Injection molding is a method used to manufacture plastic parts at extremely high speeds. Therefore, it is no surprise that injection molding is the first choice of most plastic consumer goods. The material used to manufacture the product using plastic injection molding starts from granular plastic, which is shown below:
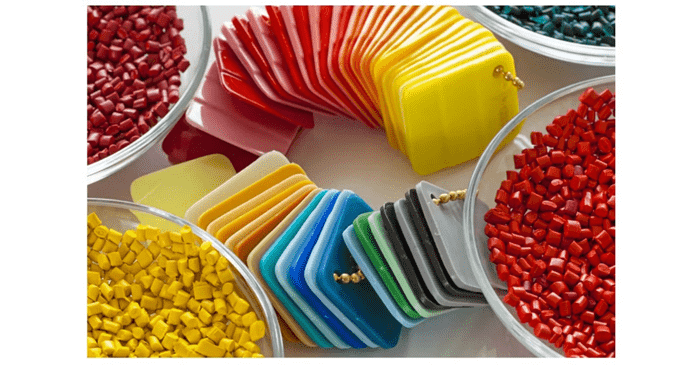
Photo source: Aykut Erdogdu/Shutterstock.com
Injection molds are designed and manufactured specifically for the products being produced. The following diagram illustrates the process of creating a mold.
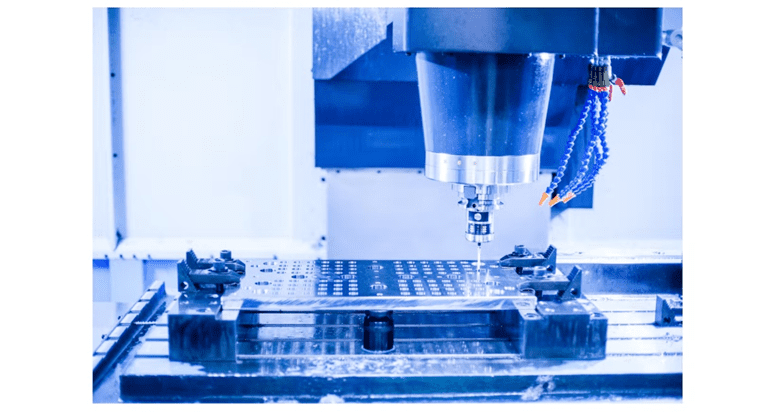
Photo source: Rene H. Kang/Shutterstock.com
Advantages of plastic injection molding include but are not limited to the following contents:
1. Complex part design provided by injection molding
Injection molding can be used to handle highly complex parts, provide consistency and ensure the ability to manufacture millions of nearly identical parts. The effectiveness of high-volume injection molding and better part accuracy and quality mean that key design elements should be considered.
Parts must be designed to maximize the efficiency inherent in mass forming. With ideal designs, parts can be manufactured in high quality without sacrificing complexity.
2. High efficiency and speed of production by injection molding
There are several good reasons why this is the more common and efficient form of molding. First of all, compared with other methods, the injection molding process is faster in operation and has high production yield, making it more efficient.
The processing speed depends on the complexity and size of the mold, but it generally takes only about 15-120 seconds between each molding cycle. Due to the shorter cycles between cycles, more injection molding parts can be produced in given lead time.
3.Greater intensity by injection molding
Over the years, the strength and durability of plastics have improved significantly. Modern lightweight thermoplastics can even withstand harsh environments as well as metal parts. In some cases, they can even exceed metal.
In addition, there are more than 25,000 engineered materials available for complex injection molding applications. High-performance plastic blends and hybrids can also be manufactured to meet specific part requirements and characteristics, such as high tensile strength.
4.Injection molding is more flexible in colors and materials
The plastic injection molding process is flexible, which can be reflected in characteristics of the plastics used as well as the ability of the original equipment manufacturer in its customizing color selection to meet requirements of a particular project. The benefit of plastic injection molding is that it gives original equipment manufacturers freedom to design, especially when they are compared to metal. Many materials can be used.
In the molding process, the desired colors can be obtained by adjusting plastics, additives and biocompatibility so that transparent parts or a variety of colors can be generated. However, when a product requires multiple colors, this can be achieved by encapsulation molding.
5.Less waste during injection molding
Compared with the traditional manufacturing process, the plastic injection molding process only generates a small amount of waste later. Waste plastic usually comes from sprue and runner. However, any unused or discarded plastic can be re-ground and recycled for future use.
