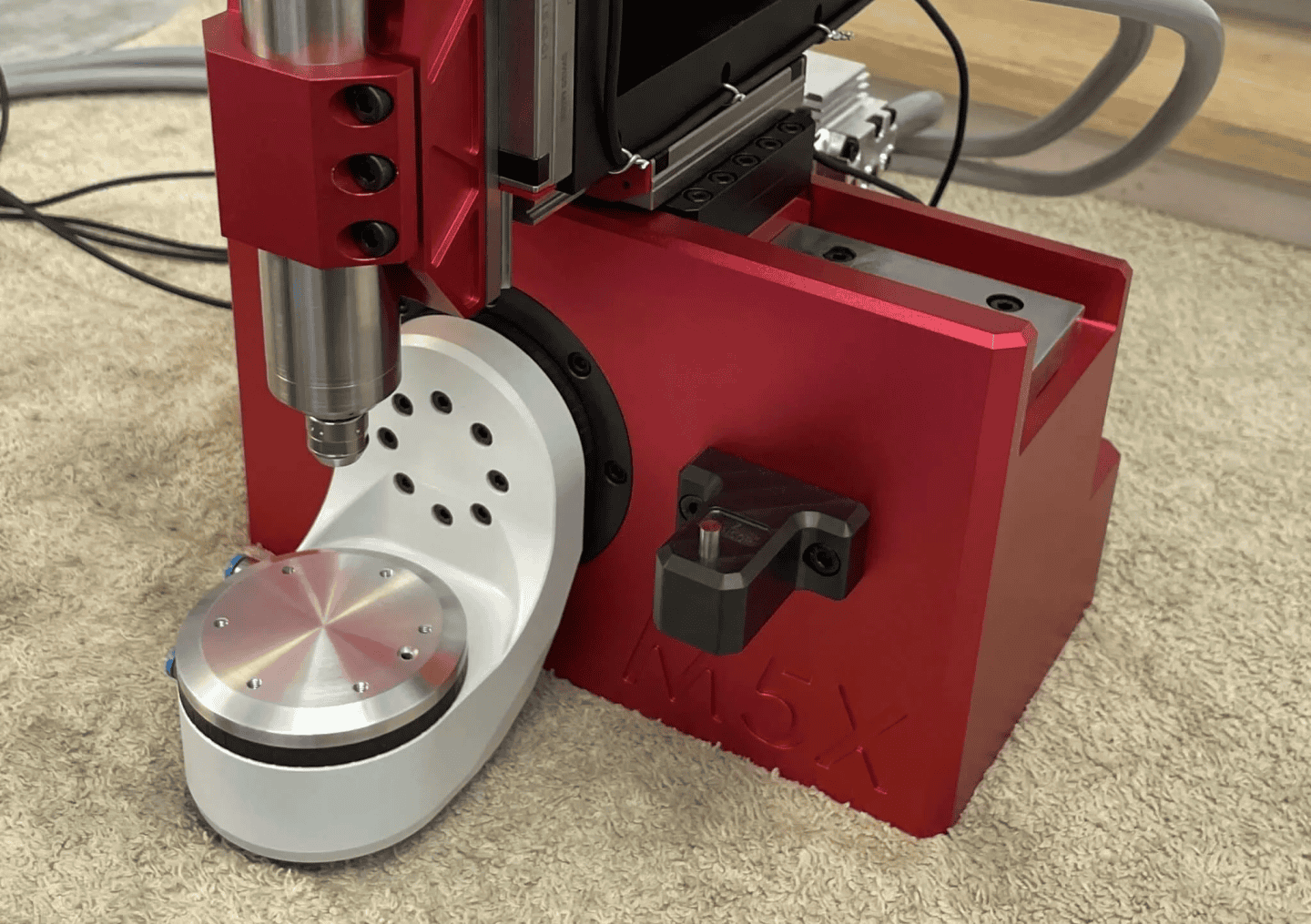
I completed my specialist training in microtechnology and mechanical design in the Arve Valley, a region in the French Alps known for its machining expertise. This training involved the design and machining of mechanical parts, as well as the design and manufacture of tooling for plastic injection, cutting and stamping. Afterwards, I decided to return to my hometown in Limousin to bring my vision to life. That’s how RC proto was born in January 2024.
At RC proto, I focus on machining small prototype mechanical parts in aluminum and engineering plastics (PET, POM, standard PEEK, and HPV PEEK), while continuing my work as a methodologist in the aerospace industry. This project is a dream come true that allows me to combine my love for precision engineering with the joy of designing cutting-edge machines.
My interest in the kinematics and mechanics of machine tools naturally led me to want to create a precision machine. The idea of developing a 5-axis micro-milling machine came to me when I realised that my current machine could not achieve the level of precision needed for certain projects, particularly those requiring tolerances of a few microns. As well as machining prototypes, I have even considered using it as a learning tool to train myself in watchmaking, another passion that I want to explore.
Designing a Compact Machine Without Compromising on Performance
Creating a micro-milling machine came with its fair share of challenges, but I saw each one as an opportunity to innovate. My goal was clear: to design a machine that was not only compact and lightweight (under 20 kilos) but was also capable of achieving total precision. After experimenting with different materials, I found the perfect solution in 5083 aluminum. It’s light, durable, and corrosion-resistant—ideal for both the casing and other key components.
But I wanted more than just performance. I wanted the machine to look just as impressive, so I chose an anodised finish in sleek shades of red, black, and grey. The result? A machine that is as stylish as it is functional.
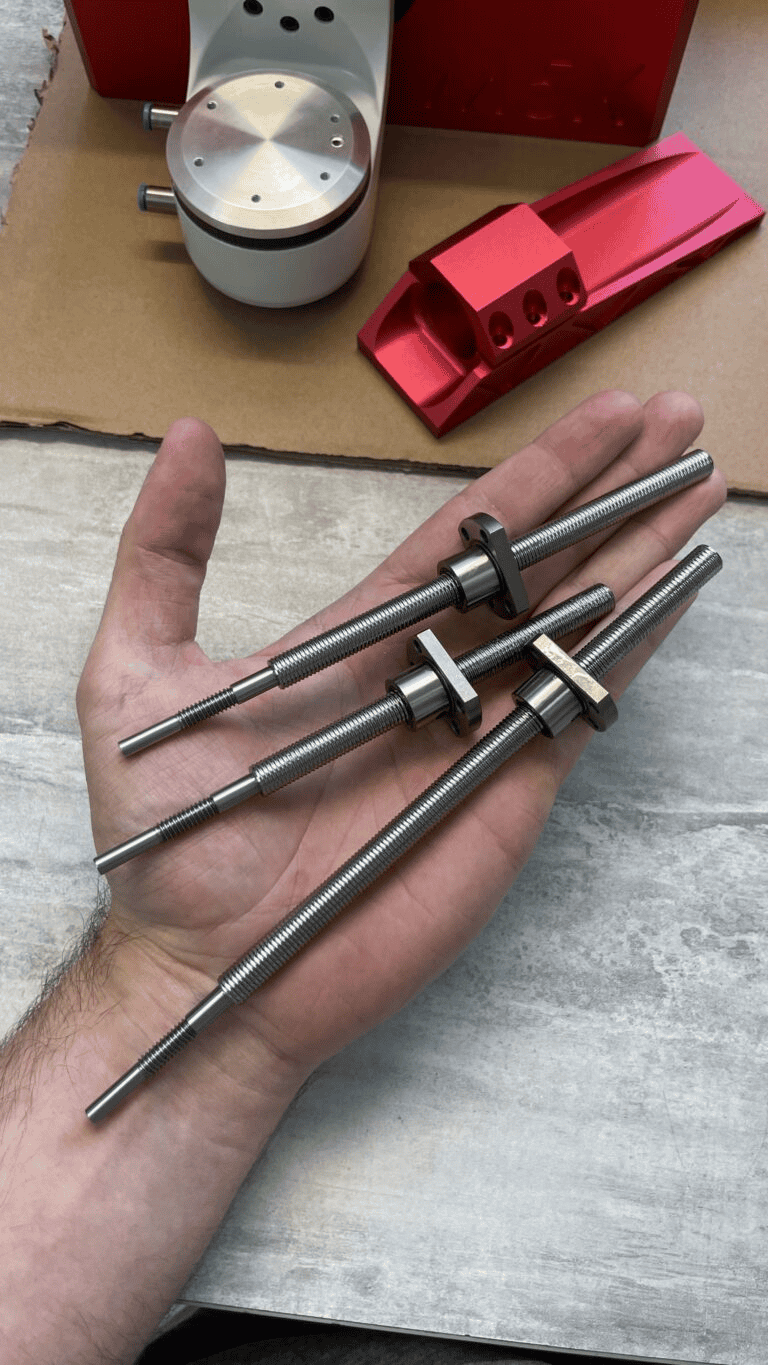
Micro ballscrews
Overcoming Space Constraints With Smart Engineering
One of the toughest challenges was integrating the motors on the Y and Z axes. With space being tight, I had to get creative. The solution? I hollowed out the Y-axis ram to house the motors, a clever design inspired by old manual milling machines, where many mechanical elements were built right into the ram. This approach gave me the compactness I needed. I also opted for a belt drive system to prevent the motors from protruding and adding unnecessary weight. This design choice kept everything streamlined and efficient.