6.Lower labor cost by injection molding
The labor cost of injection molding operations is relatively low compared with that of other types of molding processes. Its ability to produce high-level parts at high productivity helps reduce manufacturing costs through their efficiency and effectiveness.
The molded devices are often equipped with automatic pouring and automated process tools to keep operations simple and ensure mass production under less supervision.
7. Various surfaces created by injection molding
Most injection molded parts have a smooth surface finish that is close to the desired appearance. However, the smooth apprentice is not suitable for all applications. Depending on the physical and chemical properties of the plastic material used, the surface finish created by the plastic injection molding manufacturing process does not need a secondary operation. This process ensures flexibility in surface treatment as well as matte surfaces, unique textures and sculpting.
8. Lightweight products produced by injection molding
While they are common in the automotive industry, original equipment manufacturers tend to use lightweight plastic injection molding products in many industries. Compared with metal parts, plastic parts can reduce weight. Today, high-strength, lightweight thermoplastics can replace metal parts as they have little difference in strength or durability. They only have different weights.
9.Many types of plastics can be used in injection molding
Components made of different materials are often needs to design complex parts. Although this may seem simple, it may be complicated to combine plastics. In any case, by guaranteeing compatibility, the plastic expertise of the mold project engineer can reduce the risk of defects, injuries and warranty claims.
10.Consistency can be ensured by injection molding
Producing high-volume but complex plastic parts requires a consistent and repeatable process to achieve a design with tight tolerances. The injection molding production process can ensure consistent quality because the same kind of mold is continuously used in each part and is backed by the continuous improvement practices of the injection molding machine. These practices all combine currently leading technologies.
11.Precision products by injection molding
The proper maintenance of modern high-speed injection mold equipment can allow the mass production of precision molded plastic parts. This molding process is the best choice for the production of plastic parts such as connectors and gears that require high precision production, with the tolerance up to +/-0.0002 inches.
12.Shorter development time by injection molding
Different skill combinations of injection mold engineers can help original equipment manufacturers reduce product development time. Doing so ensures faster production cycles because it can bring defect-free parts to market faster. This is a decisive competitive advantage for manufacturers.
How to make full use of the injection molding process?
In order to make full use of the injection molding process, we need to recognize that there are many details associated with the process and that some changes should be changed to make the process better meet the needs of a given product. Both proper and large-scale production operations all require attention to detail and optimization. This process can reduce the interruption time as much as possible.
Using materials wisely and efficiently is another important skill. Reducing the injection size may provide some help. Experts say that reducing the injection size by 10 percent of the machine's large capacity can ensure the nozzles to paint more colors and check the inspection ring better. Both of these measures an facilitate the management of the later cleaning, which will reduce wasted materials.
The application of right thermoplastics in the application is another way to ensure that your material budget is as tight as possible. Preventive maintenance should not be neglected either. Besides, cleaning the molding equipment is a top priority during regular preventive maintenance.
We should also consider the thickness of the product wall. Uniformity here will help the product cool evenly and reduce the possibility of warping. There are two valuable rules:
- Avoid sharp corners to meet rounded features
- Keep the thickness of each wall at about 40% to 60% of the thickness of the adjacent wall
For more information, please refer to the article on the basics of injection molding.
What type of injection molding technology is more advantageous?
Favorable processes depend on the application of the desired products and materials. Some common examples include cube molding, gas-assisted injection molding, die casting, liquid silicone rubber injection molding, micro-injection molding, thin-wall injection molding, and reaction injection molding. For more information, please refer to the article on the types of plastic molding techniques.
Does injection molding have any shortcomings?
While injection molding has significant advantages, there are several disadvantages.
First, while overall manufacturing costs are lower, this manufacturing process may need high upfront cost, especially when it comes to tools. Therefore, before any parts are produced, prototype parts must be created, which needs time and money to complete and can be costly.
Injection molding is also not applicable for the production of large plastic parts as single pieces due to the size limitations of injection molding machines and molds. Items that are too large for the capacity of the injection molding machine need to be created as multiple parts and joined together in subsequent steps.
Professional designers are also needed to avoid large dents because these can add more expense to the production of the finished products.
Overview
This article summarizes 12 advantages of the injection molding process.
About Xometry
Xometry offers a full range of injection molding capabilities to meet your production needs. Please visit our website to explore our full range of capabilities and contact us to help you solve your injection mold design problems. You can also request a free, no-obligation quote.