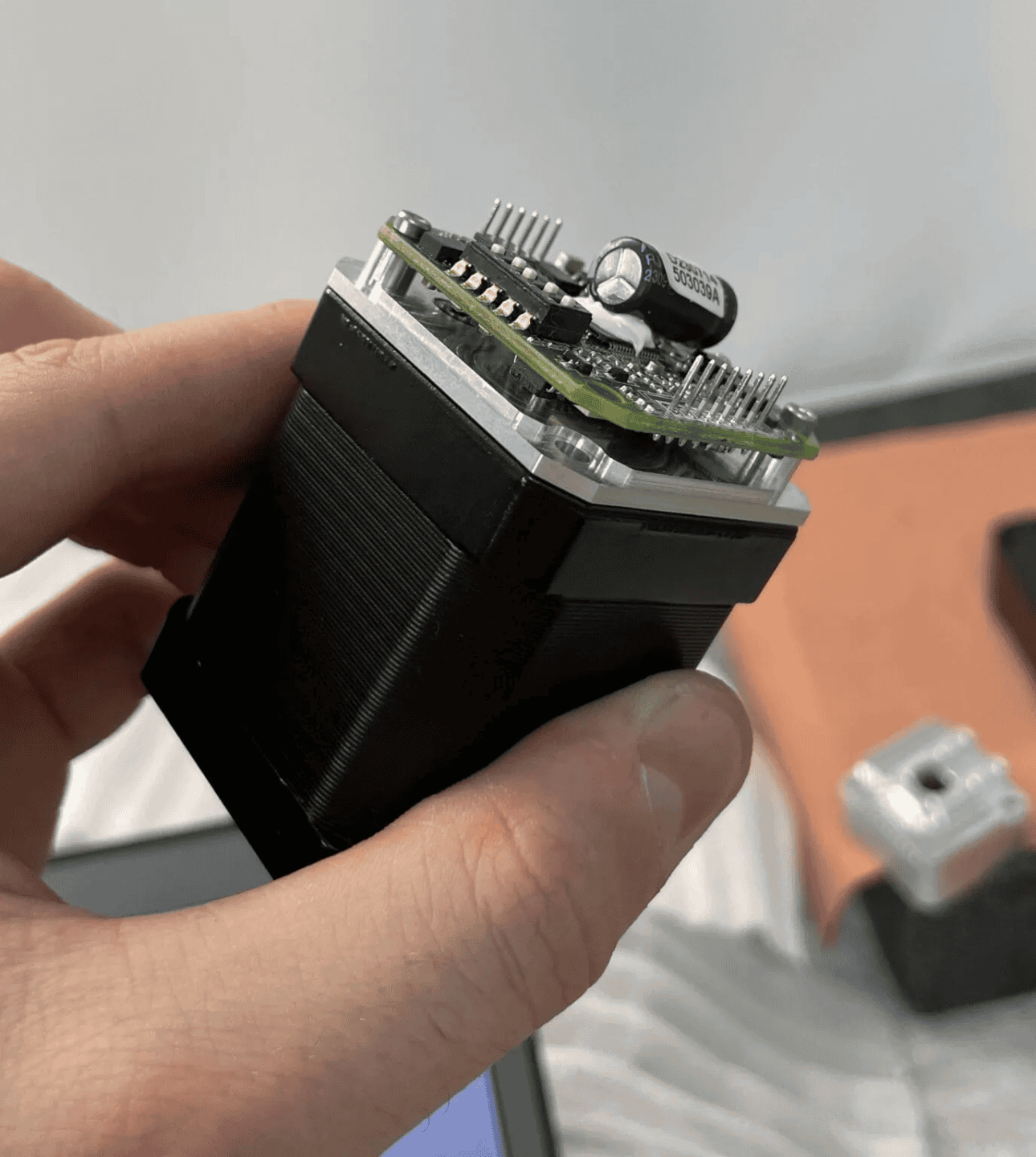
One of the motors of the micro-milling machine
Pushing the Limits of Automation and Precision
I also equipped the machine with a high-speed pneumatic spindle that can reach up to 120,000 RPM. This addition has revolutionised the machine’s capabilities, especially when it comes to speed and precision for small part machining. I also incorporated an automatic tool probe that calibrates each new tool automatically. This innovation significantly reduces errors, particularly when dealing with delicate, small-diameter tools that require extra care.
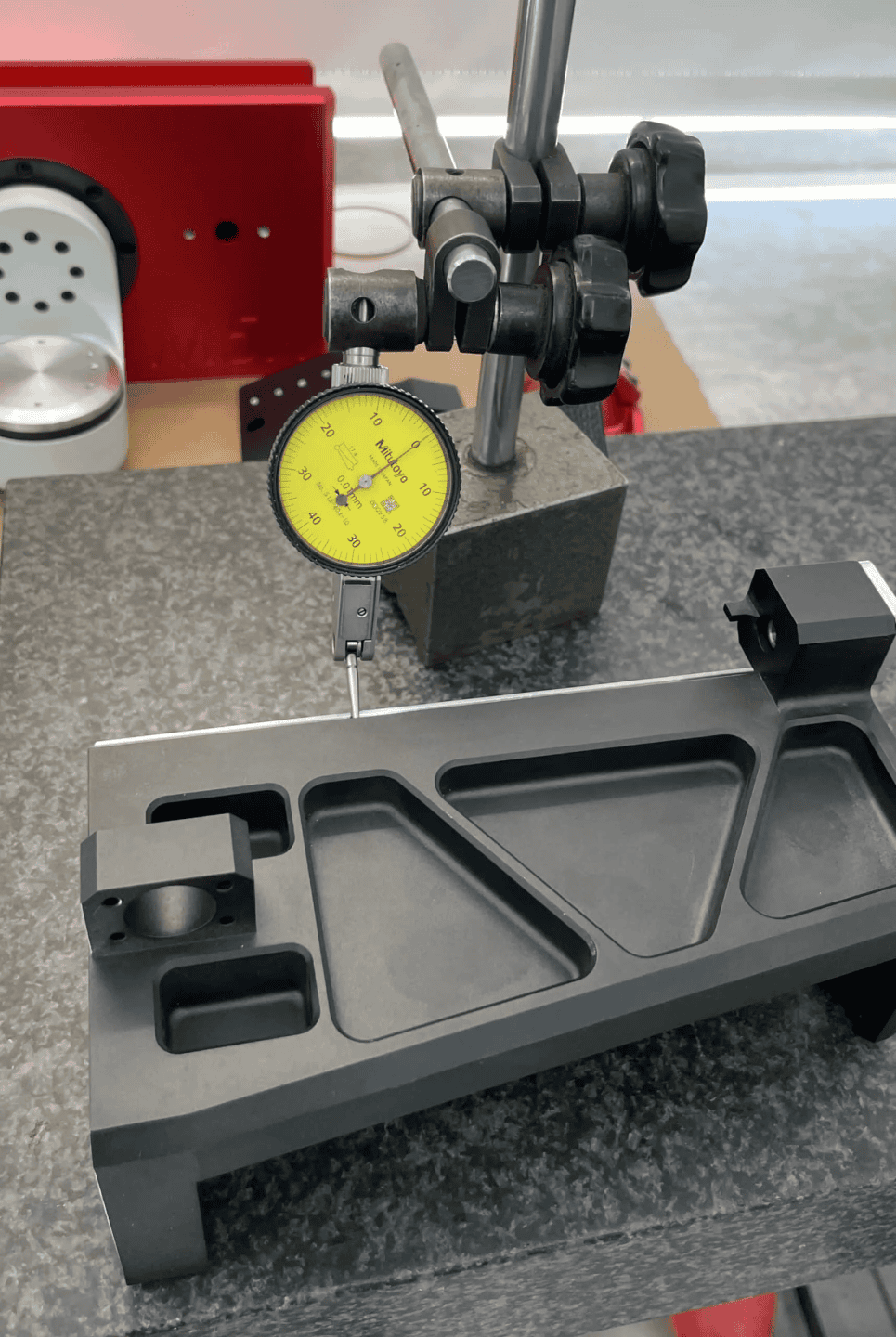
Automatic tool probe of the micro-milling machine
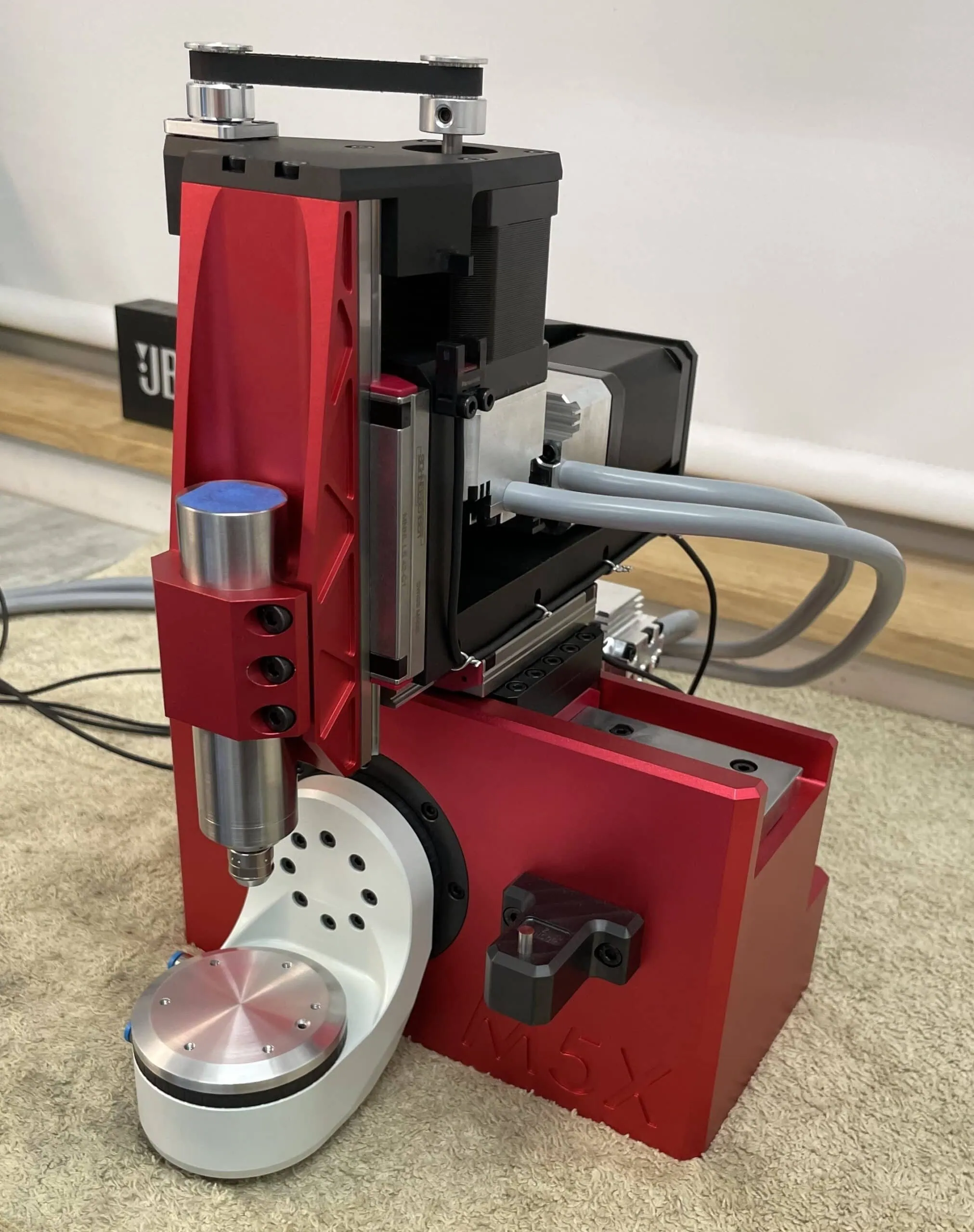
Micro-milling machine
Moving Towards Tests and New Challenges
Now, I’m on the final stretch: fine-tuning the electronics, pneumatics, and machine settings before I begin testing. Every step brings me closer to my vision of a compact, high-performance machine that combines precision with aesthetic appeal. This project has also opened doors to other fields that I am interested in like watchmaking, and I can’t wait to see where it takes me.
But my journey with RC proto doesn’t end here. In 2025, I’m planning to relocate to a new region, driven by the vision to continue pushing the boundaries of mechanical precision. I’m excited to explore new solutions in machining and automation, and the future holds even greater possibilities.
How would you approach designing a compact, high-precision machine like Romain’s? What materials or engineering solutions come to mind? If you’ve ever built or customised a machine, we’d love to hear about your experiences and the challenges you faced!